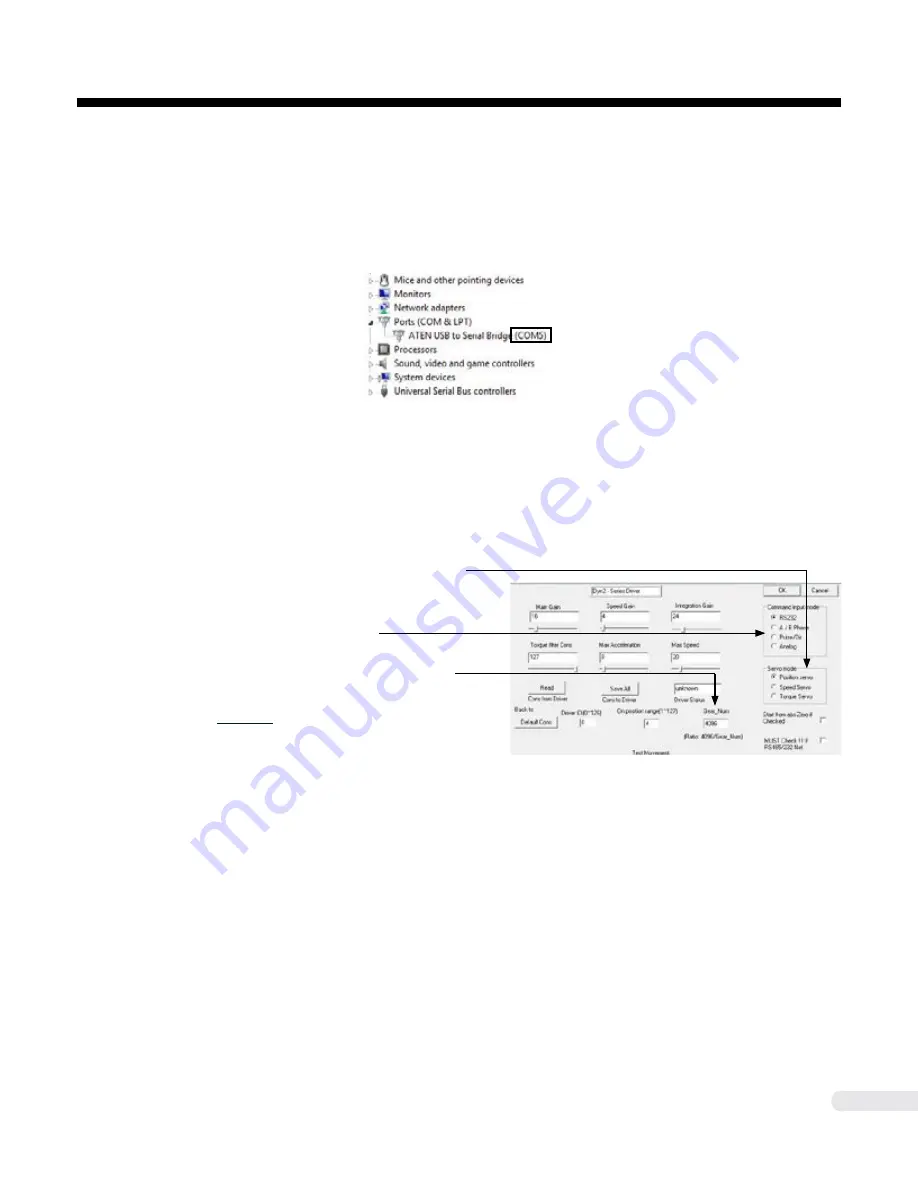
66
DYN2MS-02F-0116A17
APPENDIX B - Operation Examples
█
Position Servo Mode - Ball Screw
1. Connect encoder feedback and motor power cable from servo drive to servo motor.
2. Connect RS232 tuning cable from servo drive JP2 to controller PC.
3. Power ON servo drive.
4. Open Windows Device Manager - Locate COM Port Number of RS232 tuning cable.
5. Open DMMDRV program.
6. Select COMSET --> COM PORT. Press “Change Port“ until RS232 tuning cable COM
port number selected. Press “ok“.
7. Select ServoSetting --> DYN2-DRIVER.
Setting drive parameters and mode
main screen
will open.
8. Press “Read” to read out the factory default or current setting of the servo drive. At any
time, pressing “Save All“ will save the parameters into the servo drive.
9. Under Servo Mode, select “Position Servo”.
10. Under command input mode, select “Pulse/Dir”,
“A/B Phase”, or “CW/CCW”.
11. Set GEAR_NUM parameter according to
ball screw pitch and target travel speed.
Example:
Ball screw pitch = 10mm
Reduction = 2:1
Target Speed = 15m/min
Rated Motor Speed = 3,000rpm = 50rev/s
Controller Pulse Output Frequency = 100kHz = 100,000pulse/s
3,000rpm / 2 = 1,500rpm after reduction
1,500rpm * 10mm = 15,000mm/min = 15m/min
100,000pulse/s / 50rev/s = 2,000pulse/rev
2,000pulse/rev / 4 = 500
GEAR_NUM = 500
12. Tune Gain and OnPosition Range according to machine and operation requirements.
13. Click “Save All“ when finished adjustments.
14. The servo drive is ready to accept position pulse commands.