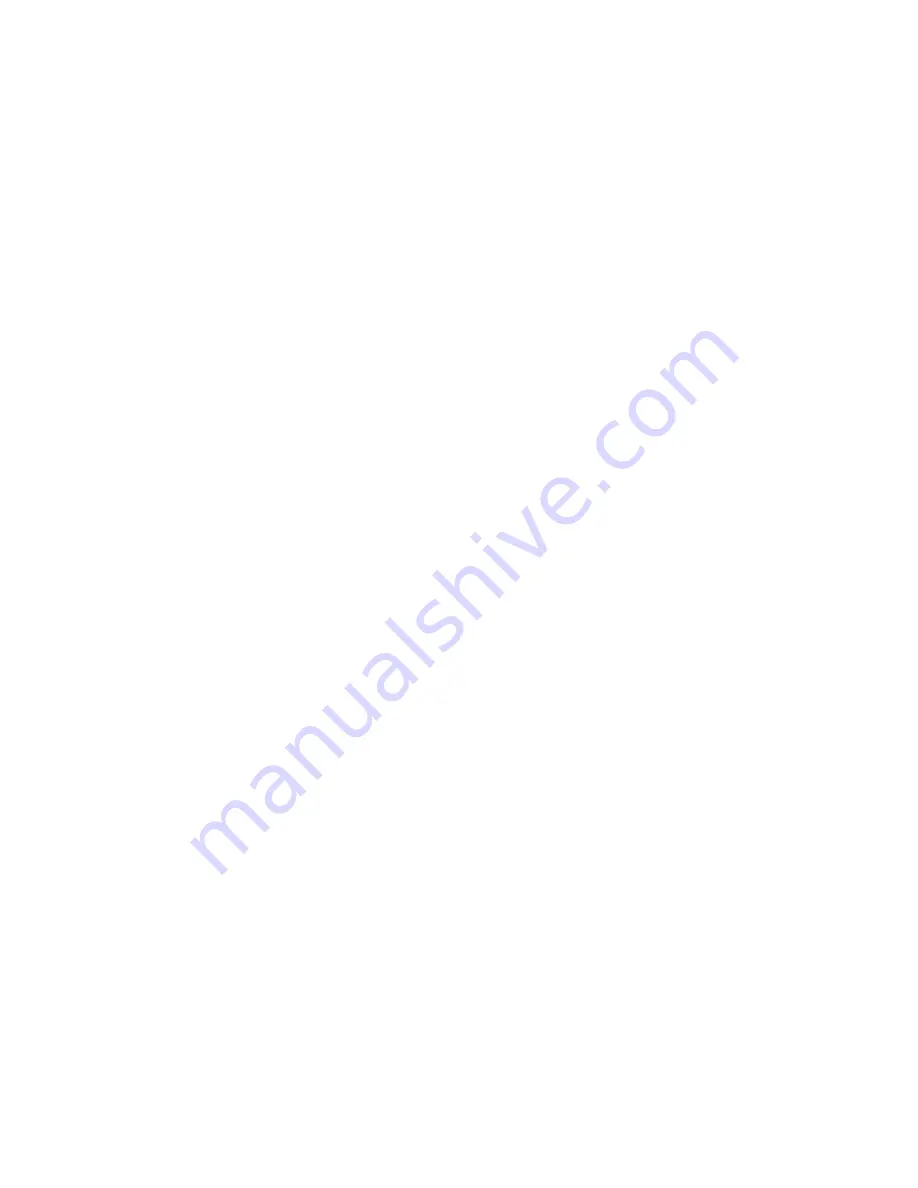
STANDARD PRODUCT WARRANTY
SYSTEMS, INC. warrants that its products will be free from defects in design, materials and workmanship
for a period of one (1) year from the date of shipment. All claims for breach of this warranty must be
made within 30 days after the defect is or can with reasonable care, be detected. In no event shall any
claim be made more than 30 days after this warranty has expired. In order to be entitled to the benefits
of this warranty, the product must have been properly installed, maintained and operated in accordance
with all manufacturer’s recommendations and/or specified design parameters and not otherwise
have been subject to abuse, misuse, misapplication, acts of nature, overloading, unauthorized repair
or modification, application in a corrosive environment or lack of maintenance. Periodic lubrication,
adjustment and inspection in accordance with all manufacturers’ recommendations are the sole
responsibility of the Owner/User.
In the event of a defect, as determined by SYSTEMS INC., covered by this warranty, SYSTEMS INC.
shall remedy such defect by repairing or replacing any defective equipment or parts, bearing the cost
for the parts, labor and transportation. This shall be exclusive remedy for all claims whether based on
contract, negligence or strict liability.
WARRANTY LIMITATIONS
THE ABOVE WARRANTIES ARE IN LIEU OF ANY OTHER WARRANTIES, WHETHER EXPRESSED
OR IMPLIED, INCLUDING BUT NOT LIMITED TO ANY IMPLIED WARRANTY OF MERCHANTABILITY
OR FITNESS FOR A PARTICULAR PURPOSE. SYSTEMS INC. AND ITS SUBSIDIARIES SHALL
NOT IN ANY EVENT BE LIABLE TO ANYONE, INCLUDING THIRD PARTIES, FOR INCIDENTAL,
CONSEQUENTIAL OR SPECIAL DAMAGES OF ANY KIND INCLUDING BUT NOT LIMITED TO,
BREACH OF WARRANTY, LOSS OF USE, LOSS OF PROFIT, INTERRUPTION OF BUSINESS OR
LOSS OF GOODWILL.