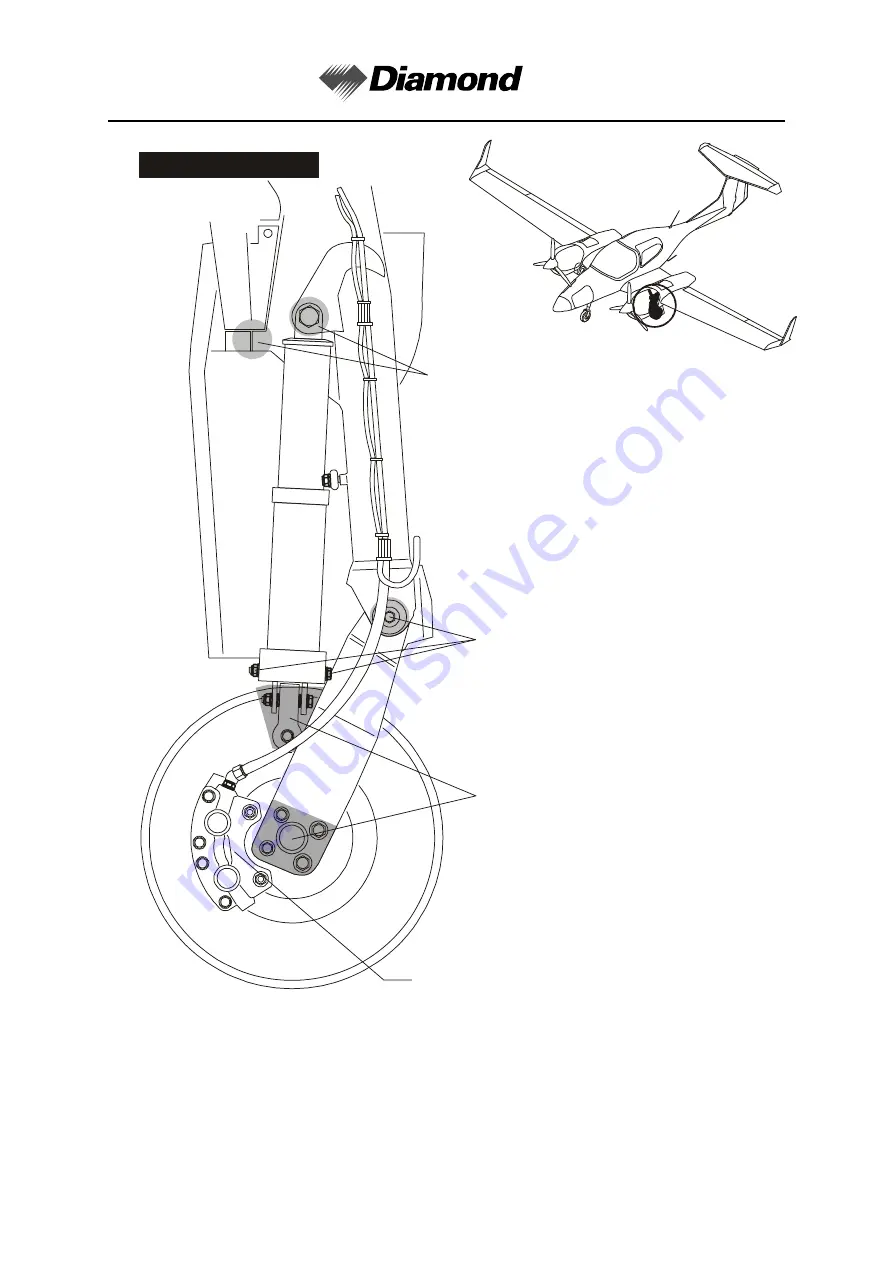
AIRCRAFT
Servicing - General
DA 42 NG AMM
Page 10
15 Mar 2018
12-30-00
Doc # 7.02.15
Rev. 4
Coating with Preventives according to
Section 12-30 of this AMM
Keep Caliper, Brake Disc and
Tyre free of Preventives
LH Shown, RH Similar
Coating with Preventives according to
Section 12-30 of this AMM
Coating with Preventives according to
Section 12-30 of this AMM
Figure 4: Anti-Corrosion Coating - Main Landing Gear LH/RH (2)
Содержание DA 42 NG
Страница 41: ...AIRCRAFT DA 42 NG AMM Introduction Doc 7 02 15 Rev 4 01 TITLE Page 1 15 Mar 2018 CHAPTER 01 INTRODUCTION ...
Страница 42: ...AIRCRAFT Introduction DA 42 NG AMM Page 2 15 Mar 2018 01 TITLE Doc 7 02 15 Rev 4 Intentionally left blank ...
Страница 44: ...AIRCRAFT Introduction DA 42 NG AMM Page 2 15 Mar 2018 01 CONTENTS Doc 7 02 15 Rev 4 Intentionally left blank ...
Страница 234: ...AIRCRAFT Dimensions and Areas DA 42 NG AMM Page 2 15 Mar 2018 06 TITLE Doc 7 02 15 Rev 4 Intentionally left blank ...
Страница 236: ...AIRCRAFT Dimensions and Areas DA 42 NG AMM Page 2 15 Mar 2018 06 CONTENTS Doc 7 02 15 Rev 4 Intentionally left blank ...
Страница 252: ...AIRCRAFT Dimensions and Areas DA 42 NG AMM Page 16 15 Mar 2018 06 00 00 Doc 7 02 15 Rev 4 Intentionally left blank ...
Страница 266: ...AIRCRAFT Leveling and Weighing DA 42 NG AMM Page 2 15 Mar 2018 08 TITLE Doc 7 02 15 Rev 4 Intentionally left blank ...
Страница 268: ...AIRCRAFT Leveling and Weighing DA 42 NG AMM Page 2 15 Mar 2018 08 CONTENTS Doc 7 02 15 Rev 4 Intentionally left blank ...
Страница 270: ...AIRCRAFT Leveling and Weighing DA 42 NG AMM Page 2 15 Mar 2018 08 00 00 Doc 7 02 15 Rev 4 Intentionally left blank ...
Страница 282: ...AIRCRAFT Leveling and Weighing DA 42 NG AMM Page 4 15 Mar 2018 08 20 00 Doc 7 02 15 Rev 4 Intentionally left blank ...
Страница 284: ...AIRCRAFT Towing and Taxiing General DA 42 NG AMM Page 2 15 Mar 2018 09 TITLE Doc 7 02 15 Rev 4 Intentionally left blank ...
Страница 288: ...AIRCRAFT Towing and Taxiing General DA 42 NG AMM Page 2 15 Mar 2018 09 00 00 Doc 7 02 15 Rev 4 Intentionally left blank ...
Страница 292: ...AIRCRAFT Towing and Taxiing General DA 42 NG AMM Page 4 15 Mar 2018 09 10 00 Doc 7 02 15 Rev 4 Intentionally left blank ...
Страница 296: ...AIRCRAFT Towing and Taxiing General DA 42 NG AMM Page 4 15 Mar 2018 09 20 00 Doc 7 02 15 Rev 4 Intentionally left blank ...
Страница 314: ...AIRCRAFT Placards and Markings DA 42 NG AMM Page 2 15 Mar 2018 11 TITLE Doc 7 02 15 Rev 4 Intentionally left blank ...
Страница 316: ...AIRCRAFT Placards and Markings DA 42 NG AMM Page 2 15 Mar 2018 11 CONTENTS Doc 7 02 15 Rev 4 Intentionally left blank ...
Страница 324: ...AIRCRAFT Placards and Markings DA 42 NG AMM Page 204 15 Mar 2018 11 20 00 Doc 7 02 15 Rev 4 Intentionally left blank ...
Страница 332: ...AIRCRAFT Placards and Markings DA 42 NG AMM Page 8 15 Mar 2018 11 30 00 Doc 7 02 15 Rev 4 Intentionally left blank ...
Страница 335: ...AIRCRAFT DA 42 NG AMM Servicing General Doc 7 02 15 Rev 4 12 TITLE Page 1 05 May 2016 CHAPTER 12 SERVICING GENERAL ...
Страница 336: ...AIRCRAFT Servicing General DA 42 NG AMM Page 2 15 Mar 2018 12 TITLE Doc 7 02 15 Rev 4 Intentionally left blank ...
Страница 338: ...AIRCRAFT Servicing General DA 42 NG AMM Page 2 15 Mar 2018 12 CONTENTS Doc 7 02 15 Rev 4 Intentionally left blank ...
Страница 340: ...AIRCRAFT Servicing General DA 42 NG AMM Page 2 15 Mar 2018 12 00 00 Doc 7 02 15 Rev 4 Intentionally left blank ...
Страница 360: ...AIRCRAFT Servicing General DA 42 NG AMM Page 20 15 Mar 2018 12 10 00 Doc 7 02 15 Rev 4 Intentionally left blank ...
Страница 389: ...AIRCRAFT DA 42 NG AMM Standard Practices Doc 7 02 15 Rev 4 20 TITLE Page 1 15 Mar 2018 CHAPTER 20 STANDARD PRACTICES ...
Страница 390: ...AIRCRAFT Standard Practices DA 42 NG AMM Page 2 15 Mar 2018 20 TITLE Doc 7 02 15 Rev 4 Intentionally left blank ...
Страница 394: ...AIRCRAFT Standard Practices DA 42 NG AMM Page 2 15 Mar 2018 20 00 00 Doc 7 02 15 Rev 4 Intentionally left blank ...
Страница 402: ...AIRCRAFT Standard Practices DA 42 NG AMM Page 4 15 Mar 2018 20 30 00 Doc 7 02 15 Rev 4 Intentionally left blank ...
Страница 410: ...AIRCRAFT Standard Practices DA 42 NG AMM Page 8 15 Mar 2018 20 70 00 Doc 7 02 15 Rev 4 Intentionally left blank ...
Страница 420: ...AIRCRAFT Standard Practices DA 42 NG AMM Page 10 15 Mar 2018 20 90 00 Doc 7 02 15 Rev 4 Intentionally left blank ...
Страница 422: ...AIRCRAFT Standard Practices DA 42 NG AMM Page 102 15 Mar 2018 20 90 00 Doc 7 02 15 Rev 4 Intentionally left blank ...
Страница 424: ...AIRCRAFT Standard Practices DA 42 NG AMM Page 202 15 Mar 2018 20 90 00 Doc 7 02 15 Rev 4 Intentionally left blank ...
Страница 426: ...AIRCRAFT Heating and Ventilation DA 42 NG AMM Page 2 15 Mar 2018 21 TITLE Doc 7 02 15 Rev 4 Intentionally left blank ...
Страница 430: ...AIRCRAFT Heating and Ventilation DA 42 NG AMM Page 4 15 Mar 2018 21 CONTENTS Doc 7 02 15 Rev 4 Intentionally left blank ...
Страница 460: ...AIRCRAFT Heating and Ventilation DA 42 NG AMM Page 2 15 Mar 2018 21 40 00 Doc 7 02 15 Rev 4 Figure 1 Heating System ...
Страница 462: ...AIRCRAFT Heating and Ventilation DA 42 NG AMM Page 4 15 Mar 2018 21 40 00 Doc 7 02 15 Rev 4 Intentionally left blank ...
Страница 464: ...AIRCRAFT Heating and Ventilation DA 42 NG AMM Page 102 15 Mar 2018 21 40 00 Doc 7 02 15 Rev 4 Intentionally left blank ...
Страница 472: ...AIRCRAFT Heating and Ventilation DA 42 NG AMM Page 208 15 Mar 2018 21 40 00 Doc 7 02 15 Rev 4 Intentionally left blank ...
Страница 492: ...AIRCRAFT Heating and Ventilation DA 42 NG AMM Page 214 15 Mar 2018 21 50 00 Doc 7 02 15 Rev 4 Intentionally left blank ...
Страница 498: ...AIRCRAFT Heating and Ventilation DA 42 NG AMM Page 102 15 Mar 2018 21 51 00 Doc 7 02 15 Rev 4 Intentionally left blank ...
Страница 516: ...AIRCRAFT Heating and Ventilation DA 42 NG AMM Page 4 15 Mar 2018 21 60 00 Doc 7 02 15 Rev 4 Intentionally left blank ...
Страница 518: ...AIRCRAFT Heating and Ventilation DA 42 NG AMM Page 102 15 Mar 2018 21 60 00 Doc 7 02 15 Rev 4 Intentionally left blank ...
Страница 524: ...AIRCRAFT Heating and Ventilation DA 42 NG AMM Page 206 15 Mar 2018 21 60 00 Doc 7 02 15 Rev 4 Intentionally left blank ...
Страница 525: ...AIRCRAFT DA 42 NG AMM Auto Flight Doc 7 02 15 Rev 4 22 TITLE Page 1 15 Mar 2018 CHAPTER 22 AUTO FLIGHT ...
Страница 526: ...AIRCRAFT Auto Flight DA 42 NG AMM Page 2 15 Mar 2018 22 TITLE Doc 7 02 15 Rev 4 Intentionally left blank ...
Страница 528: ...AIRCRAFT Auto Flight DA 42 NG AMM Page 2 15 Mar 2018 22 CONTENTS Doc 7 02 15 Rev 4 Intentionally left blank ...
Страница 530: ...AIRCRAFT Auto Flight DA 42 NG AMM Page 2 15 Mar 2018 22 00 00 Doc 7 02 15 Rev 4 Intentionally left blank ...
Страница 534: ...AIRCRAFT Auto Flight DA 42 NG AMM Page 4 15 Mar 2018 22 10 00 Doc 7 02 15 Rev 4 Figure 2 Roll Servo Installation ...
Страница 539: ...AIRCRAFT DA 42 NG AMM Auto Flight Doc 7 02 15 Rev 4 22 10 00 Page 205 15 Mar 2018 Figure 3 Pitch Servo Installation ...
Страница 546: ...AIRCRAFT Auto Flight DA 42 NG AMM Page 212 15 Mar 2018 22 10 00 Doc 7 02 15 Rev 4 Figure 5 Yaw Servo Installation ...
Страница 557: ...AIRCRAFT DA 42 NG AMM Communications Doc 7 02 15 Rev 4 23 TITLE Page 1 15 Mar 2018 CHAPTER 23 COMMUNICATIONS ...
Страница 558: ...AIRCRAFT Communications DA 42 NG AMM Page 2 15 Mar 2018 23 TITLE Doc 7 02 15 Rev 4 Intentionally left blank ...
Страница 562: ...AIRCRAFT Communications DA 42 NG AMM Page 2 15 Mar 2018 23 00 00 Doc 7 02 15 Rev 4 Intentionally left blank ...
Страница 566: ...AIRCRAFT Communications DA 42 NG AMM Page 4 15 Mar 2018 23 10 00 Doc 7 02 15 Rev 4 Intentionally left blank ...
Страница 568: ...AIRCRAFT Communications DA 42 NG AMM Page 102 15 Mar 2018 23 10 00 Doc 7 02 15 Rev 4 Intentionally left blank ...
Страница 574: ...AIRCRAFT Communications DA 42 NG AMM Page 2 15 Mar 2018 23 15 00 Doc 7 02 15 Rev 4 Intentionally left blank ...
Страница 576: ...AIRCRAFT Communications DA 42 NG AMM Page 102 15 Mar 2018 23 15 00 Doc 7 02 15 Rev 4 Intentionally left blank ...
Страница 580: ...AIRCRAFT Communications DA 42 NG AMM Page 204 15 Mar 2018 23 15 00 Doc 7 02 15 Rev 4 Intentionally left blank ...
Страница 586: ...AIRCRAFT Communications DA 42 NG AMM Page 6 15 Mar 2018 23 50 00 Doc 7 02 15 Rev 4 Intentionally left blank ...
Страница 588: ...AIRCRAFT Communications DA 42 NG AMM Page 102 15 Mar 2018 23 50 00 Doc 7 02 15 Rev 4 Intentionally left blank ...
Страница 595: ...AIRCRAFT DA 42 NG AMM Electrical Power Doc 7 02 15 Rev 4 24 TITLE Page 1 15 Mar 2018 CHAPTER 24 ELECTRICAL POWER ...
Страница 596: ...AIRCRAFT Electrical Power DA 42 NG AMM Page 2 15 Mar 2018 24 TITLE Doc 7 02 15 Rev 4 Intentionally left blank ...
Страница 600: ...AIRCRAFT Electrical Power DA 42 NG AMM Page 4 15 Mar 2018 24 CONTENTS Doc 7 02 15 Rev 4 Intentionally left blank ...
Страница 612: ...AIRCRAFT Electrical Power DA 42 NG AMM Page 12 15 Mar 2018 24 00 00 Doc 7 02 15 Rev 4 Intentionally left blank ...
Страница 618: ...AIRCRAFT Electrical Power DA 42 NG AMM Page 6 15 Mar 2018 24 30 00 Doc 7 02 15 Rev 4 Intentionally left blank ...
Страница 620: ...AIRCRAFT Electrical Power DA 42 NG AMM Page 102 15 Mar 2018 24 30 00 Doc 7 02 15 Rev 4 Intentionally left blank ...
Страница 634: ...AIRCRAFT Electrical Power DA 42 NG AMM Page 102 15 Mar 2018 24 31 00 Doc 7 02 15 Rev 4 Intentionally left blank ...
Страница 644: ...AIRCRAFT Electrical Power DA 42 NG AMM Page 210 15 Mar 2018 24 31 00 Doc 7 02 15 Rev 4 Intentionally left blank ...
Страница 646: ...AIRCRAFT Electrical Power DA 42 NG AMM Page 2 15 Mar 2018 24 32 00 Doc 7 02 15 Rev 4 Intentionally left blank ...
Страница 648: ...AIRCRAFT Electrical Power DA 42 NG AMM Page 102 15 Mar 2018 24 32 00 Doc 7 02 15 Rev 4 Intentionally left blank ...
Страница 652: ...AIRCRAFT Electrical Power DA 42 NG AMM Page 204 15 Mar 2018 24 32 00 Doc 7 02 15 Rev 4 Intentionally left blank ...
Страница 656: ...AIRCRAFT Electrical Power DA 42 NG AMM Page 4 15 Mar 2018 24 33 00 Doc 7 02 15 Rev 4 Intentionally left blank ...
Страница 658: ...AIRCRAFT Electrical Power DA 42 NG AMM Page 102 15 Mar 2018 24 33 00 Doc 7 02 15 Rev 4 Intentionally left blank ...
Страница 666: ...AIRCRAFT Electrical Power DA 42 NG AMM Page 4 15 Mar 2018 24 40 00 Doc 7 02 15 Rev 4 Intentionally left blank ...
Страница 668: ...AIRCRAFT Electrical Power DA 42 NG AMM Page 102 15 Mar 2018 24 40 00 Doc 7 02 15 Rev 4 Intentionally left blank ...
Страница 678: ...AIRCRAFT Electrical Power DA 42 NG AMM Page 102 15 Mar 2018 24 60 00 Doc 7 02 15 Rev 4 Intentionally left blank ...
Страница 688: ...AIRCRAFT Electrical Power DA 42 NG AMM Page 210 15 Mar 2018 24 60 00 Doc 7 02 15 Rev 4 Intentionally left blank ...
Страница 690: ...AIRCRAFT Equipment Furnishings DA 42 NG AMM Page 2 15 Mar 2018 25 TITLE Doc 7 02 15 Rev 4 Intentionally left blank ...
Страница 734: ...AIRCRAFT Equipment Furnishings DA 42 NG AMM Page 4 15 Mar 2018 25 50 00 Doc 7 02 15 Rev 4 Intentionally left blank ...
Страница 744: ...AIRCRAFT Equipment Furnishings DA 42 NG AMM Page 102 15 Mar 2018 25 60 00 Doc 7 02 15 Rev 4 Intentionally left blank ...
Страница 762: ...AIRCRAFT Equipment Furnishings DA 42 NG AMM Page 218 15 Mar 2018 25 60 00 Doc 7 02 15 Rev 4 Intentionally left blank ...
Страница 763: ...AIRCRAFT DA 42 NG AMM Fire Protection Doc 7 02 15 Rev 4 26 TITLE Page 1 15 Mar 2018 CHAPTER 26 FIRE PROTECTION ...
Страница 764: ...AIRCRAFT Fire Protection DA 42 NG AMM Page 2 15 Mar 2018 26 TITLE Doc 7 02 15 Rev 4 Intentionally left blank ...
Страница 766: ...AIRCRAFT Fire Protection DA 42 NG AMM Page 2 15 Mar 2018 26 CONTENTS Doc 7 02 15 Rev 4 Intentionally left blank ...
Страница 772: ...AIRCRAFT Fire Protection DA 42 NG AMM Page 6 15 Mar 2018 26 00 00 Doc 7 02 15 Rev 4 Intentionally left blank ...
Страница 774: ...AIRCRAFT Fire Protection DA 42 NG AMM Page 102 15 Mar 2018 26 00 00 Doc 7 02 15 Rev 4 Intentionally left blank ...
Страница 777: ...AIRCRAFT DA 42 NG AMM Flight Controls Doc 7 02 15 Rev 4 27 TITLE Page 1 15 Mar 2018 CHAPTER 27 FLIGHT CONTROLS ...
Страница 778: ...AIRCRAFT Flight Controls DA 42 NG AMM Page 2 15 Mar 2018 27 TITLE Doc 7 02 15 Rev 4 Intentionally left blank ...
Страница 784: ...AIRCRAFT Flight Controls DA 42 NG AMM Page 6 15 Mar 2018 27 CONTENTS Doc 7 02 15 Rev 4 Intentionally left blank ...
Страница 790: ...AIRCRAFT Flight Controls DA 42 NG AMM Page 6 15 Mar 2018 27 00 00 Doc 7 02 15 Rev 4 Intentionally left blank ...
Страница 806: ...AIRCRAFT Flight Controls DA 42 NG AMM Page 102 15 Mar 2018 27 10 00 Doc 7 02 15 Rev 4 Intentionally left blank ...
Страница 814: ...AIRCRAFT Flight Controls DA 42 NG AMM Page 208 15 Mar 2018 27 10 00 Doc 7 02 15 Rev 4 Intentionally left blank ...
Страница 824: ...AIRCRAFT Flight Controls DA 42 NG AMM Page 10 15 Mar 2018 27 20 00 Doc 7 02 15 Rev 4 Intentionally left blank ...
Страница 826: ...AIRCRAFT Flight Controls DA 42 NG AMM Page 102 15 Mar 2018 27 20 00 Doc 7 02 15 Rev 4 Intentionally left blank ...
Страница 848: ...AIRCRAFT Flight Controls DA 42 NG AMM Page 102 15 Mar 2018 27 21 00 Doc 7 02 15 Rev 4 Intentionally left blank ...
Страница 856: ...AIRCRAFT Flight Controls DA 42 NG AMM Page 208 15 Mar 2018 27 21 00 Doc 7 02 15 Rev 4 Intentionally left blank ...
Страница 864: ...AIRCRAFT Flight Controls DA 42 NG AMM Page 102 15 Mar 2018 27 30 00 Doc 7 02 15 Rev 4 Intentionally left blank ...
Страница 878: ...AIRCRAFT Flight Controls DA 42 NG AMM Page 214 15 Mar 2018 27 30 00 Doc 7 02 15 Rev 4 Intentionally left blank ...
Страница 880: ...AIRCRAFT Flight Controls DA 42 NG AMM Page 2 15 Mar 2018 27 37 00 Doc 7 02 15 Rev 4 Intentionally left blank ...
Страница 886: ...AIRCRAFT Flight Controls DA 42 NG AMM Page 204 15 Mar 2018 27 37 00 Doc 7 02 15 Rev 4 Intentionally left blank ...
Страница 892: ...AIRCRAFT Flight Controls DA 42 NG AMM Page 6 15 Mar 2018 27 38 00 Doc 7 02 15 Rev 4 Intentionally left blank ...
Страница 894: ...AIRCRAFT Flight Controls DA 42 NG AMM Page 102 15 Mar 2018 27 38 00 Doc 7 02 15 Rev 4 Intentionally left blank ...
Страница 904: ...AIRCRAFT Flight Controls DA 42 NG AMM Page 2 15 Mar 2018 27 39 00 Doc 7 02 15 Rev 4 Intentionally left blank ...
Страница 906: ...AIRCRAFT Flight Controls DA 42 NG AMM Page 102 15 Mar 2018 27 39 00 Doc 7 02 15 Rev 4 Intentionally left blank ...
Страница 908: ...AIRCRAFT Flight Controls DA 42 NG AMM Page 202 15 Mar 2018 27 39 00 Doc 7 02 15 Rev 4 Intentionally left blank ...
Страница 933: ...AIRCRAFT DA 42 NG AMM Fuel Doc 7 02 15 Rev 4 28 TITLE Page 1 15 Mar 2018 CHAPTER 28 FUEL ...
Страница 934: ...AIRCRAFT Fuel DA 42 NG AMM Page 2 15 Mar 2018 28 TITLE Doc 7 02 15 Rev 4 Intentionally left blank ...
Страница 938: ...AIRCRAFT Fuel DA 42 NG AMM Page 4 15 Mar 2018 28 CONTENTS Doc 7 02 15 Rev 4 Intentionally left blank ...
Страница 958: ...AIRCRAFT Fuel DA 42 NG AMM Page 10 15 Mar 2018 28 10 00 Doc 7 02 15 Rev 4 Intentionally left blank ...
Страница 960: ...AIRCRAFT Fuel DA 42 NG AMM Page 102 15 Mar 2018 28 10 00 Doc 7 02 15 Rev 4 Intentionally left blank ...
Страница 984: ...AIRCRAFT Fuel DA 42 NG AMM Page 102 15 Mar 2018 28 20 00 Doc 7 02 15 Rev 4 Intentionally left blank ...
Страница 1024: ...AIRCRAFT Fuel DA 42 NG AMM Page 102 15 Mar 2018 28 21 00 Doc 7 02 15 Rev 4 Intentionally left blank ...
Страница 1050: ...AIRCRAFT Fuel DA 42 NG AMM Page 226 15 Mar 2018 28 21 00 Doc 7 02 15 Rev 4 Intentionally left blank ...
Страница 1054: ...AIRCRAFT Fuel DA 42 NG AMM Page 4 15 Mar 2018 28 40 00 Doc 7 02 15 Rev 4 Intentionally left blank ...
Страница 1065: ...AIRCRAFT DA 42 NG AMM Hydraulic Power Doc 7 02 15 Rev 4 29 TITLE Page 1 15 Mar 2018 CHAPTER 29 HYDRAULIC POWER ...
Страница 1066: ...AIRCRAFT Hydraulic Power DA 42 NG AMM Page 2 15 Mar 2018 29 TITLE Doc 7 02 15 Rev 4 Intentionally left blank ...
Страница 1068: ...AIRCRAFT Hydraulic Power DA 42 NG AMM Page 2 15 Mar 2018 29 CONTENTS Doc 7 02 15 Rev 4 Intentionally left blank ...
Страница 1070: ...AIRCRAFT Hydraulic Power DA 42 NG AMM Page 2 15 Mar 2018 29 00 00 Doc 7 02 15 Rev 4 Intentionally left blank ...
Страница 1072: ...AIRCRAFT Hydraulic Power DA 42 NG AMM Page 2 15 Mar 2018 29 10 00 Doc 7 02 15 Rev 4 Intentionally left blank ...
Страница 1142: ...AIRCRAFT Ice Protection System DA 42 NG Series AMM Page 2 15 Mar 2018 30 TITLE Doc 7 02 15 Rev 4 Intentionally left blank ...
Страница 1144: ...AIRCRAFT Ice Protection System DA 42 NG Series AMM Page 2 15 Mar 2018 30 CONTENTS Doc 7 02 15 Rev 4 Intentionally left blank ...
Страница 1160: ...AIRCRAFT Ice Protection System DA 42 NG Series AMM Page 102 15 Mar 2018 30 00 00 Doc 7 02 15 Rev 4 Intentionally left blank ...
Страница 1184: ...AIRCRAFT Ice Protection System DA 42 NG Series AMM Page 224 15 Mar 2018 30 00 00 Doc 7 02 15 Rev 4 Intentionally left blank ...
Страница 1185: ...AIRCRAFT DA 42 NG AMM Indicating Systems Doc 7 02 15 Rev 4 31 TITLE Page 1 15 Mar 2018 CHAPTER 31 INDICATING SYSTEMS ...
Страница 1186: ...AIRCRAFT Indicating Systems DA 42 NG AMM Page 2 15 Mar 2018 31 TITLE Doc 7 02 15 Rev 4 Intentionally left blank ...
Страница 1190: ...AIRCRAFT Indicating Systems DA 42 NG AMM Page 2 15 Mar 2018 31 00 00 Doc 7 02 15 Rev 4 Intentionally left blank ...
Страница 1198: ...AIRCRAFT Indicating Systems DA 42 NG AMM Page 8 15 Mar 2018 31 10 00 Doc 7 02 15 Rev 4 Intentionally left blank ...
Страница 1200: ...AIRCRAFT Indicating Systems DA 42 NG AMM Page 102 15 Mar 2018 31 10 00 Doc 7 02 15 Rev 4 Intentionally left blank ...
Страница 1208: ...AIRCRAFT Indicating Systems DA 42 NG AMM Page 2 15 Mar 2018 31 20 00 Doc 7 02 15 Rev 4 Intentionally left blank ...
Страница 1224: ...AIRCRAFT Indicating Systems DA 42 NG AMM Page 102 15 Mar 2018 31 40 00 Doc 7 02 15 Rev 4 Intentionally left blank ...
Страница 1250: ...AIRCRAFT Indicating Systems DA 42 NG AMM Page 226 15 Mar 2018 31 40 00 Doc 7 02 15 Rev 4 Intentionally left blank ...
Страница 1251: ...AIRCRAFT DA 42 NG AMM Landing Gear Doc 7 02 15 Rev 4 32 TITLE Page 1 15 Mar 2018 CHAPTER 32 LANDING GEAR ...
Страница 1252: ...AIRCRAFT Landing Gear DA 42 NG AMM Page 2 15 Mar 2018 32 TITLE Doc 7 02 15 Rev 4 Intentionally left blank ...
Страница 1264: ...AIRCRAFT Landing Gear DA 42 NG AMM Page 102 15 Mar 2018 32 10 00 Doc 7 02 15 Rev 4 Intentionally left blank ...
Страница 1315: ...AIRCRAFT DA 42 NG AMM Landing Gear Doc 7 02 15 Rev 4 32 10 00 Page 251 15 Mar 2018 Figure 14 Main Landing Gear Door Measurement ...
Страница 1322: ...AIRCRAFT Landing Gear DA 42 NG AMM Page 102 15 Mar 2018 32 20 00 Doc 7 02 15 Rev 4 Intentionally left blank ...
Страница 1398: ...AIRCRAFT Landing Gear DA 42 NG AMM Page 8 15 Mar 2018 32 40 00 Doc 7 02 15 Rev 4 Intentionally left blank ...
Страница 1426: ...AIRCRAFT Landing Gear DA 42 NG AMM Page 226 15 Mar 2018 32 40 00 Doc 7 02 15 Rev 4 Intentionally left blank ...
Страница 1432: ...AIRCRAFT Landing Gear DA 42 NG AMM Page 102 15 Mar 2018 32 50 00 Doc 7 02 15 Rev 4 Intentionally left blank ...
Страница 1438: ...AIRCRAFT Landing Gear DA 42 NG AMM Page 206 15 Mar 2018 32 50 00 Doc 7 02 15 Rev 4 Intentionally left blank ...
Страница 1444: ...AIRCRAFT Landing Gear DA 42 NG AMM Page 102 15 Mar 2018 32 60 00 Doc 7 02 15 Rev 4 Intentionally left blank ...
Страница 1458: ...AIRCRAFT Landing Gear DA 42 NG AMM Page 214 15 Mar 2018 32 60 00 Doc 7 02 15 Rev 4 Intentionally left blank ...
Страница 1459: ...AIRCRAFT DA 42 NG AMM Lights Doc 7 02 15 Rev 4 33 TITLE Page 1 15 Mar 2018 CHAPTER 33 LIGHTS ...
Страница 1460: ...AIRCRAFT Lights DA 42 NG AMM Page 2 15 Mar 2018 33 TITLE Doc 7 02 15 Rev 4 Intentionally left blank ...
Страница 1466: ...AIRCRAFT Lights DA 42 NG AMM Page 4 15 Mar 2018 33 00 00 Doc 7 02 15 Rev 4 Intentionally left blank ...
Страница 1472: ...AIRCRAFT Lights DA 42 NG AMM Page 102 15 Mar 2018 33 10 00 Doc 7 02 15 Rev 4 Intentionally left blank ...
Страница 1508: ...AIRCRAFT Lights DA 42 NG AMM Page 218 15 Mar 2018 33 40 00 Doc 7 02 15 Rev 4 Intentionally left blank ...
Страница 1509: ...AIRCRAFT DA 42 NG AMM Navigation Doc 7 02 15 Rev 4 34 TITLE Page 1 15 Mar 2018 CHAPTER 34 NAVIGATION ...
Страница 1510: ...AIRCRAFT Navigation DA 42 NG AMM Page 2 15 Mar 2018 34 TITLE Doc 7 02 15 Rev 4 Intentionally left blank ...
Страница 1518: ...AIRCRAFT Navigation DA 42 NG AMM Page 4 15 Mar 2018 34 00 00 Doc 7 02 15 Rev 4 Intentionally left blank ...
Страница 1524: ...AIRCRAFT Navigation DA 42 NG AMM Page 102 15 Mar 2018 34 10 00 Doc 7 02 15 Rev 4 Intentionally left blank ...
Страница 1550: ...AIRCRAFT Navigation DA 42 NG AMM Page 206 15 Mar 2018 34 20 00 Doc 7 02 15 Rev 4 Intentionally left blank ...
Страница 1552: ...AIRCRAFT Navigation DA 42 NG AMM Page 2 15 Mar 2018 34 30 00 Doc 7 02 15 Rev 4 Intentionally left blank ...
Страница 1554: ...AIRCRAFT Navigation DA 42 NG AMM Page 2 15 Mar 2018 34 40 00 Doc 7 02 15 Rev 4 Intentionally left blank ...
Страница 1556: ...AIRCRAFT Navigation DA 42 NG AMM Page 2 15 Mar 2018 34 41 00 Doc 7 02 15 Rev 4 Intentionally left blank ...
Страница 1558: ...AIRCRAFT Navigation DA 42 NG AMM Page 102 15 Mar 2018 34 41 00 Doc 7 02 15 Rev 4 Intentionally left blank ...
Страница 1564: ...AIRCRAFT Navigation DA 42 NG AMM Page 102 15 Mar 2018 34 42 00 Doc 7 02 15 Rev 4 Intentionally left blank ...
Страница 1572: ...AIRCRAFT Navigation DA 42 NG AMM Page 102 15 Mar 2018 34 43 00 Doc 7 02 15 Rev 4 Intentionally left blank ...
Страница 1576: ...AIRCRAFT Navigation DA 42 NG AMM Page 204 15 Mar 2018 34 43 00 Doc 7 02 15 Rev 4 Figure 2 Radar Nose Cone Sealed Joint ...
Страница 1578: ...AIRCRAFT Navigation DA 42 NG AMM Page 2 15 Mar 2018 34 50 00 Doc 7 02 15 Rev 4 Figure 1 Antenna Locations ...
Страница 1580: ...AIRCRAFT Navigation DA 42 NG AMM Page 102 15 Mar 2018 34 50 00 Doc 7 02 15 Rev 4 Intentionally left blank ...
Страница 1592: ...AIRCRAFT Navigation DA 42 NG AMM Page 212 15 Mar 2018 34 50 00 Doc 7 02 15 Rev 4 Intentionally left blank ...
Страница 1594: ...AIRCRAFT Navigation DA 42 NG AMM Page 2 15 Mar 2018 34 56 00 Doc 7 02 15 Rev 4 Intentionally left blank ...
Страница 1595: ...AIRCRAFT DA 42 NG AMM Oxygen System Doc 7 02 15 Rev 4 35 TITLE Page 1 15 Mar 2018 CHAPTER 35 OXYGEN SYSTEM ...
Страница 1596: ...AIRCRAFT Oxygen System DA 42 NG AMM Page 2 15 Mar 2018 35 TITLE Doc 7 02 15 Rev 4 Intentionally left blank ...
Страница 1598: ...AIRCRAFT Oxygen System DA 42 NG AMM Page 2 15 Mar 2018 35 CONTENTS Doc 7 02 15 Rev 4 Intentionally left blank ...
Страница 1600: ...AIRCRAFT Oxygen System DA 42 NG AMM Page 2 15 Mar 2018 35 00 00 Doc 7 02 15 Rev 4 Intentionally left blank ...
Страница 1608: ...AIRCRAFT Oxygen System DA 42 NG AMM Page 102 15 Mar 2018 35 10 00 Doc 7 02 15 Rev 4 Intentionally left blank ...
Страница 1620: ...AIRCRAFT Standard Practices Structures DA 42 NG AMM Page 2 15 Mar 2018 51 TITLE Doc 7 02 15 Rev 4 Intentionally left blank ...
Страница 1624: ...AIRCRAFT Standard Practices Structures DA 42 NG AMM Page 4 15 Mar 2018 51 CONTENTS Doc 7 02 15 Rev 4 Intentionally left blank ...
Страница 1636: ...AIRCRAFT Standard Practices Structures DA 42 NG AMM Page 4 15 Mar 2018 51 20 00 Doc 7 02 15 Rev 4 Intentionally left blank ...
Страница 1668: ...AIRCRAFT Standard Practices Structures DA 42 NG AMM Page 232 15 Mar 2018 51 20 00 Doc 7 02 15 Rev 4 Intentionally left blank ...
Страница 1680: ...AIRCRAFT Standard Practices Structures DA 42 NG AMM Page 12 15 Mar 2018 51 30 00 Doc 7 02 15 Rev 4 Intentionally left blank ...
Страница 1684: ...AIRCRAFT Standard Practices Structures DA 42 NG AMM Page 202 15 Mar 2018 51 40 00 Doc 7 02 15 Rev 4 Intentionally left blank ...
Страница 1704: ...AIRCRAFT Standard Practices Structures DA 42 NG AMM Page 4 15 Mar 2018 51 80 00 Doc 7 02 15 Rev 4 Intentionally left blank ...
Страница 1711: ...AIRCRAFT DA 42 NG AMM Doors Doc 7 02 15 Rev 4 52 TITLE Page 1 15 Mar 2018 CHAPTER 52 DOORS ...
Страница 1712: ...AIRCRAFT Doors DA 42 NG AMM Page 2 15 Mar 2018 52 TITLE Doc 7 02 15 Rev 4 Intentionally left blank ...
Страница 1716: ...AIRCRAFT Doors DA 42 NG AMM Page 2 15 Mar 2018 52 00 00 Doc 7 02 15 Rev 4 Intentionally left blank ...
Страница 1724: ...AIRCRAFT Doors DA 42 NG AMM Page 8 15 Mar 2018 52 10 00 Doc 7 02 15 Rev 4 Intentionally left blank ...
Страница 1726: ...AIRCRAFT Doors DA 42 NG AMM Page 102 15 Mar 2018 52 10 00 Doc 7 02 15 Rev 4 Intentionally left blank ...
Страница 1762: ...AIRCRAFT Doors DA 42 NG AMM Page 236 15 Mar 2018 52 10 00 Doc 7 02 15 Rev 4 Intentionally left blank ...
Страница 1766: ...AIRCRAFT Doors DA 42 NG AMM Page 4 15 Mar 2018 52 30 00 Doc 7 02 15 Rev 4 Intentionally left blank ...
Страница 1768: ...AIRCRAFT Doors DA 42 NG AMM Page 102 15 Mar 2018 52 30 00 Doc 7 02 15 Rev 4 Intentionally left blank ...
Страница 1773: ...AIRCRAFT DA 42 NG AMM Fuselage Doc 7 02 15 Rev 4 53 TITLE Page 1 15 Mar 2018 CHAPTER 53 FUSELAGE ...
Страница 1774: ...AIRCRAFT Fuselage DA 42 NG AMM Page 2 15 Mar 2018 53 TITLE Doc 7 02 15 Rev 4 Intentionally left blank ...
Страница 1776: ...AIRCRAFT Fuselage DA 42 NG AMM Page 2 15 Mar 2018 53 CONTENTS Doc 7 02 15 Rev 4 Intentionally left blank ...
Страница 1788: ...AIRCRAFT Fuselage DA 42 NG AMM Page 10 15 Mar 2018 53 10 00 Doc 7 02 15 Rev 4 Figure 6 Trim Weight ...
Страница 1797: ...AIRCRAFT DA 42 NG AMM Stabilizers Doc 7 02 15 Rev 3 55 TITLE Page 1 15 Mar 2018 CHAPTER 55 STABILIZERS ...
Страница 1798: ...AIRCRAFT Stabilizers DA 42 NG AMM Page 2 15 Mar 2018 55 TITLE Doc 7 02 15 Rev 4 Intentionally left blank ...
Страница 1810: ...AIRCRAFT Stabilizers DA 42 NG AMM Page 206 15 Mar 2018 55 10 00 Doc 7 02 15 Rev 4 Intentionally left blank ...
Страница 1812: ...AIRCRAFT Stabilizers DA 42 NG AMM Page 2 15 Mar 2018 55 20 00 Doc 7 02 15 Rev 4 Figure 1 Elevator Structure ...
Страница 1820: ...AIRCRAFT Stabilizers DA 42 NG AMM Page 206 15 Mar 2018 55 20 00 Doc 7 02 15 Rev 4 Intentionally left blank ...
Страница 1822: ...AIRCRAFT Stabilizers DA 42 NG AMM Page 2 15 Mar 2018 55 30 00 Doc 7 02 15 Rev 4 Intentionally left blank ...
Страница 1826: ...AIRCRAFT Stabilizers DA 42 NG AMM Page 4 15 Mar 2018 55 40 00 Doc 7 02 15 Rev 4 Left Shell Right Shell Figure 2 Rudder Trim Tab ...
Страница 1834: ...AIRCRAFT Stabilizers DA 42 NG AMM Page 208 15 Mar 2018 55 40 00 Doc 7 02 15 Rev 4 Intentionally left blank ...
Страница 1835: ...AIRCRAFT DA 42 NG AMM Windows Doc 7 02 15 Rev 4 56 TITLE Page 1 15 Mar 2018 CHAPTER 56 WINDOWS ...
Страница 1836: ...AIRCRAFT Windows DA 42 NG AMM Page 2 15 Mar 2018 56 TITLE Doc 7 02 15 Rev 4 Intentionally left blank ...
Страница 1838: ...AIRCRAFT Windows DA 42 NG AMM Page 2 15 Mar 2018 56 CONTENTS Doc 7 02 15 Rev 4 Intentionally left blank ...
Страница 1840: ...AIRCRAFT Windows DA 42 NG AMM Page 2 15 Mar 2018 56 00 00 Doc 7 02 15 Rev 4 Intentionally left blank ...
Страница 1844: ...AIRCRAFT Windows DA 42 NG AMM Page 4 15 Mar 2018 56 10 00 Doc 7 02 15 Rev 4 Intentionally left blank ...
Страница 1851: ...AIRCRAFT DA 42 NG AMM Windows Doc 7 02 15 Rev 4 56 10 00 Page 207 15 Mar 2018 Figure 4 Window Repairs ...
Страница 1853: ...AIRCRAFT DA 42 NG AMM Wings Doc 7 02 15 Rev 4 57 TITLE Page 1 15 Mar 2018 CHAPTER 57 WINGS ...
Страница 1854: ...AIRCRAFT Wings DA 42 NG AMM Page 2 15 Mar 2018 57 TITLE Doc 7 02 15 Rev 4 Intentionally left blank ...
Страница 1856: ...AIRCRAFT Wings DA 42 NG AMM Page 2 15 Mar 2018 57 CONTENTS Doc 7 02 15 Rev 4 Maintenance Practices 1 General 201 ...
Страница 1858: ...AIRCRAFT Wings DA 42 NG AMM Page 2 15 Mar 2018 57 00 00 Doc 7 02 15 Rev 4 Intentionally left blank ...
Страница 1884: ...AIRCRAFT Wings DA 42 NG AMM Page 6 15 Mar 2018 57 50 00 Doc 7 02 15 Rev 4 Intentionally left blank ...
Страница 1896: ...AIRCRAFT Wings DA 42 NG AMM Page 212 15 Mar 2018 57 50 00 Doc 7 02 15 Rev 4 Intentionally left blank ...
Страница 1900: ...AIRCRAFT Wings DA 42 NG AMM Page 4 15 Mar 2018 57 60 00 Doc 7 02 15 Rev 4 Intentionally left blank ...
Страница 1906: ...AIRCRAFT Wings DA 42 NG AMM Page 206 15 Mar 2018 57 60 00 Doc 7 02 15 Rev 4 Intentionally left blank ...
Страница 1907: ...AIRCRAFT DA 42 NG AMM Propeller Doc 7 02 15 Rev 4 61 TITLE Page 1 15 Mar 2018 CHAPTER 61 PROPELLER ...
Страница 1908: ...AIRCRAFT Propeller DA 42 NG AMM Page 2 15 Mar 2018 61 TITLE Doc 7 02 15 Rev 4 Intentionally left blank ...
Страница 1912: ...AIRCRAFT Propeller DA 42 NG AMM Page 2 15 Mar 2018 61 00 00 Doc 7 02 15 Rev 4 Spinner Propeller Figure 1 Propeller Assembly ...
Страница 1918: ...AIRCRAFT Propeller DA 42 NG AMM Page 6 15 Mar 2018 61 10 00 Doc 7 02 15 Rev 4 Intentionally left blank ...
Страница 1920: ...AIRCRAFT Propeller DA 42 NG AMM Page 102 15 Mar 2018 61 10 00 Doc 7 02 15 Rev 4 Intentionally left blank ...
Страница 1938: ...AIRCRAFT Propeller DA 42 NG AMM Page 218 15 Mar 2018 61 10 00 Doc 7 02 15 Rev 4 Intentionally left blank ...
Страница 1940: ...AIRCRAFT Propeller DA 42 NG AMM Page 2 15 Mar 2018 61 20 00 Doc 7 02 15 Rev 4 Figure 1 Propeller RPM Adjusted by the EECU System ...
Страница 1944: ...AIRCRAFT Propeller DA 42 NG AMM Page 6 15 Mar 2018 61 20 00 Doc 7 02 15 Rev 4 Intentionally left blank ...
Страница 1946: ...AIRCRAFT Propeller DA 42 NG AMM Page 102 15 Mar 2018 61 20 00 Doc 7 02 15 Rev 4 Intentionally left blank ...
Страница 1957: ...AIRCRAFT DA 42 NG AMM Power Plant Doc 7 02 15 Rev 4 71 TITLE Page 1 15 Mar 2018 CHAPTER 71 POWER PLANT ...
Страница 1958: ...AIRCRAFT Power Plant DA 42 NG AMM Page 2 15 Mar 2018 71 TITLE Doc 7 02 15 Rev 4 Intentionally left blank ...
Страница 1968: ...AIRCRAFT Power Plant DA 42 NG AMM Page 6 15 Mar 2018 71 00 00 Doc 7 02 15 Rev 4 Intentionally left blank ...
Страница 1970: ...AIRCRAFT Power Plant DA 42 NG AMM Page 102 15 Mar 2018 71 00 00 Doc 7 02 15 Rev 4 Intentionally left blank ...
Страница 1990: ...AIRCRAFT Power Plant DA 42 NG AMM Page 220 15 Mar 2018 71 00 00 Doc 7 02 15 Rev 4 Intentionally left blank ...
Страница 1994: ...AIRCRAFT Power Plant DA 42 NG AMM Page 4 15 Mar 2018 71 10 00 Doc 7 02 15 Rev 4 Intentionally left blank ...
Страница 1996: ...AIRCRAFT Power Plant DA 42 NG AMM Page 102 15 Mar 2018 71 10 00 Doc 7 02 15 Rev 4 Intentionally left blank ...
Страница 2004: ...AIRCRAFT Power Plant DA 42 NG AMM Page 4 15 Mar 2018 71 11 00 Doc 7 02 15 Rev 4 Intentionally left blank ...
Страница 2006: ...AIRCRAFT Power Plant DA 42 NG AMM Page 102 15 Mar 2018 71 11 00 Doc 7 02 15 Rev 4 Intentionally left blank ...
Страница 2016: ...AIRCRAFT Power Plant DA 42 NG AMM Page 4 15 Mar 2018 71 20 00 Doc 7 02 15 Rev 4 Intentionally left blank ...
Страница 2018: ...AIRCRAFT Power Plant DA 42 NG AMM Page 102 15 Mar 2018 71 20 00 Doc 7 02 15 Rev 4 Intentionally left blank ...
Страница 2022: ...AIRCRAFT Power Plant DA 42 NG AMM Page 204 15 Mar 2018 71 20 00 Doc 7 02 15 Rev 4 Intentionally left blank ...
Страница 2024: ...AIRCRAFT Power Plant DA 42 NG AMM Page 2 15 Mar 2018 71 50 00 Doc 7 02 15 Rev 4 Intentionally left blank ...
Страница 2027: ...AIRCRAFT DA 42 NG AMM Power Plant Doc 7 02 15 Rev 4 71 60 00 Page 3 15 Mar 2018 Figure 2 Air Valve Assembly ...
Страница 2030: ...AIRCRAFT Power Plant DA 42 NG AMM Page 6 15 Mar 2018 71 60 00 Doc 7 02 15 Rev 4 Intentionally left blank ...
Страница 2032: ...AIRCRAFT Power Plant DA 42 NG AMM Page 102 15 Mar 2018 71 60 00 Doc 7 02 15 Rev 4 Intentionally left blank ...
Страница 2052: ...AIRCRAFT Power Plant DA 42 NG AMM Page 220 15 Mar 2018 71 60 00 Doc 7 02 15 Rev 4 Intentionally left blank ...
Страница 2058: ...AIRCRAFT Power Plant DA 42 NG AMM Page 102 15 Mar 2018 71 61 00 Doc 7 02 15 Rev 4 Intentionally left blank ...
Страница 2064: ...AIRCRAFT Power Plant DA 42 NG AMM Page 204 15 Mar 2018 71 70 00 Doc 7 02 15 Rev 4 Intentionally left blank ...
Страница 2070: ...AIRCRAFT Power Plant DA 42 NG AMM Page 204 15 Mar 2018 71 71 00 Doc 7 02 15 Rev 4 Intentionally left blank ...
Страница 2071: ...AIRCRAFT DA 42 NG AMM Engine Doc 7 02 15 Rev 4 72 TITLE Page 1 15 Mar 2018 CHAPTER 72 ENGINE ...
Страница 2072: ...AIRCRAFT Engine DA 42 NG AMM Page 2 15 Mar 2018 72 TITLE Doc 7 02 15 Rev 4 Intentionally left blank ...
Страница 2074: ...AIRCRAFT Engine DA 42 NG AMM Page 2 15 Mar 2018 72 CONTENTS Doc 7 02 15 Rev 4 Intentionally left blank ...
Страница 2078: ...AIRCRAFT Engine DA 42 NG AMM Page 4 15 Mar 2018 72 00 00 Doc 7 02 15 Rev 4 Intentionally left blank ...
Страница 2080: ...AIRCRAFT Engine DA 42 NG AMM Page 102 15 Mar 2018 72 00 00 Doc 7 02 15 Rev 4 Intentionally left blank ...
Страница 2086: ...AIRCRAFT Engine DA 42 NG AMM Page 206 15 Mar 2018 72 00 00 Doc 7 02 15 Rev 4 Intentionally left blank ...
Страница 2087: ...AIRCRAFT DA 42 NG AMM Engine Fuel and Control Doc 7 02 15 Rev 4 73 TITLE Page 1 15 Mar 2018 CHAPTER 73 ENGINE FUEL AND CONTROL ...
Страница 2088: ...AIRCRAFT Engine Fuel and Control DA 42 NG AMM Page 2 15 Mar 2018 73 TITLE Doc 7 02 15 Rev 4 Intentionally left blank ...
Страница 2090: ...AIRCRAFT Engine Fuel and Control DA 42 NG AMM Page 2 15 Mar 2018 73 CONTENTS Doc 7 02 15 Rev 4 Intentionally left blank ...
Страница 2096: ...AIRCRAFT Engine Fuel and Control DA 42 NG AMM Page 102 15 Mar 2018 73 00 00 Doc 7 02 15 Rev 4 Intentionally left blank ...
Страница 2100: ...AIRCRAFT Engine Fuel and Control DA 42 NG AMM Page 204 15 Mar 2018 73 00 00 Doc 7 02 15 Rev 4 Intentionally left blank ...
Страница 2101: ...AIRCRAFT DA 42 NG AMM Liquid Cooling System Doc 7 02 15 Rev 4 75 TITLE Page 1 15 Mar 2018 CHAPTER 75 LIQUID COOLING SYSTEM ...
Страница 2102: ...AIRCRAFT Liquid Cooling System DA 42 NG AMM Page 2 15 Mar 2018 75 TITLE Doc 7 02 15 Rev 4 Intentionally left blank ...
Страница 2104: ...AIRCRAFT Liquid Cooling System DA 42 NG AMM Page 2 15 Mar 2018 75 CONTENTS Doc 7 02 15 Rev 4 Intentionally left blank ...
Страница 2114: ...AIRCRAFT Liquid Cooling System DA 42 NG AMM Page 102 15 Mar 2018 75 00 00 Doc 7 02 15 Rev 4 Intentionally left blank ...
Страница 2135: ...AIRCRAFT DA 42 NG AMM Engine Controls Doc 7 02 15 Rev 4 76 TITLE Page 1 15 Mar 2018 CHAPTER 76 ENGINE CONTROLS ...
Страница 2136: ...AIRCRAFT Engine Controls DA 42 NG AMM Page 2 15 Mar 2018 76 TITLE Doc 7 02 15 Rev 4 Intentionally left blank ...
Страница 2138: ...AIRCRAFT Engine Controls DA 42 NG AMM Page 2 15 Mar 2018 76 CONTENTS Doc 7 02 15 Rev 4 Intentionally left blank ...
Страница 2146: ...AIRCRAFT Engine Controls DA 42 NG AMM Page 102 15 Mar 2018 76 00 00 Doc 7 02 15 Rev 4 Intentionally left blank ...
Страница 2162: ...AIRCRAFT Engine Controls DA 42 NG AMM Page 216 15 Mar 2018 76 00 00 Doc 7 02 15 Rev 4 Intentionally left blank ...
Страница 2163: ...AIRCRAFT DA 42 NG AMM Engine Indicating Doc 7 02 15 Rev 4 77 TITLE Page 1 15 Mar 2018 CHAPTER 77 ENGINE INDICATING ...
Страница 2164: ...AIRCRAFT Engine Indicating DA 42 NG AMM Page 2 15 Mar 2018 77 TITLE Doc 7 02 15 Rev 4 Intentionally left blank ...
Страница 2166: ...AIRCRAFT Engine Indicating DA 42 NG AMM Page 2 15 Mar 2018 77 CONTENTS Doc 7 02 15 Rev 4 Intentionally left blank ...
Страница 2172: ...AIRCRAFT Engine Indicating DA 42 NG AMM Page 4 15 Mar 2018 77 40 00 Doc 7 02 15 Rev 4 Intentionally left blank ...
Страница 2174: ...AIRCRAFT Engine Indicating DA 42 NG AMM Page 102 15 Mar 2018 77 40 00 Doc 7 02 15 Rev 4 Intentionally left blank ...
Страница 2182: ...AIRCRAFT Engine Indicating DA 42 NG AMM Page 208 15 Mar 2018 77 40 00 Doc 7 02 15 Rev 4 Intentionally left blank ...
Страница 2183: ...AIRCRAFT DA 42 NG AMM Exhaust Doc 7 02 15 Rev 4 78 TITLE Page 1 15 Mar 2018 CHAPTER 78 EXHAUST ...
Страница 2184: ...AIRCRAFT Exhaust DA 42 NG AMM Page 2 15 Mar 2018 78 TITLE Doc 7 02 15 Rev 4 Intentionally left blank ...
Страница 2186: ...AIRCRAFT Exhaust DA 42 NG AMM Page 2 15 Mar 2018 78 CONTENTS Doc 7 02 15 Rev 4 Intentionally left blank ...
Страница 2190: ...AIRCRAFT Exhaust DA 42 NG AMM Page 4 15 Mar 2018 78 00 00 Doc 7 02 15 Rev 4 Intentionally left blank ...
Страница 2192: ...AIRCRAFT Exhaust DA 42 NG AMM Page 102 15 Mar 2018 78 00 00 Doc 7 02 15 Rev 4 Intentionally left blank ...
Страница 2195: ...AIRCRAFT DA 42 NG AMM Oil Cooling Doc 7 02 15 Rev 4 79 TITLE Page 1 15 Mar 2018 CHAPTER 79 OIL COOLING ...
Страница 2196: ...AIRCRAFT Oil Cooling DA 42 NG AMM Page 2 15 Mar 2018 79 TITLE Doc 7 02 15 Rev 4 Intentionally left blank ...
Страница 2198: ...AIRCRAFT Oil Cooling DA 42 NG AMM Page 2 15 Mar 2018 79 CONTENTS Doc 7 02 15 Rev 4 Intentionally left blank ...
Страница 2202: ...AIRCRAFT Oil Cooling DA 42 NG AMM Page 102 15 Mar 2018 79 00 00 Doc 7 02 15 Rev 4 Intentionally left blank ...
Страница 2208: ...AIRCRAFT Oil Cooling DA 42 NG AMM Page 206 15 Mar 2018 79 00 00 Doc 7 02 15 Rev 4 Intentionally left blank ...
Страница 2209: ...AIRCRAFT DA 42 NG AMM Starting Doc 7 02 15 Rev 4 80 TITLE Page 1 15 Mar 2018 CHAPTER 80 STARTING ...
Страница 2210: ...AIRCRAFT Starting DA 42 NG AMM Page 2 15 Mar 2018 80 TITLE Doc 7 02 15 Rev 4 Intentionally left blank ...
Страница 2212: ...AIRCRAFT Starting DA 42 NG AMM Page 2 15 Mar 2018 80 CONTENTS Doc 7 02 15 Rev 4 Intentionally left blank ...
Страница 2227: ...AIRCRAFT DA 42 NG AMM Turbo Charger Doc 7 02 15 Rev 4 81 TITLE Page 1 15 Mar 2018 CHAPTER 81 TURBO CHARGER ...
Страница 2228: ...AIRCRAFT Turbo Charger DA 42 NG AMM Page 2 15 Mar 2018 81 TITLE Doc 7 02 15 Rev 4 Intentionally left blank ...
Страница 2230: ...AIRCRAFT Turbo Charger DA 42 NG AMM Page 2 15 Mar 2018 81 CONTENTS Doc 7 02 15 Rev 4 Intentionally left blank ...
Страница 2236: ...AIRCRAFT Turbo Charger DA 42 NG AMM Page 6 15 Mar 2018 81 00 00 Doc 7 02 15 Rev 4 Intentionally left blank ...
Страница 2238: ...AIRCRAFT Turbo Charger DA 42 NG AMM Page 102 15 Mar 2018 81 00 00 Doc 7 02 15 Rev 4 Intentionally left blank ...
Страница 2252: ...AIRCRAFT Turbo Charger DA 42 NG AMM Page 6 15 Mar 2018 81 01 00 Doc 7 02 15 Rev 4 Intentionally left blank ...
Страница 2254: ...AIRCRAFT Turbo Charger DA 42 NG AMM Page 102 15 Mar 2018 81 01 00 Doc 7 02 15 Rev 4 Intentionally left blank ...
Страница 2263: ...AIRCRAFT DA 42 NG AMM Wiring Diagrams Doc 7 02 15 Rev 4 92 TITLE Page 1 15 Mar 2018 CHAPTER 92 WIRING DIAGRAMS ...
Страница 2264: ...AIRCRAFT Wiring Diagrams DA 42 NG AMM Page 2 15 Mar 2018 92 TITLE Doc 7 02 15 Rev 4 Intentionally left blank ...
Страница 2266: ...AIRCRAFT Wiring Diagrams DA 42 NG AMM Page 2 15 Mar 2018 92 CONTENTS Doc 7 02 15 Rev 4 Intentionally left blank ...
Страница 2269: ...AIRCRAFT DA 42 NG AMM Wiring Diagrams Title Drawing No Rev No No of Sheets Doc 7 02 15 Rev 4 92 00 00 Page 3 15 Mar 2018 ...
Страница 2270: ...AIRCRAFT Wiring Diagrams DA 42 NG AMM Page 4 15 Mar 2018 92 00 00 Doc 7 02 15 Rev 4 Intentionally left blank ...
Страница 2288: ......
Страница 2320: ......
Страница 2322: ......