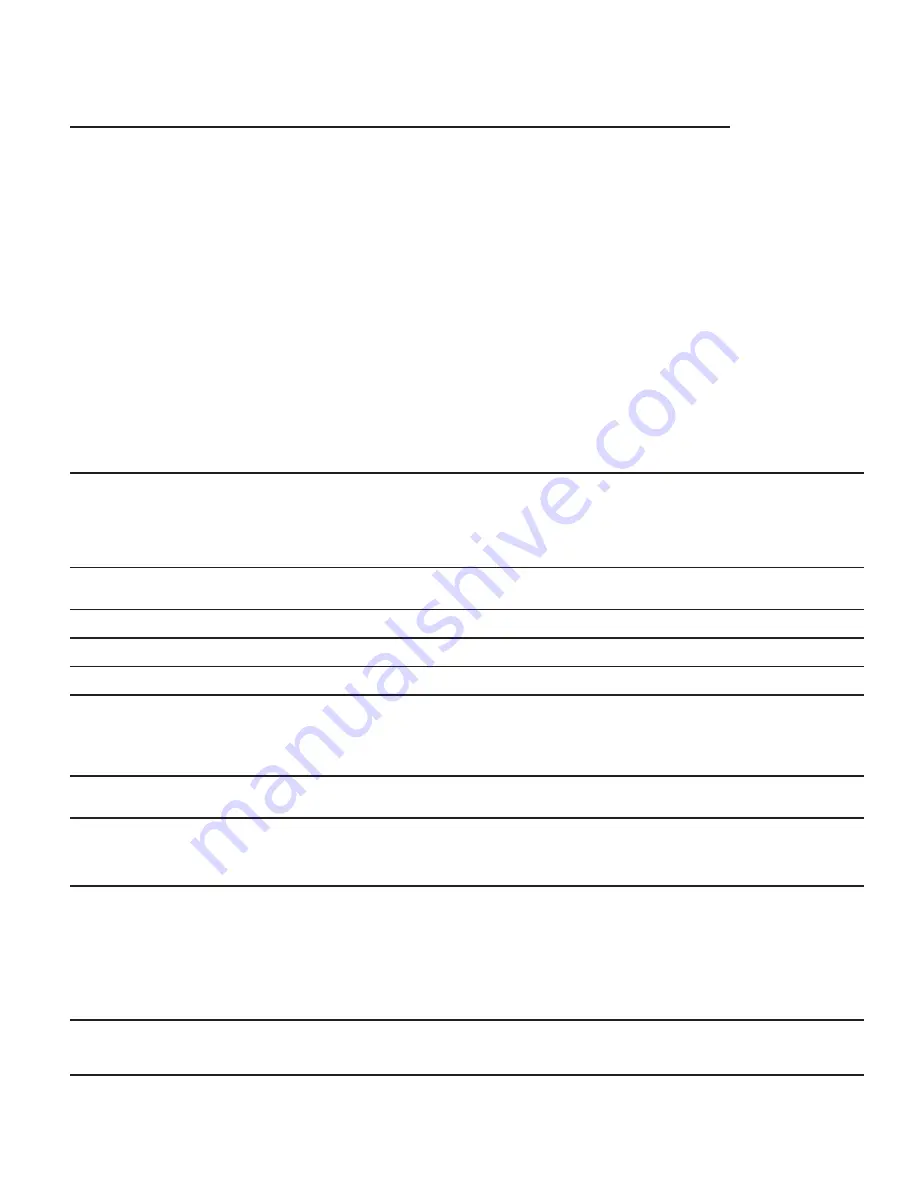
9
DIAGNOSIS AND MAINTENANCE
PROBLEM
PROBABLE CAUSE
SOLUTION
Low Pressure
Worn nozzle
Replace nozzle of proper size.
Belt slippage.
Tighten or replace; use correct belt.
Air leak in inlet plumbing.
Use PTFE liquid or tape.
Pressure gauge inoperative or not
Check pressure with new guage and replace as needed.
registering accurately.
Relief valve stuck partially plugged or
Clean and reset relief valve to system pressure
improperly adjusted.
and correct by-pass. Check supply tank for contamination.
Worn seat or valves.
Clean or replace with valve kit.
Inlet suction strainer clogged or
Use adequate size for inlet pump connection
improprly sized.
and fluid being pumped. Clean frequently.
Worn seals. Abrasives in pumped
Install and maintain proper filter, check line
fluid, severe cavitation; inadequate
size and flow available to pump. Install a C.A.T.
water supply, stressful inlet conditions.
Fouled or dirty inlet or discharge valves.
Clean inlet and discharge valve assemblies.
Worn inlet or discharge valves.
Replace with valve kit.
Leaky discharge hose.
Replace hose. Check connections.
Pulsation, pump runs
Faulty Pulsation Dampener
Check precharge (should be 30-50%) of system
extremely rough, pressure low
.
pressure or replace as needed.
Restricted inlet or air entering inlet plumbing.
Check filters and clean as needed. Check fittings and use
PTFE liquid or tape for air tight connection.
Stuck inlet or discharge valve
Clean or replace valve. Check supply tank for contamination.
Water leakage from under
Worn seals
Replace with seal kit, check inlet pressure and system
the manifold
temperature, use Thermo Valve in by- inlet pressure regulator
in inlet line.
Oil leak between crankcase
Worn crankcase seals
Replace crankcase seals
and pumping section *Slight leakage
.
Oil leaking in area of crankshaft
Worn crankshaft seal
Replace damaged seals.
Bad bearing
Replace bearing.
Excessive play in the end of
Worn bearing
Replace bearing.
t
he crankshaft.
Water in crankcase
Humid air condensing into water
Change oil every 3 months or 500 hours intervels using
inside of the crankcase
premium grade 10W30 Non-detergent hydraulic oil,
(other approved oil every month or 200 hours.)
Leaking of crankcase seals or
Replace seals. Follow proper installation procedure.
seals installed backward
Contact pump supplier for crankcase servicing.
Oil leaking at the rear portion
Damaged or improperly installed oil guage,
Replace oil gauge, crankcase cover or drain plug o-ring.
of the crankcase
crankcase cover, or drain plug o-ring
Thread in oil guage and drain plug hand tight to avoid
extruding o-ring.
Loud knocking noise in pump
Pulley loose on crankshaft
Check key and tighten screw
Worn bearing, connecting rod or crankshaft.
Consult pump supplier for crankcase servicing.
Stressful inlet conditions.
Install C.A.T.
Frequent or premature failure
Cracked or scored plungers
Replace plungers
of the packing
Abrasive material in the fluid being pumped
Install proper filtration on pump inlet plumbing.
Check supply tank for contamination.
Excessive pressure and/or temperature
Check pressure and fluid inlet temperature; be sure they are
of fluid being pumped.
within specified range.
Over pressure of inlet or discharge
Reduce pressure per specifications.
Running pump dry.
DO NOT RUN PUMP WITHOUT WATER!
Strong surging at the inlet
Foreign particles in the inlet or discharge
Check for smooth surfaces on inlet and discharge valve seats.
and low pressure at the discharge side.
valve or worn inlet or discharge valves.
Replace with kit if pitted or worn. Check supply tank for
contamination, Install and regularly clean filter. Do not pump
abrasive fluids.