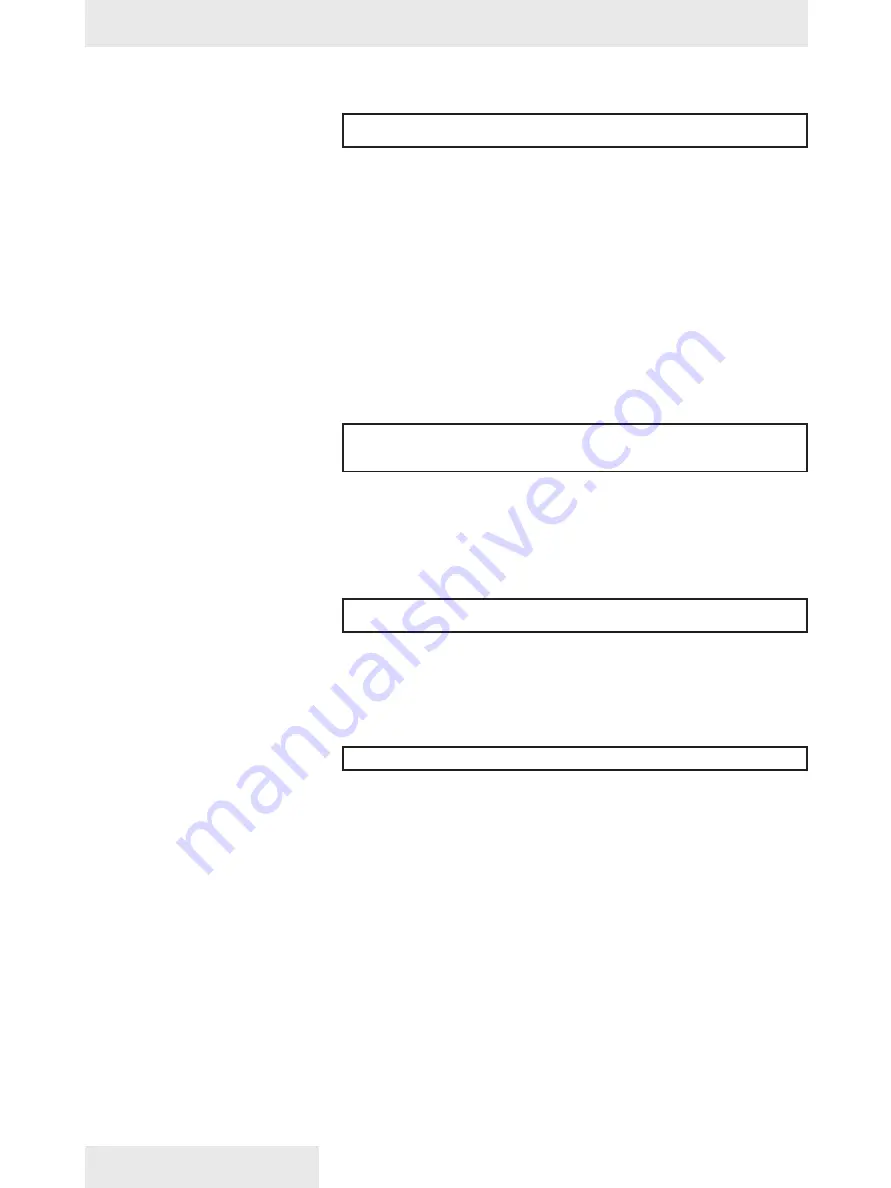
43
If pressures are incorrect, remove replenishing relief valve pilot and increase or decrease
pressure as required. (One full turn on adj. screw will cause pressure to change approx-
imately 50 PSI) (3.4 bar). Re-torque locknut to 20-25 in-lbs. (2.3-2.8 Nm).
Note: There is no servo relief valve adjustment. Increasing or decreasing repl. pres-
sure will cause both servo and repl. pressure to change by the same amount.
9. Set pump to full displacement and set the test stand relief valve at approx. 2000 PSI
(138 bar). Set the pump compensator at 1000 PSI (69 bar). Set the shuttle relief valve
pilot cap to 220 ± 20 PSI (15.2 ± 1.4 bar) above case pressure and secure with locknut
and acorn nut.
10. Stroke pump to center position and observe repl. pressure. It should rise to the value
in step 8 above.
11. Slowly cycle the pump across center several times while observing repl. pressure
drops to 220 ± 20 PSI (15.2 ±1.4 bar) while on stroke, and rises to 350 ± 20 PSI (24.1 ±
1.4 bar) at zero stroke, to verify shuttle operation.
12. Set pump to compensate at 5000 PSI (345 bar). Record repl. and servo pressure.
Servo Pressure-Minus Case Pressure-660 to 770 PSI (45.5 to 53.1 bar).
Repl. Pressure-Minus Case Pressure-350 ± 20 PSI (24.1 ± 1.4 bar).
13. Set pump to compensate at minumum PSI. Servo pressure should return to 455 to
570 PSI (3.3 to 39.3 bar).
Note: After completing step 13, proceed with pump control test and adjustment. Refer
to the goldcup control manual #S1-AM030 for your control type. Continue with step
14 after testing controls.
14. Adjust pump displacement for full volume and adjust system pressure to 6000 PSI
(413.8 bar).**Adjust compensator from 6000 PSI to 3000 PSI (413.8 to 206.9 bar) to min-
imum pressure. At each pressure, stroke rotary servo input shaft to the full position on
each side of center. Cam indicator should remain on or very near the zero position with
no oscillation. System pressure should not vary from Port "A" to Port "B" more than 150
PSI (10.3 bar) and not oscillate.
Minimum compensator pressure should be under 500 PSI (34.5 bar)
**Caution: DO NOT hold pump at 6000 PSI (413.8 bar) for longer than one minute at
any time. This is only an intermittent pressure rating.
15. Set compensator for 1000 PSI (69 bar) when fully compensated, UNLESS OTHER-
WISE SPECIFIED. Increase and decrease system pressure above and below compensa-
tor setting. When system pressure is above compensator setting, the pump should de-
stroke and not oscillate. When the system pressure is below the compensator setting, the
pump should stroke to full volume.
16. Check pump for external leaks. No external leaks permitted.
Note: Refer to Manual S1-AM030 for Control Service information.
BASIC PUMP TEST
(continued)
TEST PROCEDURES
Содержание Goldcup Series
Страница 9: ...9 ASSEMBLY TOOL DRAWINGS Note Dimensions in are mm T 1 T 2 MATERIAL CRS 1 DIA X 2 5 8 25 4mm 66 68 mm...
Страница 25: ...25 ASSEMBLY PROCEDURES Figure 11 Seal Kit S23 00135 Valve Block After 7 93 S23 12770...
Страница 40: ...40 HYDRAULIC CIRCUIT Revised...
Страница 41: ...41 HYDRAULIC CIRCUIT Revised...
Страница 47: ...47 NOTES...