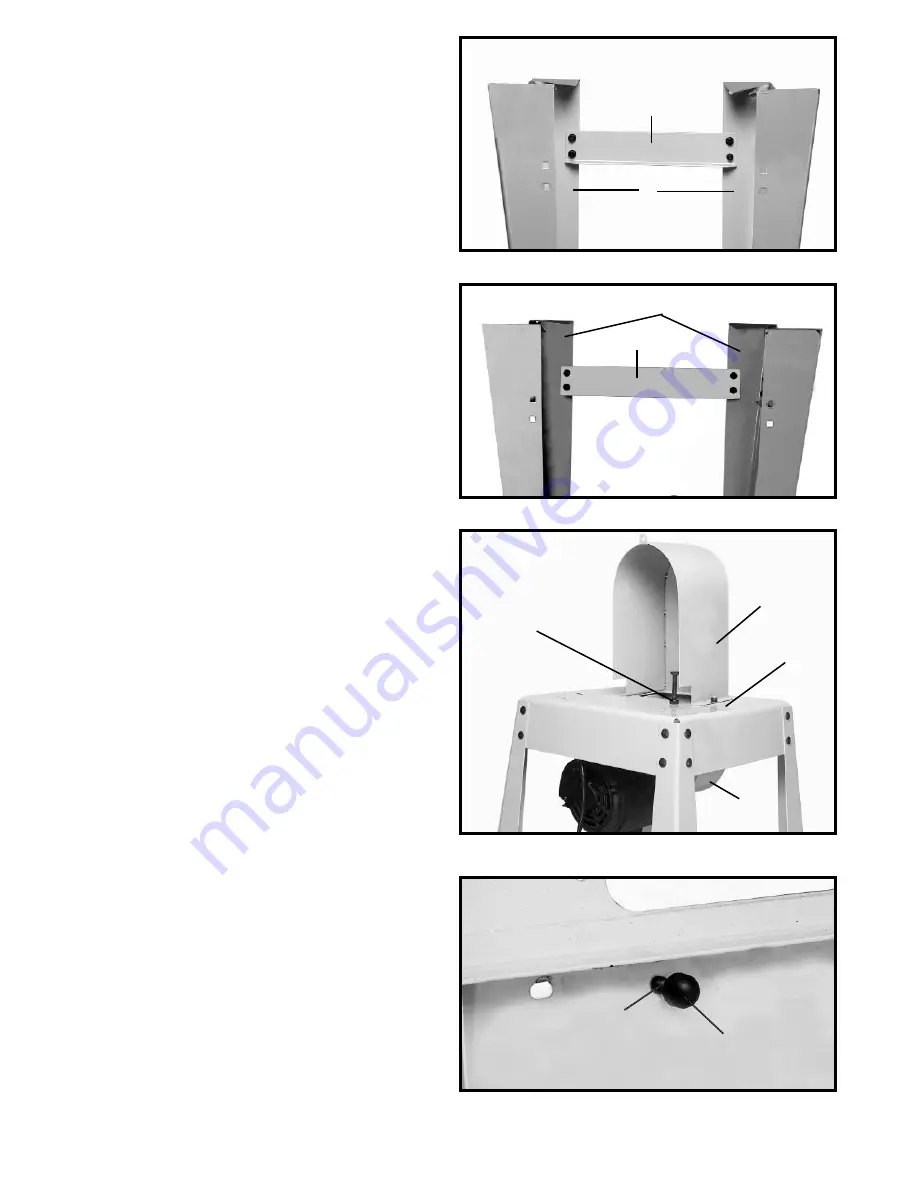
12
14. Align the four holes in the short brace (A) Fig. 14,
with the four holes in the two legs (B).
15. Insert a M8x1.25x16mm carriage head bolt through
the hole in the stand and the hole the short brace.
16. Thread a M8x1.25 flange nut onto the screw.
NOTE:
DO NOT COMPLETELY TIGHTEN STAND HARDWARE
AT THIS TIME.
17. Repeat this process for the three remaining holes in
the short brace.
18. Attach the remaining short brace to the opposite
side of the stand in the same manner.
Fig. 14
Fig. 15
19. Align the four holes in the long brace (A) Fig. 15, with
the four holes in the two legs (B).
20. Insert a M8x1.25x16mm carriage head bolt through
the hole in the stand and the hole in the long brace.
21. Thread a M8x1.25 flange nut onto the screw.
NOTE:
DO NOT COMPLETELY TIGHTEN STAND HARDWARE
AT THIS TIME.
22. Repeat this process for the three remaining holes in
the long brace.
23. Attach the remaining long brace to the opposite side
of the stand in the same manner.
24. Turn the stand over so that it is resting on its legs.
25. Thread a M8x1.25 hex nut onto a M8x1.25x80mm
hex head screw approximately 1/4".
26. Thread the M8x1.25x80mm hex head screw into the
hole (A) Fig. 16, in the top of the stand.
27. Place the damping cap (A) Fig. 16A onto the
threaded end of the screw (C).
28. Insert the two threaded studs on the lower pulley
guard (C) Fig 16, through the two holes in the top of the
stand (B).
29. Align the two holes in the upper pulley guard (D) Fig.
16, with the two threaded studs on the lower pulley
guard (C). Place the upper pulley guard on the studs of
the lower pulley guard.
30. Thread an M8x1.25 hex flange nut onto each of the
studs and tighten securely.
31. Make sure the stand is level and tighten all stand
hardware at this time.
Fig. 16
A
B
A
C
B
D
A
B
Fig. 16A
A
C
Содержание 28-206
Страница 23: ...23 NOTES...