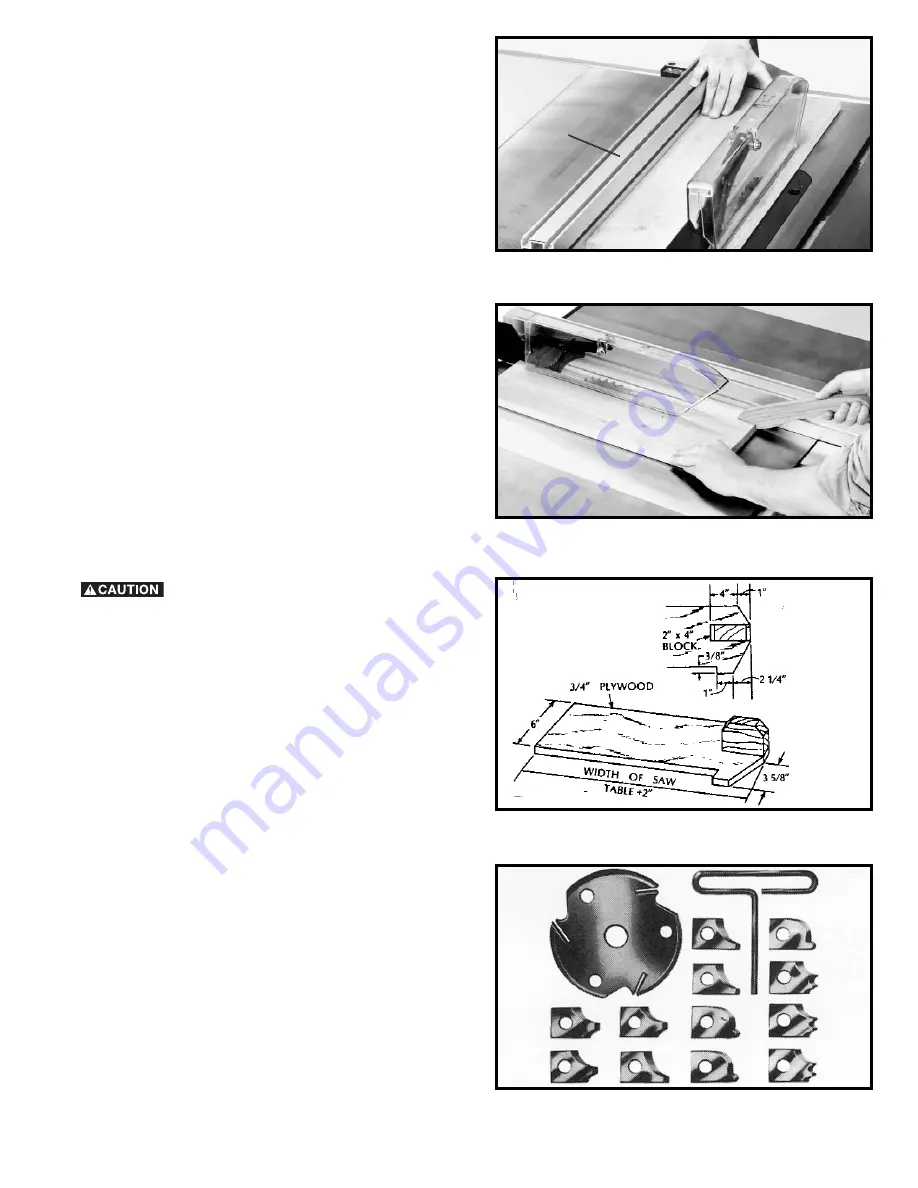
25
RIPPING
Ripping is the operation of making a lengthwise cut
through a board, as shown in Fig. 82, and the rip fence (A)
is used to position and guide the work. One edge of the
work rides against the rip fence while the flat side of the
board rests on the table. Since the work is pushed along
the fence, it must have a straight edge and make solid
contact with the table. The saw guard must be used. The
guard has anti-kickback fingers to prevent wood
kickback, and a splitter to prevent the wood kerf from
closing and binding the blade.
Start the motor and advance the work holding it down
and against the fence. Never stand in the line of the saw
cut when ripping. Hold the work and push it along the
fence and into the saw blade as shown in Fig. 82. The
work can then be fed through the saw blade with one or
two hands. After the work is beyond the saw blade and
anti-kickback fingers, the hand is removed from the work.
When this is done the work will either stay on the table,
tilt up slightly and be caught by the rear end of the guard
or slide off the table to the floor. Alternately, the feed can
continue to the end of the table, after which the work is
lifted and brought back along the outside edge of the
fence. The cut-off stock remains on the table and is not
touched with the hands until the saw blade is stopped,
unless it is a large piece allowing safe removal. When
ripping boards longer than three feet, it is recommended
that a work support be used at the rear of the saw to keep
the workpiece from falling off the saw table.
If the ripped work is less than 4 inches wide,
a push stick should always be used to complete the feed,
as shown in Fig. 83. The push stick can easily be made
from scrap material as explained in the section
“CONSTRUCTING A PUSH STICK.”
When ripping material under 2 inches in width, a flat
pushboard is a valuable accessory since ordinary type
sticks may interfere with the blade guard. That flat
pushboard can be made as shown in Fig. 83A.
USING ACCESSORY
MOULDING CUTTERHEAD
Moulding is cutting a shape on the edge or face of the
work. Cutting mouldings with a moulding cutterhead in
the circular saw is a fast, safe and clean operation. The
many different knife shapes available make it possible for
the operator to produce almost any kind of mouldings,
such as various styles of corner moulds, picture frames,
table edges, etc.
The moulding head consists of a cutterhead in which can
be mounted various shapes of steel knives, as shown in
Fig. 84. Each of the three knives in a set is fitted into a
groove in the cutterhead and securely clamped with a
screw. The knife grooves should be kept free of sawdust,
which would prevent the cutter from seating properly.
Fig. 82
A
Fig. 83A
Fig. 83
Fig. 84
Содержание 36-650
Страница 31: ...NOTES 31...