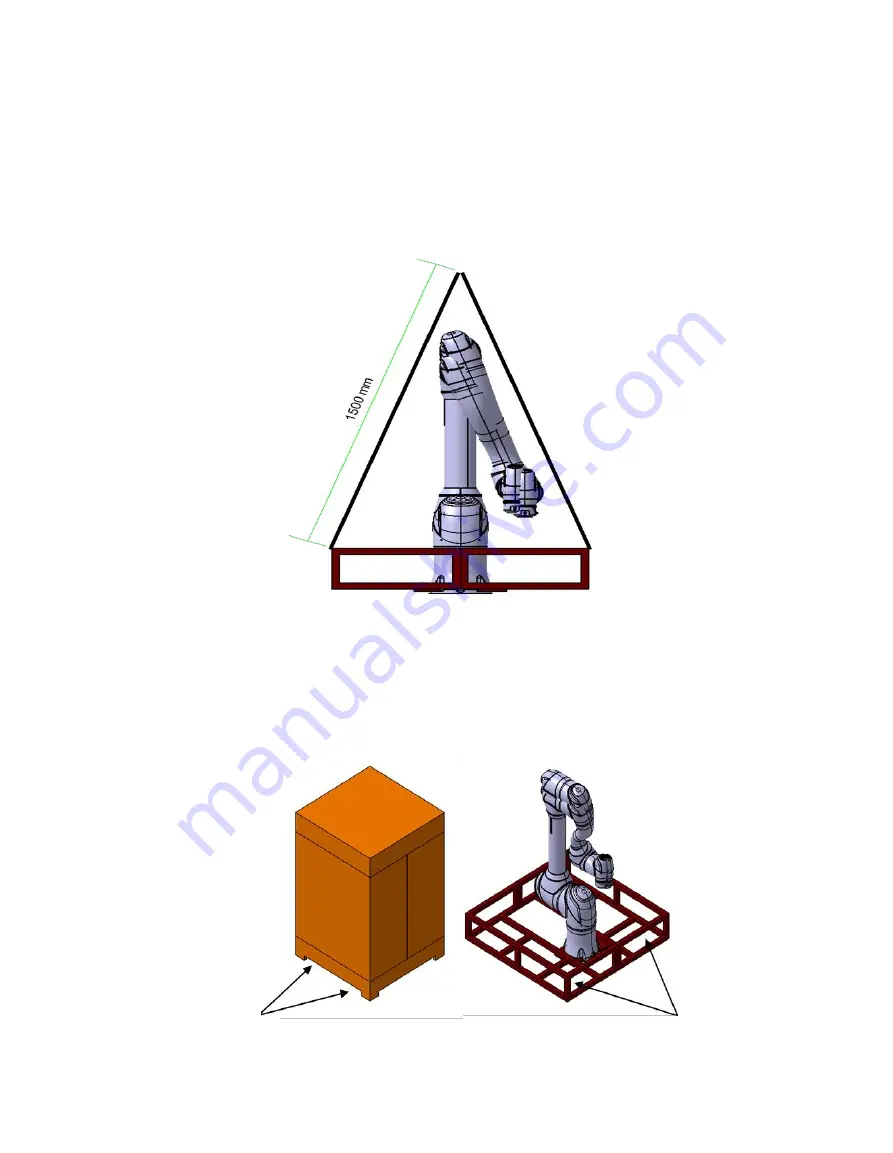
Doosan Robotics Installation Manual v2.1
188
1.
When Using Cranes
◼
The weight of the
robot
is approximately 70 kg. Use wire ropes capable of handling the w
eight of the
robot
.
◼
The length of the wire ropes must be at least 1500 mm, and it is recommended to support
4 points of the
robot
at least.
2.
When Using Forklifts
◼
If the
robot
needs to be relocated in its packaged state, lift the bottom of the package usin
g a forklift.
◼
When installation, relocate the
robot
using the lower packaging materials while taking cautio
n to avoid damage to the
robot
.
Insertion of Forklift
Insertion of Forklift
Содержание H2017
Страница 1: ...1 Manual Version 2 1 Software Version 2 7 1 ...
Страница 9: ...9 E 2 2InstallationEnvironment 178 E 2 3HardwareInstallation 179 Annex F H Series Handling Guide 186 ...
Страница 29: ...29 2 5 3 Robot operating space M0609 ...
Страница 30: ...Doosan Robotics Installation Manual v2 1 30 ...
Страница 31: ...31 M0617 ...
Страница 32: ...Doosan Robotics Installation Manual v2 1 32 ...
Страница 33: ...33 M1013 ...
Страница 34: ...Doosan Robotics Installation Manual v2 1 34 ...
Страница 35: ...35 M1509 ...
Страница 36: ...Doosan Robotics Installation Manual v2 1 36 ...
Страница 37: ...37 H2017 ...
Страница 38: ...Doosan Robotics Installation Manual v2 1 38 ...
Страница 39: ...39 H2515 ...
Страница 40: ...Doosan Robotics Installation Manual v2 1 40 ...
Страница 42: ...Doosan Robotics Installation Manual v2 1 42 M1013 M1509 ...
Страница 119: ...119 B 2 Europe Machinery Directive Attestation of Conformity ...
Страница 120: ...Doosan Robotics Installation Manual v2 1 120 ...
Страница 121: ...121 B 3 Europe EMC Directive Attestation of Conformity ...
Страница 122: ...Doosan Robotics Installation Manual v2 1 122 B 4 U S NRTL Certification U S CANADA ...
Страница 123: ...123 ...
Страница 124: ...Doosan Robotics Installation Manual v2 1 124 B 5 Functional Safety Certification ...
Страница 125: ...125 B 6 Voluntary Safety Confirmation Declaration KCs ...
Страница 126: ...Doosan Robotics Installation Manual v2 1 126 ...
Страница 127: ...127 ...
Страница 128: ...Doosan Robotics Installation Manual v2 1 128 ...
Страница 129: ...129 ...
Страница 130: ...Doosan Robotics Installation Manual v2 1 130 ...
Страница 161: ...161 D 1 3 Nameplate and Label ...
Страница 176: ...Doosan Robotics Installation Manual v2 1 176 E 1 3 Nameplate and Label ...
Страница 190: ...Doosan Robotics Installation Manual v2 1 190 ...