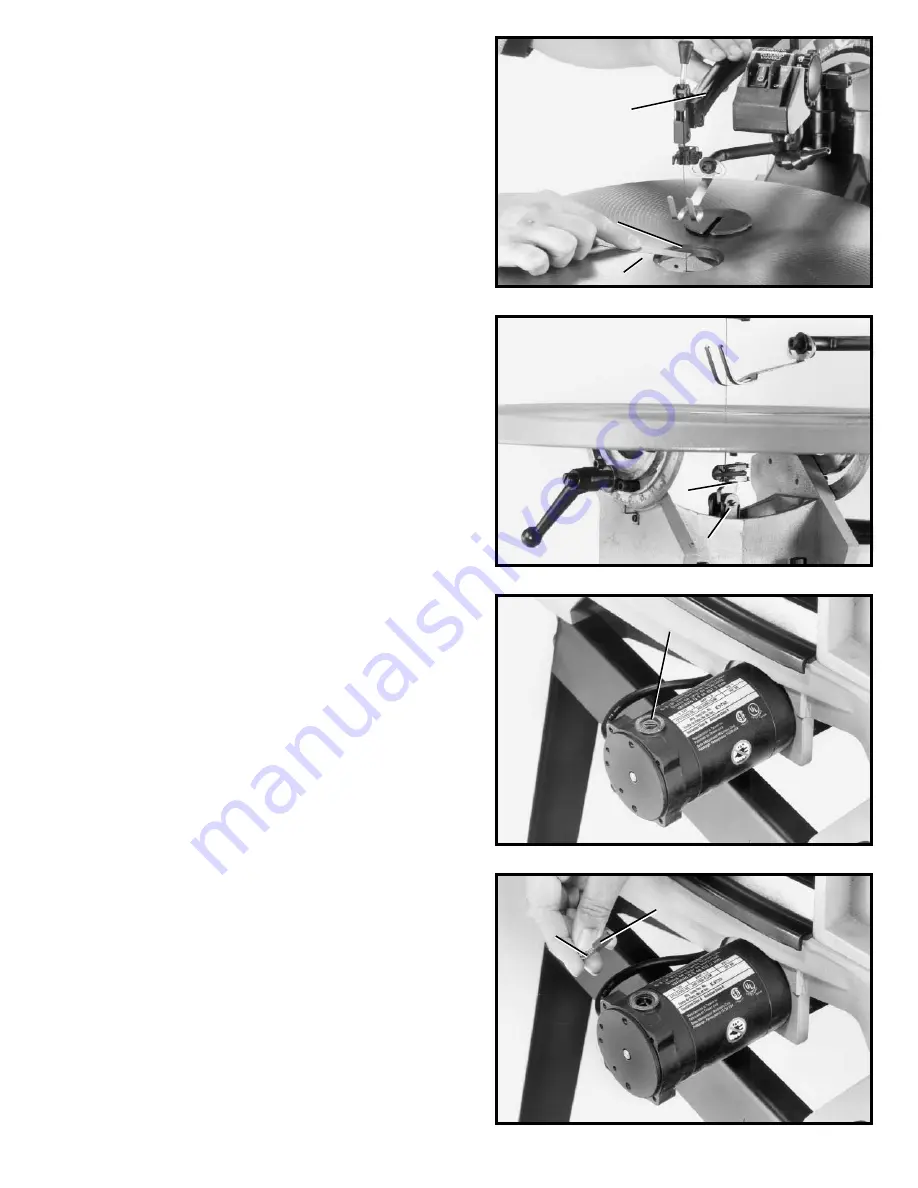
15
BRUSH INSPECTION
AND REPLACEMENT
CAUTION: BEFORE INSPECTING THE BRUSH-
ES, DISCONNECT THE MACHINE FROM THE
POWER SOURCE.
Brush life varies. It depends on the load on
the motor. Check the brushes after the first 50
hours of use for a new machine or after a new
set of brushes has been installed. After the
first check, examine them after about 10
hours of use until such time that replacement
is necessary.
The brush holders, one of which is shown at
(A) Fig. 34, are located i-n the motor housing
opposite each other. Fig. 35 illustrates one of
the brushes removed for inspection. When the
carbon (B) on either brush is worn to 3/16" in
length or if either spring (C) or shunt wire is
burned or damaged in any way, replace both
brushes. If the brushes are found serviceable
after removing, reinstall them in the same
position as removed.
Fig. 32
Fig. 33
Fig. 34
Fig. 35
ALIGNING LOWER BLADE
HOLDER WITH UPPER
BLADE HOLDER
The lower blade holder has been aligned with
the upper blade holder at the factory and fur-
ther alignment should not be necessary; how-
ever, to check or adjust the alignment, pro-
ceed as follows:
1. MAKE CERTAIN THE MACHINE IS DIS-
CONNECTED FROM THE POWER SOURCE.
2. Remove the table insert and place a small
straight edge (A) Fig. 32, against the side of
the saw blade (B) as shown in Fig. 32.
3. While holding the straight edge (A) Fig. 32,
against the saw blade, carefully move the cut-
ting arm (E) up and down in a cutting motion.
CAUTION: Do not use excessive force on the
cutting arm. The saw blade should contact the
straight edge during the entire cutting stroke.
4. If an alignment is necessary, rotate adjust-
ment screw (C) Fig. 33, to move the lower
blade holder (D) left or right, until the saw
blade is in consistent contact with the straight
edge during the entire cutting stroke.
A
B
C
D
A
B
C
E
Содержание 40-650
Страница 3: ...3 ...