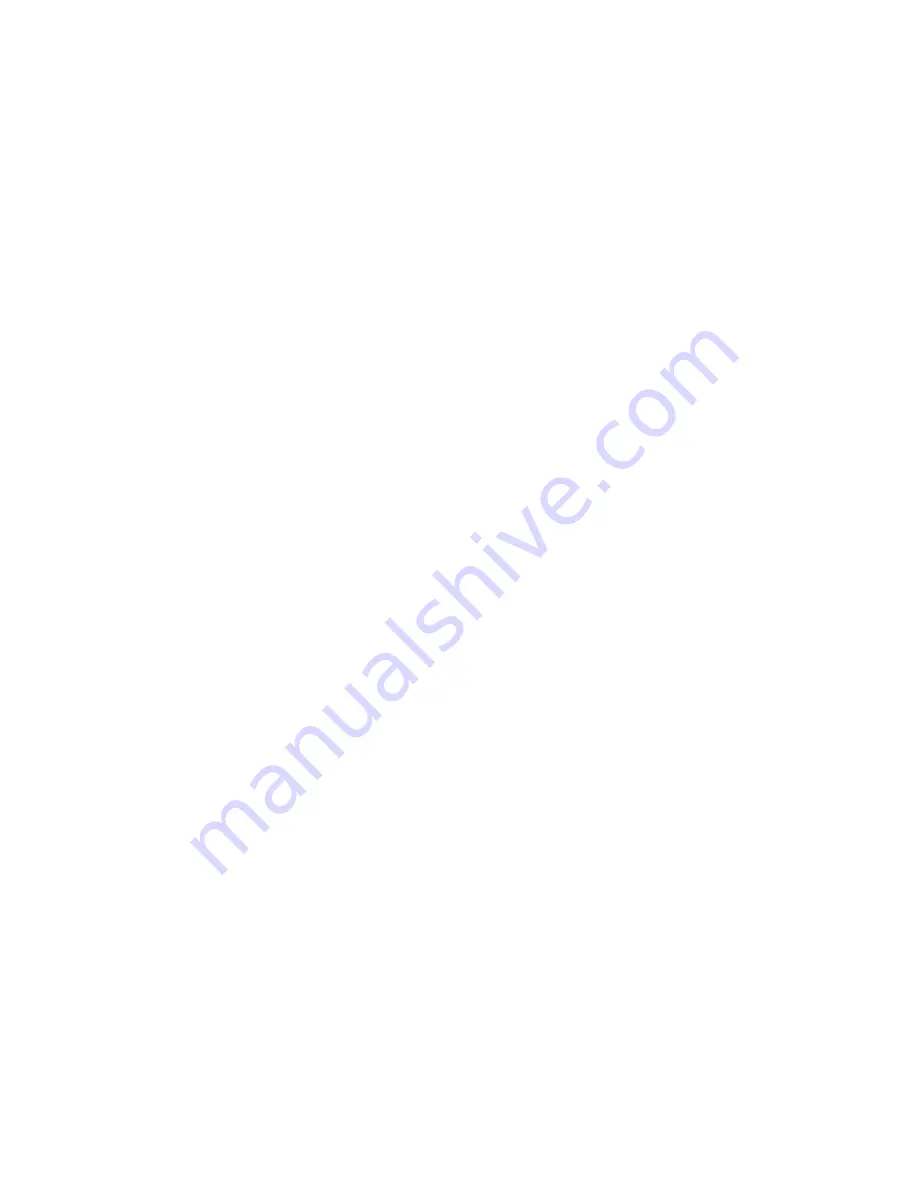
3
ADDITIONAL SAFETY RULES
FOR COMPOUND SLIDE SAWS
1.
USE ONLY CROSSCUT SAW BLADES. WHEN
USING CARBIDE TIPPED BLADES MAKE SURE THEY
HAVE A ZERO DEGREE OR NEGATIVE HOOK ANGLE.
DO NOT USE BLADES WITH DEEP GULLETS AS
THEY CAN DEFLECT AND CONTACT GUARD.
2.
DO NOT
operate the tool until it is completely
assembled and installed according to the instructions.
3.
IF YOU ARE NOT
thoroughly familiar with the
operation of compound slide saws, obtain advice from
your supervisor, instructor or other qualified person.
4.
SLIDE CUTTING BY PULLING
the saw towards the
operator can be dangerous, causing the saw to kick
upwards and towards the operator. Always
PUSH
the
saw forward, away from the operator, and towards the
fence when slide cutting.
5.
WHEN USING THE SAW AS A MITER SAW AND
MAKING CHOP CUTS, MAKE SURE
the saw sliding
mechanism is locked in place to prevent the saw from
kicking towards the operator.
6.
BE CAREFUL
when folding or unfolding legs. Pivot
points are also pinch points.
7.
PLACE
stand on flat and level surface.
8.
MAKE CERTAIN
that extension work supports are
properly locked in place before operating tool.
9.
DO NOT
stand on work table or use support
extension as a ladder or scaffolding.
10.
MAXIMUM
workpiece weight limitation – 50 lbs. per
table extension.
11.
NEVER PLACE YOUR HANDS INSIDE
the area
designated as a hazard zone while the tool is being
operated.
12.
ALWAYS
hold the work firmly against the fence and
table.
DO NOT
perform any operation free hand.
13.
IMPORTANT:
If the workpiece you are cutting causes
your hand to be within 4 inches of the saw blade, the
workpiece must be clamped to the table before cutting.
14.
BE SURE
blade is sharp, runs freely and is free of
vibration.
15.
ALLOW
the motor to come up to full speed before
starting cut.
16.
KEEP
the motor air slots clean and free of chips.
17.
ALWAYS MAKE SURE
all clamp handles are tight
before cutting.
18.
BE SURE
blade and blade flanges are clean and
that arbor screw is tightened securely.
19.
USE
only blade flanges specified for your saw.
20.
NEVER
use blades larger or smaller in diameter than
recommended. Recommended size of blade is 10
″
in
diameter.
21.
NEVER
apply lubricants to the blade while it is
running.
22.
ALWAYS
check the blade for cracks or damage
before operation. Replace cracked or damaged blade
immediately.
23.
USE ONLY
blades rated for operation of at least
5000 RPM.
24.
ONLY
use blades with 5/8
″
diameter arbor holes.
25.
USE
the blade guard at all times.
26.
ALWAYS
keep the lower blade guard in place and
operating properly.
27.
ALWAYS
keep hands out of path of saw blade.
28.
NEVER
reach around saw blade.
29.
MAKE SURE
blade is not contacting workpiece
before switch is turned on.
30.
NEVER
lock the switch in the “ON” position.
31.
IMPORTANT:
After completing cut, release power
switch and wait for coasting blade to stop before
returning saw to raised position.
32.
THE USE
of attachments and accessories not
recommended by Delta may result in the risk of injuries.
33.
TURN OFF
tool and make sure blade has come to a
complete stop before removing or securing workpiece,
changing workpiece angle or changing the angle of the
blade.
34.
NEVER
cut ferrous metals or masonry.
35.
NEVER
recut small pieces.
36.
PROVIDE
adequate support to the sides of the saw
table for long workpieces.
37.
NEVER
use the tool in an area with flammable liquids
or gases.
38.
NEVER
use solvents to clean plastic parts. Solvents
could possibly dissolve or otherwise damage the material.
Only a soft, damp cloth should be used to clean plastic
parts.
39.
DISCONNECT
tool from power source before
servicing or changing blades.
(continued next page)
Содержание 36-240
Страница 32: ...32 NOTES...