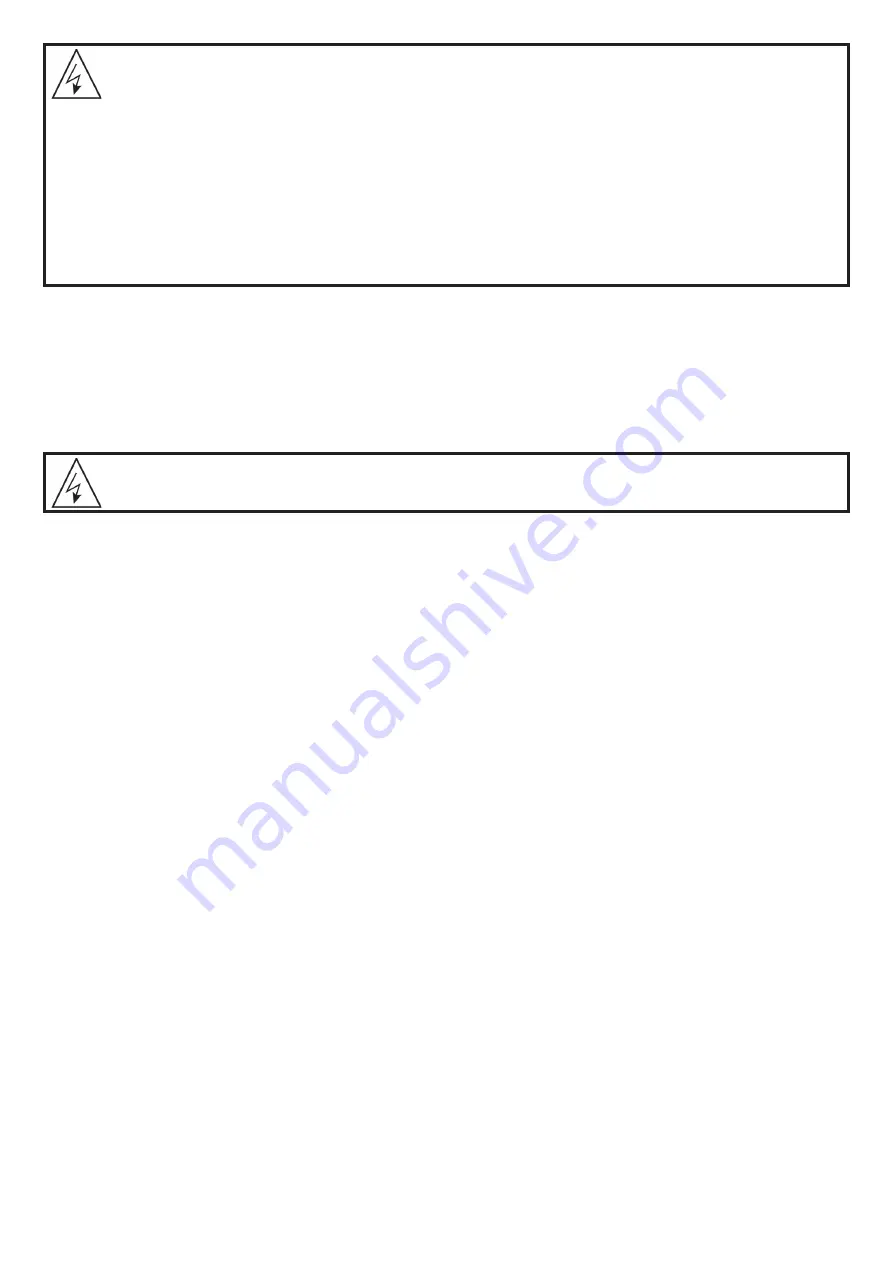
3
Fault Checks
(A)
Pump will not start:
(1) Manual Type
Check to ensure power is available and the outlet is switched ON.
Blown fuse or tripped circuit breaker (replace/reset or call an electrician).
If an extension lead is fitted, check connection.
Impeller jammed -
disconnect from power supply
, and ensure impeller is free to rotate.
Thermal cut-out switch has not reset (wait 5 minutes).
If pump does not start from new then the seal has possibly stuck due to the length of time it has been
standing since it was manufactured. In this case, disconnect from power supply, remove bottom strainer
and turn the impeller nut clockwise, this will release the initial friction on the seal and once the power is
connected will allow the pump to work.
(2) Auto Type (with float switch)
Check all in (1) above.
Float switch jammed against sump side wall.
Insufficient liquid to place the float switch in the ON position, i.e. higher than the horizontal.
(B)
Pump runs, but does not pump water or pumps insufficient water:
Insufficient liquid in sump.
Strainer, impeller and/or discharge pipework blocked.
Impeller damaged.
Air lock in discharge pipework. Ensure pump is filled with water.
Excessive back pressure or lift.
(C)
Pump will not stop:
(1) Manual Type
Must be switched off at the power supply.
(2) Auto Type (with float switch)
Float switch is prevented from moving to the fully down position.
Float switch may be faulty.
(D)
Pump runs for short periods only (the overload protection has tripped):
Some foreign body is clogging the impeller.
The liquid temperature is too high.
Pump operating in non submerged position or with no water movement around motor (not applicable to DC10).
Electrical fault.
Do not run the pump dry as this will damage the seal and reduce the life of the pump.
Where hair, lint or other string-like material may be in the water, the pump should be regularly checked. It might become
necessary sometimes to clean the suction strainer, impeller and/or discharge pipework.
With simple cleaning and regular examination this pump should give reliable service.
NOTE:
1. Long extension leads should be avoided as they often have insufficient current carrying capacity
to run electric motors, hence they can cause substantial voltage drop and operating problems.
2. Minimum voltage at the electric motor must not fall below 216 Volts for single phase, otherwise
motor damage may result which is not claimable under guarantee.
3. If the electrical fittings in your country make it necessary to remove the plug (where fitted) from
the lead fitted to the motor, care should be taken to ensure that the earth conductor green/
yellow in the lead is properly connected to a good earth. This work should be undertaken by a
suitably qualified person.
4. Expansion and contraction inside the motor due to heating and cooling is vented via the lead.
The lead end must never be sealed off, but must always be open to the atmosphere.
5. ALWAYS disconnect pump from power supply prior to commencing ANY maintenance or
adjustment.
NOTE:
If fitting an extension lead a QUALIFIED ELECTRICIAN should be consulted to ensure correct rating is provided.
Extension leads are not allowed for permanent installations.