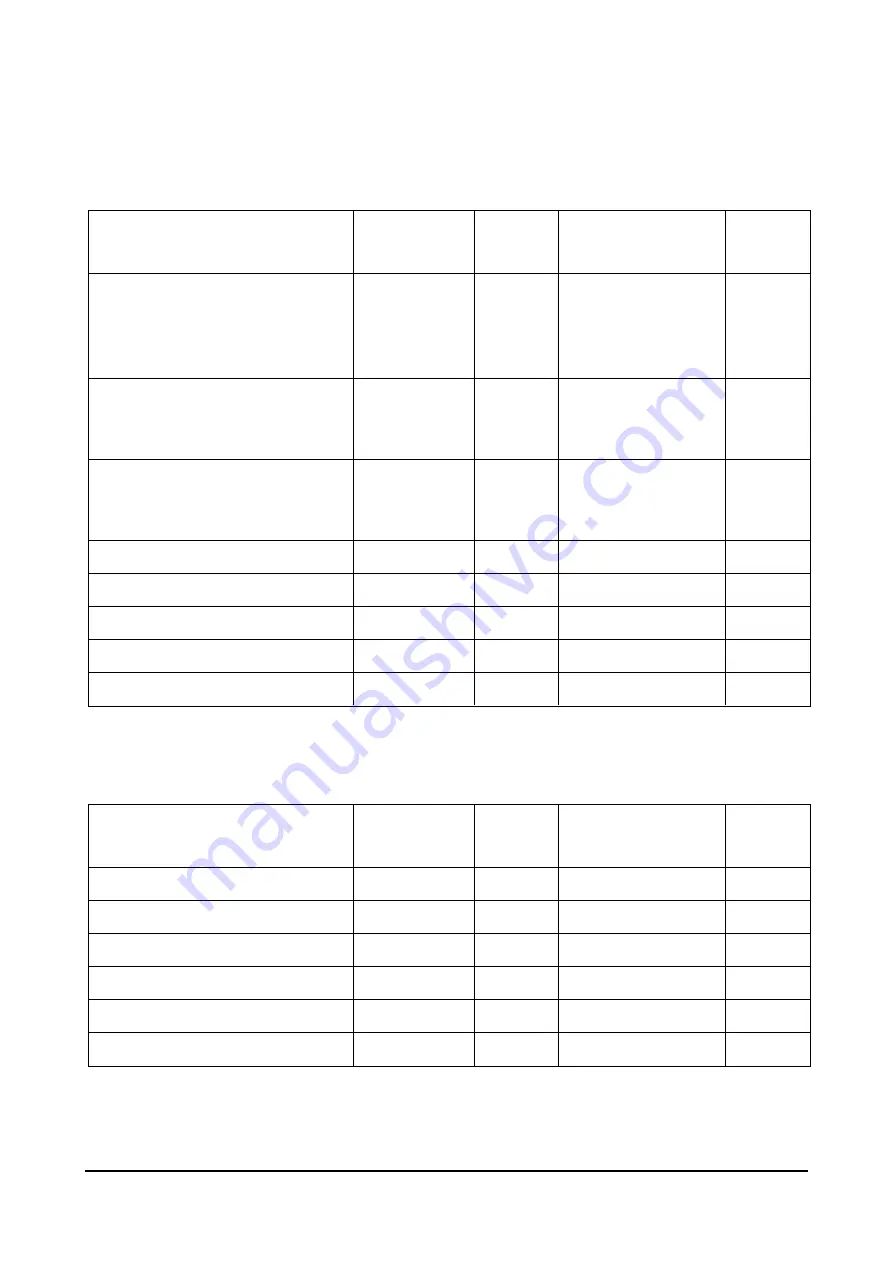
DE08TS Diesel Engines
Appendix
Appendix
1. Tightening torque for major parts
2. Tightening torque for fuel injection pump system
98
M
ajor Parts
Screw
Strength
Tightening Torque
Remarks
(Diameter x pitch)
(grade)
1st : 6.0 kg
•
m
Cylinder head bolt
M14
B
1.5
10.9T
2nd : 180°
3rd : 150°
(Angle method)
1st : 10 kg
•
m
Connecting rod bearing cap bolt
M14
B
1.5
12.9T
2nd : 15 kg
•
m
3rd : 18 kg
•
m
1st : 15 kg
•
m
Crankshaft main bearing cap bolt
M16
B
1.5
12.9T
2nd : 25 kg
•
m
3rd : 30 kg
•
m
Balance weight fixing bolt
M12
B
1.5
10.9T
9.0 kg
•
m
Flywheel housing fixing bolt
M14
B
1.5
10.9T
8.0 kg
•
m
Flywheel fixing bolt
M14
B
1.5
10.9T
21.5 kg
•
m
Crankshaft pulley fixing bolt
M12
B
1.5
10.9T
13.4 kg
•
m
Oil spray nozzle
M14
B
1.5
-
7.0 kg
•
m
M
ajor Parts
Screw
Strength
Tightening Torque
Remarks
(Diameter x pitch)
(grade)
Injection nozzle nut
M28
B
1.5
-
7.0
L
0.5 kg
•
m
Injection pump bracket bolt
M10
8.8T
4.4 kg
•
m
Injection pump coupling bolt
-
-
6.0 ~ 6.5 kg
•
m
Injection pump driving gear nut
M24
B
1.5
8.8T
25.0 kg
•
m
Injection pipe nut
M14
B
1.5
8.8T
3.0 kg
•
m
Injection pump delivery valve holder
-
-
11.0 ~ 12.0 kg
•
m