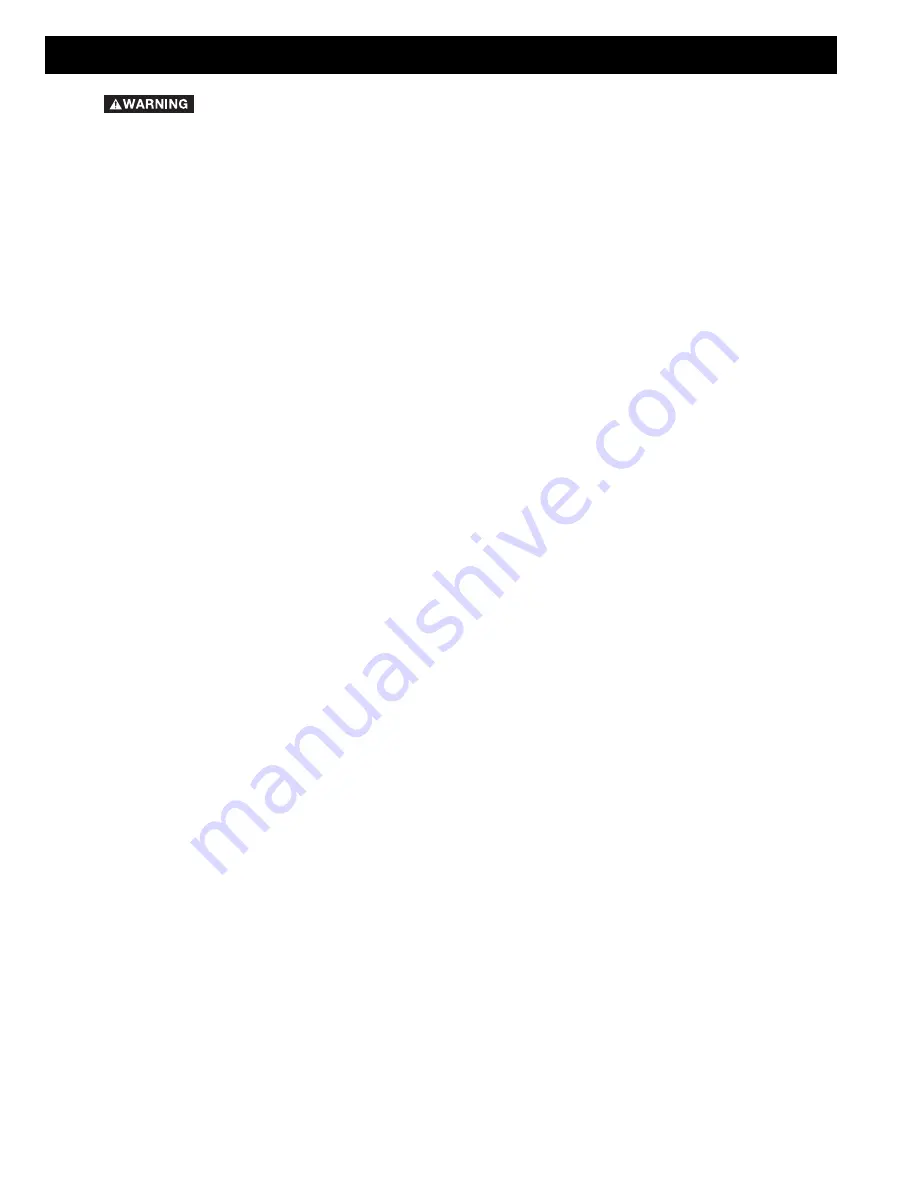
4
ADDITIONAL SAFETY RULES FOR PLANERS
1.
DO NOT OPERATE THIS MACHINE
until it is
completely assembled and installed according to
the instructions. A machine incorrectly assembled
can cause serious injury.
2.
OBTAIN ADVICE
from your supervisor, instructor,
or another qualified person if you are not
thoroughly familiar with the operation of this
machine. Knowledge is safety.
3.
FOLLOW ALL WIRING CODES
and recommend-
ed electrical connections to prevent shock or
electrocution.
4.
KEEP KNIVES SHARP
and free from rust and
pitch. Dull or rusted knives work harder and can
cause kickback.
5.
NEVER TURN THE MACHINE “ON”
before clearing
the table of all objects (tools, scraps of wood, etc.).
Flying debris can cause serious injury.
6
.
NEVER TURN THE MACHINE “ON”
with the work-
piece contacting the cutterhead. Kickback can
occur.
7.
SECURE THE MACHINE TO A SUPPORTING SUR-
FACE
to prevent the machine from sliding, walking
or tipping over.
8.
PROPERLY SECURE THE KNIVES IN THE CUTTER-
HEAD
before turning the power “ON”. Loose
blades may be thrown out at high speeds causing
serious injury.
9.
LOCK THE SPEED SETTING SECURELY
before
feeding the workpiece through the machine.
Changing speeds while planing can cause kick-
back.
10.
AVOID AWKWARD OPERATIONS AND HAND POSI-
TIONS.
A sudden slip could cause a hand to move
into the knives.
11.
KEEP ARMS, HANDS, AND FINGERS
away from
the cutterhead, the chip exhaust opening, and the
feed rollers to prevent severe cuts.
12.
NEVER REACH INTO THE CUTTERHEAD AREA
while the machine is running. Your hands can be
drawn into the knives.
13.
DO NOT STAND IN LINE OF THE WORKPIECE.
Kickback can cause injury
.
14.
ALLOW THE CUTTERHEAD TO REACH FULL SPEED
before feeding a workpiece. Changing speeds
while planing can cause kickback.
15.
WHEN PLANING BOWED STOCK,
place the concave
(cup down) side of the stock on the table and cut
with the grain to prevent kickback.
16.
DO NOT FEED A WORKPIECE
that is warped,
contains knots, or is embedded with foreign
objects (nails, staples, etc.). Kickback can occur.
17.
DO NOT FEED A SHORT, THIN, OR NARROW
WORKPIECE INTO THE MACHINE
. Your hands can
be drawn into the knives and/or the workpiece can
be thrown at high speeds. See the “OPERATION”
section of this instruction manual for details.
18.
DO NOT FEED A WORKPIECE
into the outfeed end of
the machine. The workpiece will be thrown out of
the opposite side at high speeds.
19.
REMOVE SHAVINGS ONLY
with the power “OFF” to
prevent serious injury.
20.
PROPERLY SUPPORT LONG OR WIDE WORK-
PIECES.
Loss of control of the workpiece can cause
serious injury.
21.
NEVER PERFORM LAYOUT, ASSEMBLY
or set-up
work on the table/work area when the machine is
running. Serious injury will result.
22.
TURN THE MACHINE “OFF”, DISCONNECT IT FROM
THE POWER SOURCE,
and clean the table/work
area before leaving the machine.
LOCK THE
SWITCH IN THE “OFF” POSITION
to prevent un-
authorized use. Someone else might accidentally
start the machine and cause injury to themselves
or others.
23.
ADDITIONAL INFORMATION
regarding the safe
and proper operation of power tools (i.e. a safety
video) is available from the Power Tool Institute,
1300 Sumner Avenue, Cleveland, OH 44115-2851
(www.powertoolinstitute.com). Information is also
available from the National Safety Council, 1121
Spring Lake Drive, Itasca, IL 60143-3201. Please
refer to the American National Standards Institute
ANSI 01.1 Safety Requirements for Woodworking
Machines and the U.S. Department of Labor
Regulations.
FAILURE TO FOLLOW THESE RULES MAY RESULT IN SERIOUS INJURY.
SAVE THESE INSTRUCTIONS.
Refer to them often
and use them to instruct others.
Содержание ShopMaster TP400LS
Страница 19: ...19 NOTES ...