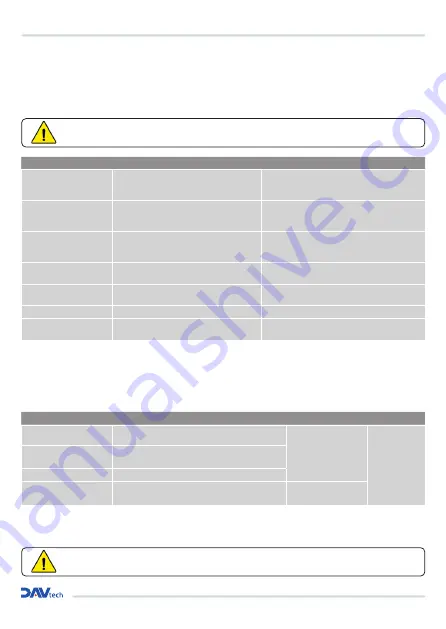
FAULT
POSSIBLE CAUSE
REMEDY
The needle metering
valve switches but no
lubricant is ejected
The feed pump is not supplying
lubricant
Consult the operating manual for the
feed pump
The needle metering
valve switches but no
lubricant is ejected
Material pressure too low
Increase pump pressure
The dispensing valve is
leaking
The control air pressure/counter-
pressure of the spring is too low
Increase the control air pressure,
reduce the material pressure, install
a stronger spring
The dispensing valve is
leaking
Defective seals
Replace seals
Air in the system
Air pockets in the grease container
Air pockets in the hoses
Loosen supply hose. Bleed system.
Reconnect supply hose.
Leaky valve
Defective seals
Replace seals
Irregular dispensing
No constant grease and air
Upstream installation of optional material
pressure regulator MDR
WHEN
WHAT
HOW
WHO
Weekly
Check valve for tightness
Visual
Qualified
personell
Weekly
Check all threaded connections and fittings
for leaks
Monthly
Check seals for damage and wear
Annually
Complete maintenance
Dismantle, clean and
replace seals
TRAINING OF PERSONNEL
Only trained and instructed personnel who have read and understood all points in the operating instructions may work on
the product. The personnel must also be able to control the operating states, and identify and implement the interrelated
safety aspects. Personnel in training may only work on the product under the supervision of qualified personnel.
5 TROUBLESHOOTING, FAULT RESOLUTION
6 MAINTENANCE
Needle metering valves are precision instruments that are not susceptible to faults, given proper handling, and operate
largely without maintenance, assuming that the application material is generally processed in clean condition, not
contaminated by foreign particles. We recommend the following maintenance intervals to optimise the service life:
The specified maintenance intervals are for single shift operation. Maintenance has to be carried out more often
depending on the field of application, medium and in case of operation in more than one shift.
CAUTION
All of the faults described below may only be resolved by trained, qualified personnel.
CAUTION All work on the system is basically only to be carried out when it is at a standstill. The pneumatic
and hydraulic systems have to be de-pressurised. The pressure gauges have to show 0 bar.
Installation and maintenance guide