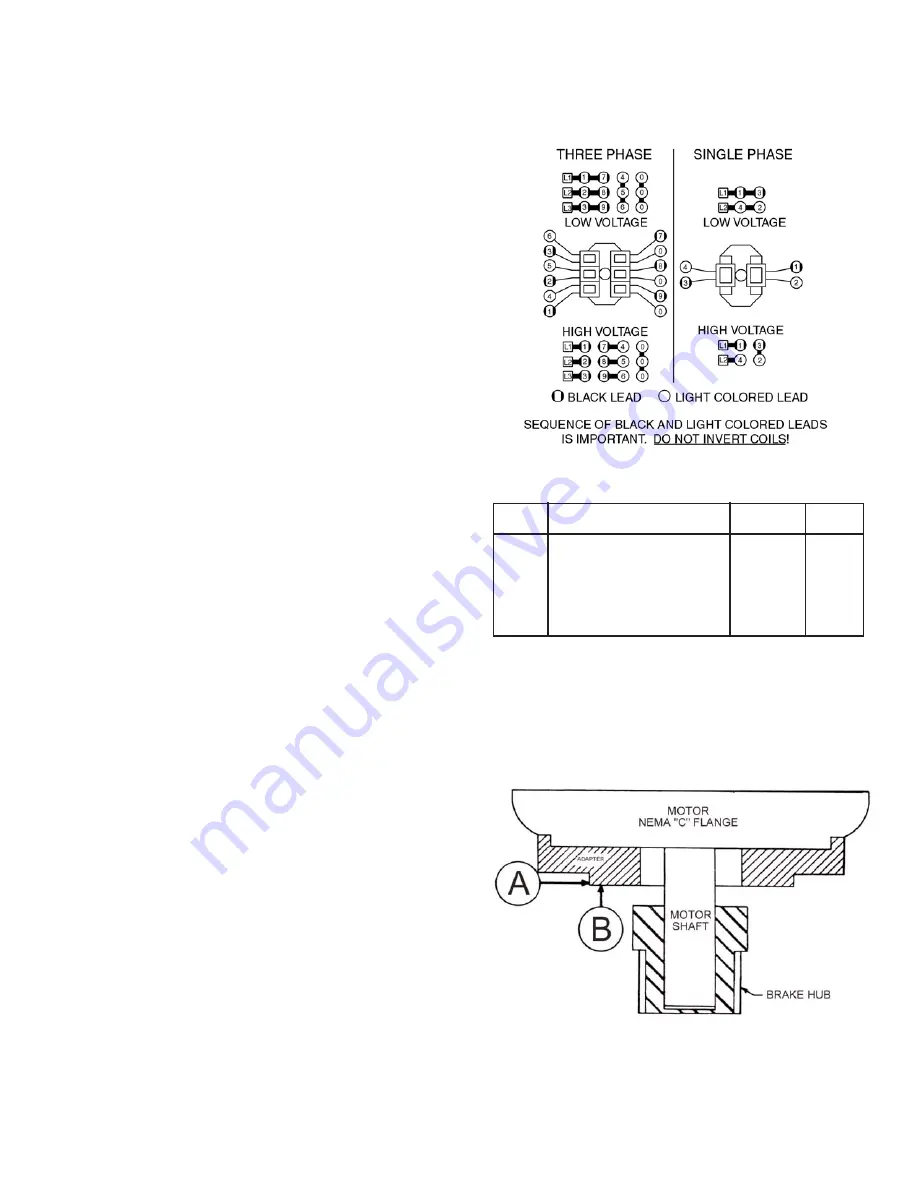
INSTALLATION OF BRAKE ON MOTOR
ENDSHIELD (See Figures 2, 3 and Table 4)
Do not operate manual release or energize brake coil before
installation in order to preserve pre-alignment of rotating disc
for easy installation of brake to motor.
Because of the close fit on all joints (bracket, cover, hub), care
should be taken to prevent damage to all machined surfaces.
Do not operate brake in hazardous location with cover removed.
All testing must be done in a non-explosive atmosphere.
1.
Remove hub (14) from brake and mount hub with key (not
supplied by Dings) on motor shaft per dimension “BC” shown
in Figure 2. Be sure that hub used is item supplied by Dings
for hazardous location applications. Tighten both set screws to
8-10 lb. ft. torque.
2.
Remove four cover bolts (21) and tap cover with soft mallet.
Remove cover (1). Do not operate the manual release (17)
until brake is installed.
3.
Inspect motor “C” flange and remove any nicks or burrs. This
will assure a precision fit of brake to motor flange. Slide
brake over hub (14), engaging teeth of rotating disc (10) and
hub.
4.
Install four mounting bolts (15) and tighten. Install four
locking set screws (16) and tighten to 40 lb. ft. torque. This
seals flame path around mounting bolts. Check rotation of hub
to make certain it does not rub in bracket (13). Diametrical
clearance or hub outside diameter to bracket bore shall not
exceed .024”.
5.
Connect brake leads to power as shown in Figure 3. All
wiring should be positioned to prevent pinching or chafing
and all connections well taped to prevent grounding.
6.
Replace cover (1). This may be done more easily by threading
a 3/8” dia. by 5” long stud (threaded one end 3/8-16NC) into
one cover bolt hole in magnet plate assembly (3) as guide.
Slide cover into position using stud as a guide and tap with
soft mallet until cover seats. Use care in assembly. Insert 3
cover bolts (21) and finger tighten. Remove guide stud and
insert fourth cover bolt. Draw up all bolts evenly and tighten
until spring washer (22) is fully compressed. A loose or
missing bolt will render the brake unsafe for operation in
hazardous locations.
INSTALLATION OF BRAKE WITH ADAPTER
ON MOTOR ENDSHIELD (See Figure 4)
7.
Inspect motor “C” flange and remove any nicks or burrs. This
will insure a precision fit of adapter to the motor flange.
Mount adapter to motor flange using the four bolts and lock
washers supplied. A soft mallet may be used to tap adapter
into place. All bolts should be drawn up evenly and tight.
8.
Check alignment or adapter. Clamp dial indicator to brake
hub (position A) and measure pilot eccentricity. This must
not exceed .006” total indicator reading for a full revolution
of hub. Reposition dial indicator (position B) and check
adapter face runout which must not exceed .006” total
indicator reading a full revolution of the shaft. Remove hub
(14) from brake and mount hub with key (not supplied by
Dings) on motor shaft per dimension shown in Figure 2.
Tighten both setscrews to 8-10 lb. ft. torque. Complete
mounting of brake per paragraphs 2 through 6.
Figure 2. Wiring Connections
Figure 3. Adapter Installation
ITEM
PART
NO.
NO.
DESCRIPTION
NO.
REQ.
3
Magnet assembly with coils
--
1
26
Magnet coil
(3 phase)
H070033
6
26A
“ “
(1 phase)
H070035
2
27
Insulating washer (3 phase)
G070037
4
27A
“ “ (1 phase)
G070029
4
51
Shading coil (1 phase only)
G070032
2
Table 2. Electrical Parts List
5