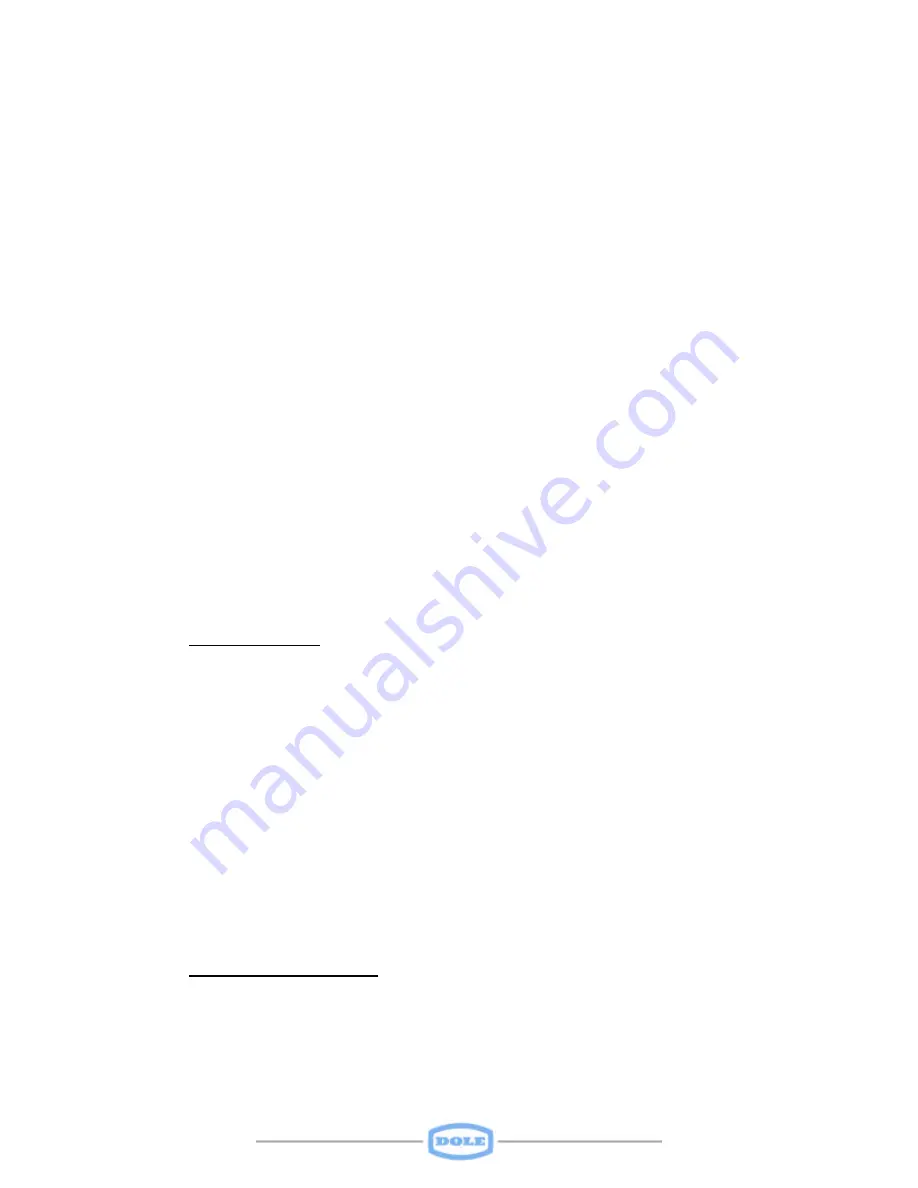
16
the “COMPRESSOR” switch has been in the “OFF” position for more than
a day, observe the following:
CAUTION:
Do not operate the compressor until electrical power has been supplied to
the freezer for a period of at least FOUR hours. The crankcase heater
requires power for at least four hours to evaporate any liquid refrigerant
that may have migrated since the unit had been shut down.
Do not operate the compressor before all five service valves (six on
shipboard models) have been opened.
Do not operate compressor before the cooling water has been connected
and turned on to the condenser.
The “OPERATING MODE” switch, which will be in the “FREEZE” position
during the refrigerating mode, should be placed in the “PUMP DOWN”
position if it is desired to pump down the system after, or between,
freezing cycles. Placing the switch in the “PUMP DOWN” position results
in the closing of the liquid solenoid valve (LSV1), thereby preventing liquid
from flowing to the plates. With the “OPERATING MODE” switch in the
“PUMP DOWN” position, the compressor will cycle between the preset
cutout/cut in suction pressures.
6. Product Loading
The freezer should be ready for product loading one hour after
compressor startup. The “HYDRAULICS” switch should be placed in the
“DOWN” position to increase the space between plates. Product
packages or trays may then be placed in the freezer.
The product should be loaded uniformly on each plate. DO NOT partially
load a plate.
For most effective freezing, all stations should be loaded with product. If a
station(s) is to be empty during freezing due to the lack of enough product
to fill all stations, the empty station(s) should be located ABOVE all
stations loaded with product. For efficient freezing, plates should be kept
free of frost.
7. Liquid Refrigerant Level
Check the liquid level in the surge drum AFTER THE COMPRESSOR
HAS BEEN IN OPERATION FOR TWO HOURS. The liquid le vel should
stabilize at the centerline of the sight glass.