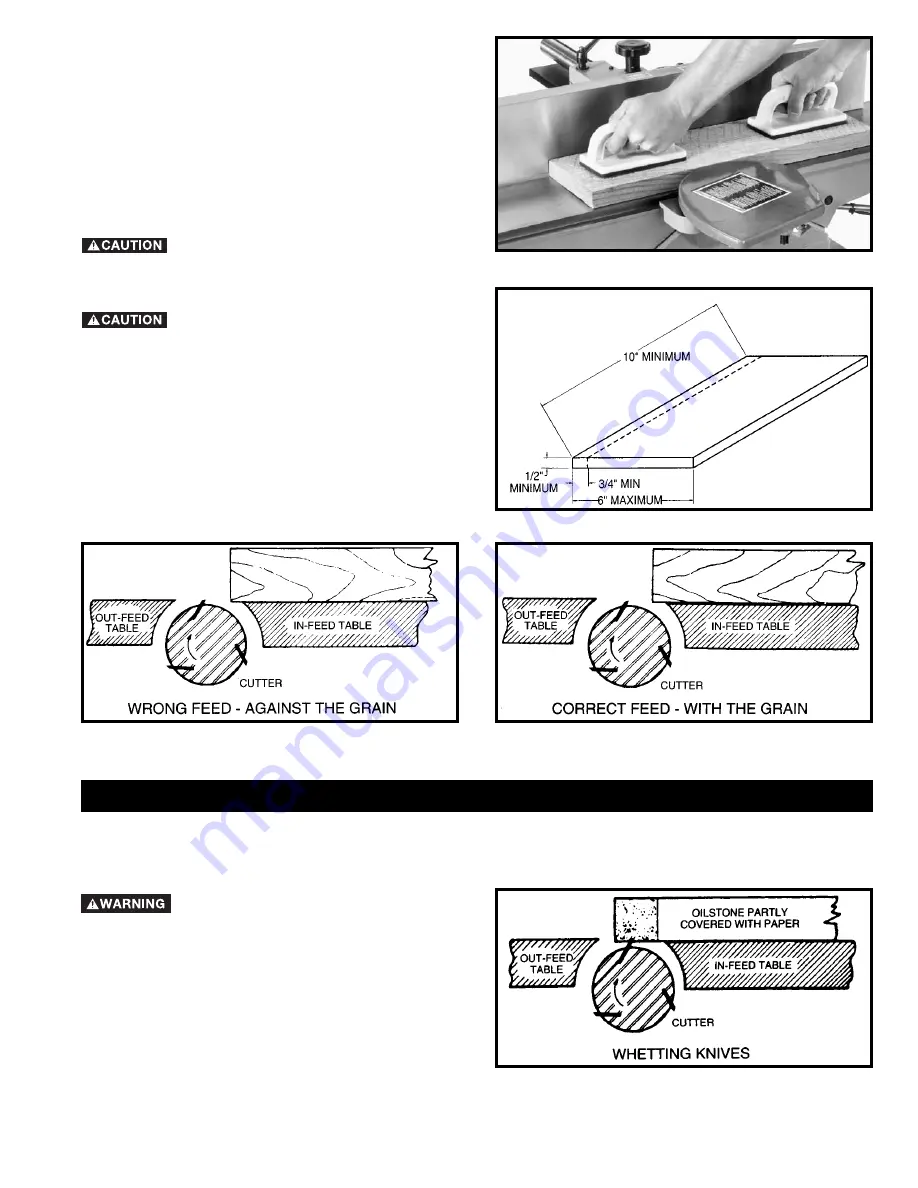
21
Fig. 66
Fig. 67
Fig. 68
Fig. 69
After considerable use, the knives will become dull and it will not be possible to do accurate work. Unless
badly damaged by running into metal or other hard material, the knives may be sharpened as follows:
WHETTING KNIVES
DISCONNECT MACHINE FROM POWER
SOURCE
.
Use a fine carborundum stone, cover it partly with paper
as indicated in Fig. 59 to avoid marking the table. Lay
the stone on the infeed table, lower the table and turn
the cutterhead forward until the stone lies flat on the
bevel of the knife as shown. Hold the cutterhead from
turning, and whet the beveled edge of the knife, stroking
lengthwise by sliding the stone back and forth across
the table. Do the same amount of whetting on each of
the three knives.
Fig. 70
MAINTENANCE AND REPAIRS
SURFACING WARPED PIECES
If the wood to be surfaced is dished or warped, take
light cuts until the surface is flat. Avoid forcing such
material down against the table; excessive pressure will
spring it while passing the knives, and it will spring back
and remain curved after the cut is completed.
SURFACING SHORT
OR THIN WORK
WHEN SURFACING SHORT OR THIN
PIECES, ALWAYS USE PUSH BLOCKS TO MINIMIZE
ALL DANGER TO THE HANDS.
Fig. 66, illustrates using
the Delta Push Blocks properly.
DO NOT PERFORM SURFACING
OPERATIONS ON MATERIAL SHORTER THAN 10
INCHES, NARROWER THAN 3/4 INCH, WIDER THAN
6 INCHES, OR LESS THAN 1/2 INCH THICK (REFER
TO FIG. 67).
DIRECTION OF GRAIN
Avoid feeding work into the jointer against the grain as
shown in Fig. 68. The result will be chipped and
splintered edges. Feed with the grain as shown in Fig.
69, to obtain a smooth surface.
MINIMUM AND
MAXIMUM SURFACING
DIMENSIONS