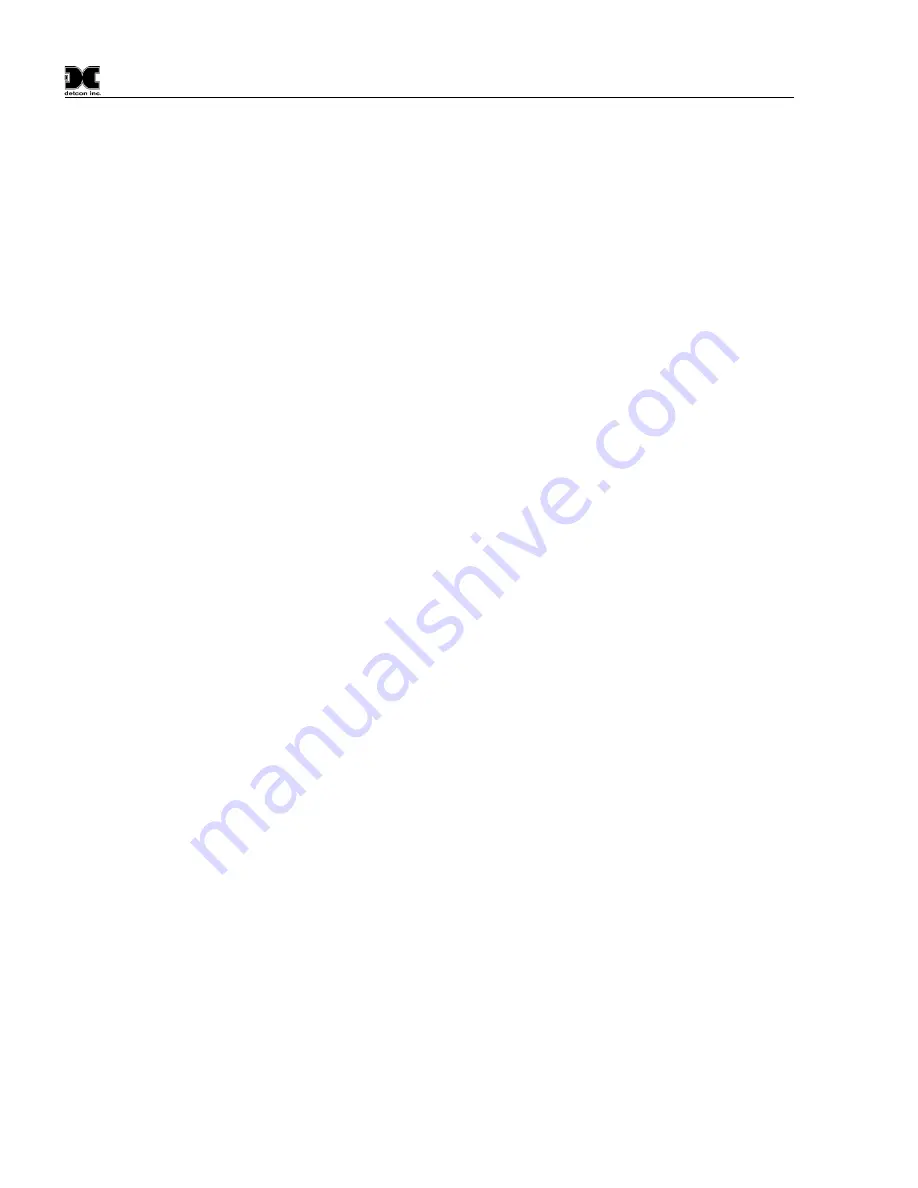
DM-634C Oxygen Sensor Assembly
DM-634C O2 Sensor Instruction Manual Rev. .066
Page 18 of 25
3.10
Program Features
Detcon MicroSafe™ toxic gas sensors incorporate a comprehensive program to accommodate easy operator
inter- face and fail-safe operation. Program features are detailed in this section. Each sensor is factory tested,
programmed, and calibrated prior to shipment.
Over Range
When the sensor detects gas greater than 25.0% O2, it will cause the display to flash
“25.0 % O2”
on and off.
Sensor Fault
If either of the wires connecting the sensor cell to the connector board should fail and cause an open circuit, the
sensor will go into a fault condition.
“SENSOR FAULT”
.
Calibration Fault
If during calibration the sensor circuitry is unable to attain the proper adjustment for span, the sensor will enter
into the calibration fault mode and cause the display to alternate between the sensor’s current status reading
and the calibration fault screen which appears as:
“CAL FAULT”
.
Fail-Safe/Fault Supervision
Detcon MicroSafe™ sensors are programmed for fail-safe operation. Any fault condition will activate the
fault relay, illuminate the fault LED, and cause the display to read its corresponding fault condition:
“SENSOR FAULT”
, or
“CAL FAULT”
. A
“SENSOR FAULT”
will also cause the mA output to drop to
zero (0) mA.
Sensor Life
The sensor life feature is a reference based on signal output from the sensor cell. When a sensor life of 25% or
less remains, the sensor cell should be replaced within a reasonable maintenance schedule.
3.11
RS-485 Protocol
Model TP-624C MicroSafe™ sensors feature Modbus™ compatible communications protocol and are
addressable via rotary dip switches for multi-point communications. Other protocols are available. Contact the
Detcon factory for specific protocol requirements. Communication is two wire, half duplex 485, 9600 baud, 8
data bits, 1 stop bit, no parity, with the sensor set up as a slave device. A master controller up to 4000 feet
away can theoretically poll up to 256 different sensors. This number may not be realistic in harsh
environments where noise and/or wiring conditions would make it impractical to place so many devices on
the same pair of wires. If a multi-point system is being utilized, each sensor should be set for a different
address. Typical address settings are: 01, 02, 03, 04, 05, 06, 07, 08, 09, 0A, 0B, 0C, 0D, 0E, 0F, 10, 11, etc.
In most instances, RS-485 ID numbers are factory set or set during installation before commissioning. If
required, the RS-485 ID number can be set via rotary dip switches located on the pre-amp circuit board.
However, any change to the RS-485 ID number would require the sensor housing to be opened, thus
declassification of the area would be required. See section 3.5.5-f for details on changing the RS-485 ID
number.
The following section explains the details of the Modbus™ protocol that the DM-634 MicroSafe™ sensor
supports.
Code 03 - Read Holding Registers, is the only code supported by the transmitter. Each transmitter contains 6
holding registers which reflect its current status.