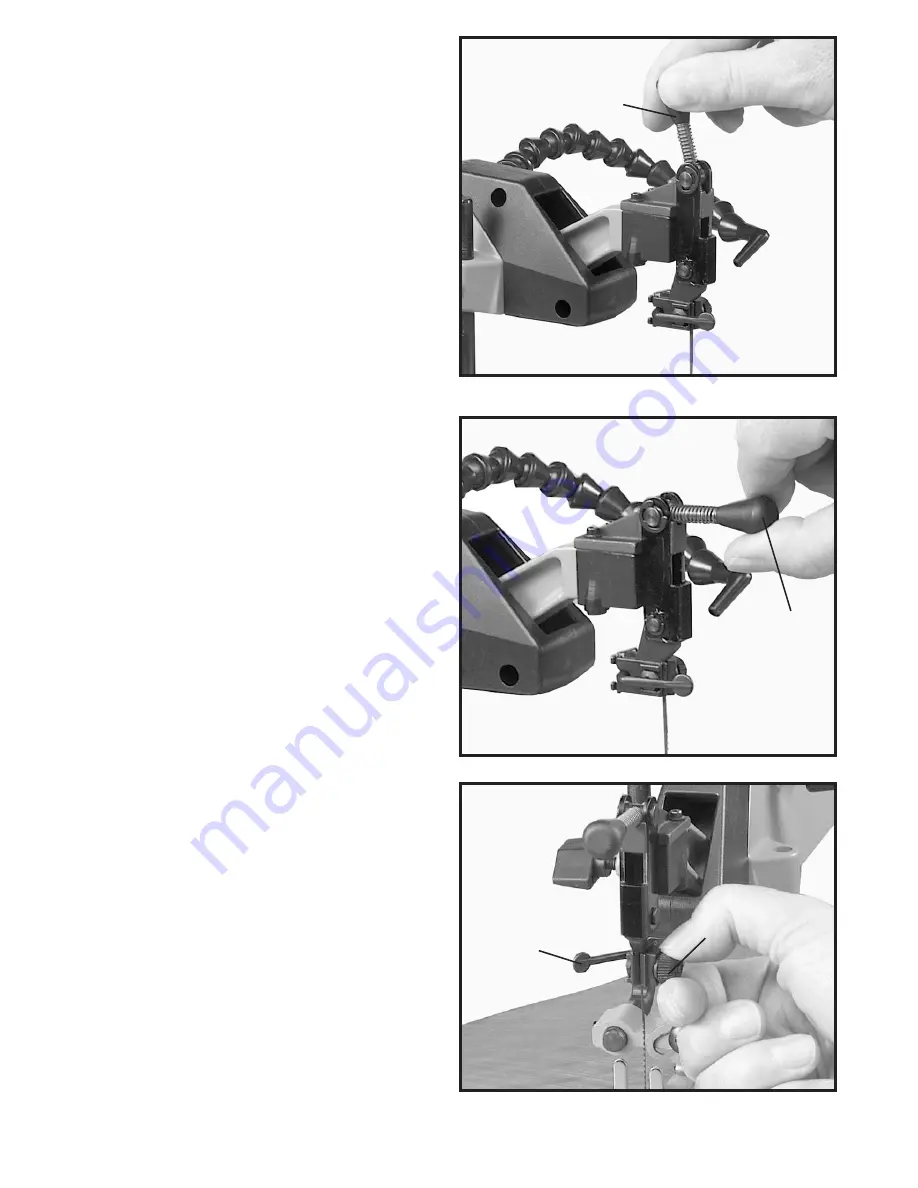
10
ADJUSTING BLADE
TENSION
Tension is applied to the blade when the blade tension
lever (A) Fig. 7, has been adjusted and is in the vertical
position as shown. When the blade tension lever (A) is
moved to the horizontal position, as shown in Fig. 8,
blade tension is released.
To adjust blade tension, position lever (A) in the vertical
position, as shown in Fig. 7. To increase tension, turn
lever (A) clockwise and to decrease tension turn lever (A)
counterclockwise. When adjusting tension, turn lever
one-quarter of a turn at a time.
NOTE:
It is necessary to
adjust the blade tension only when the blade is removed
from both the upper and lower blade holders and a new
or different type of blade is used. It is not necessary to
adjust blade tension when the blade is removed and
replaced in only the upper blade holder as in performing
inside cutting operations. After desired tension is
obtained, position tension lever (A) in the horizontal
position, as shown in Fig. 7.
Adjusting the blade for proper tension is usually
accomplished by trial and error. One method is to pull
back on the blade tension lever (A) Fig. 8, the blade
should start to have tension (resistance) when the blade
tension lever is half way between open Fig. 8, and closed
Fig. 7 positions. Finer blades require more tensioning
while thicker blades require less tension.
ADJUSTING CLAMPING
ACTION OF UPPER AND
LOWER BLADE HOLDER
CHUCK
Different widths of scroll saw blades will make it
necessary to adjust the clamping action of the upper and
lower blade holders. It should be noted, however, that
very little adjustment is necessary and very little
clamping force is required to hold the blade satisfactorily.
As a rule of thumb, looking down at the table with the
table insert slot in the 6 o’clock position, resistance on
the blade locking lever should be felt when the upper
blade locking lever reaches the 7 o’clock position, or
when the lower blade locking lever reaches the 5 o’clock
position.
1.
Move the blade locking lever (A) Fig. 9, to the rear
(open) position, as shown.
2.
Turn chuck clamping knob (B) Fig. 9, clockwise to
tighten and counterclockwise to loosen the clamping
action of the blade holder chuck. Very little movement of
knob (B) will be necessary.
NOTE:
Only the upper chuck
is shown. Clamping action of the lower chuck is adjusted
in the same manner and can be accessed by removing
dust cup shown in Fig. 24.
Fig. 7
A
Fig. 8
A
Fig. 9
A
B