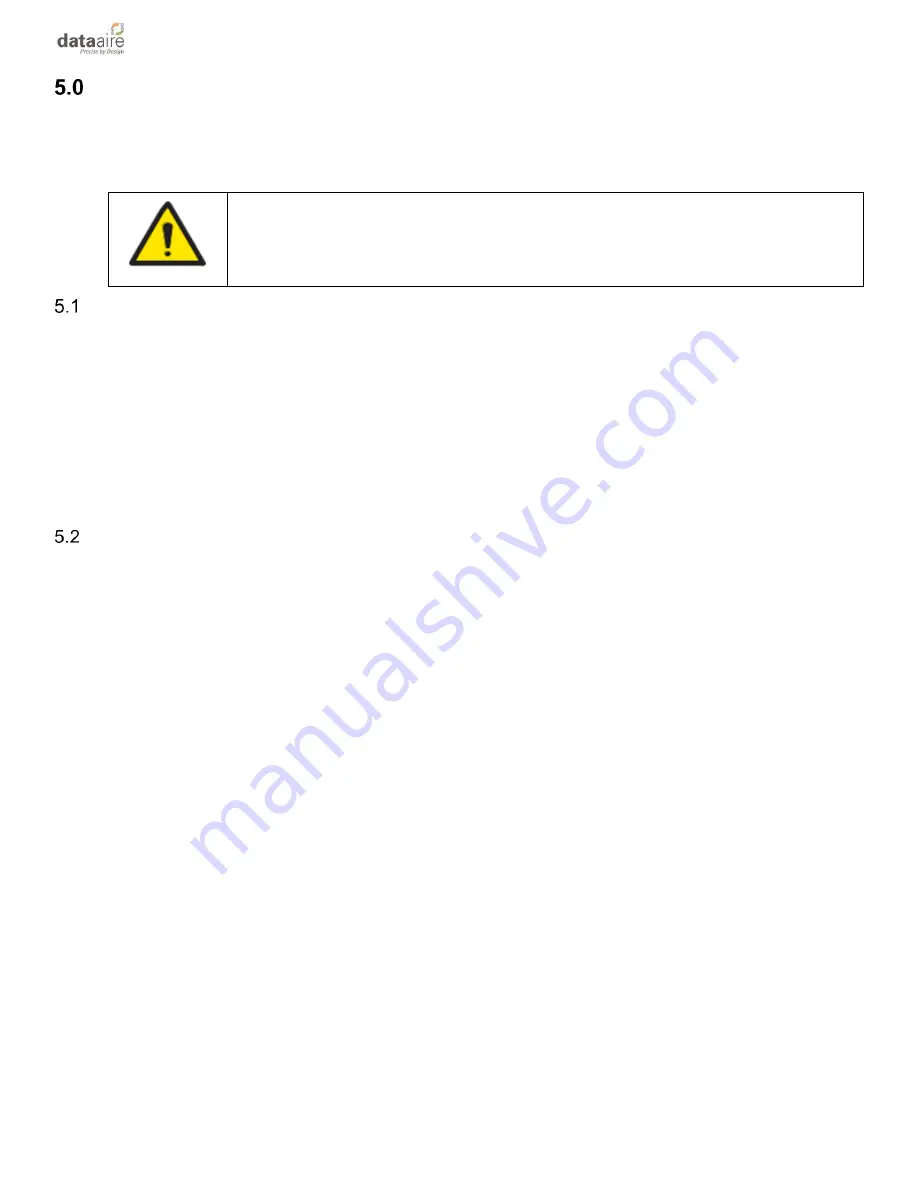
gForce Ultra IOM
47
CHARGING
These charging instructions apply to single and dual variable and fixed speed compressor circuit
models. The procedures are the same for each circuit but the requirement to follow the same steps for
the second circuit will be called out, where appropriate.
NOTICE:
R-410A use Polyol Ester oil (POE) oil that is prone to absorbing
moisture. Therefore, the system should never be left open to the atmosphere.
Charging/Installation Work Procedures
The basic installation work procedures are the same for R-410A but the working pressure for R-410A
is 1.6 times higher than for R-407C. Therefore, some of the piping, installation and tools are special.
Special Service Equipment for R-410A refrigerant
•
High pressure manifold gauge set suitable for R-410A pressure
•
High pressure recovery machine suitable for R-410A pressure
•
High pressure recovery tank suitable for R-410A pressure
(Ref: DOT 4BA400 or ABW400)
Triple Evacuation and Dehydration Procedure
Data Aire highly recommends a triple evacuation to be carried out on all Data Aire units to ensure the
highest quality moisture removal. Moisture prevents the proper operation of both the compressor and
the refrigeration system. Non-condensable and moisture reduces service life and increases
condensation pressure, which causes abnormally high discharge temperatures that can degrade the
lubricating properties of the oil. The risk of acid formation is also increased by non-condensable and
moisture and this condition can also lead to copper plating. These phenomena may cause both
mechanical and electrical compressor failure. The typical method for avoiding such problems is to triple
evacuate the system.
It is of the utmost importance that proper system evacuation and leak detection procedures be
employed. Good evacuation includes frequent vacuum pump oil changes and large diameter, short
hose connections to both high and low sides of the system (all refrigerant lines, suction line, discharge
line and liquid line) preferably using copper tubing, vacuum rated or braided hose.
All valves in the system, solenoid valves, electronic expansion valves, ball valves and service valves
(if the compressor is equipped), need to remain open during the vacuum procedures and the system
must be purged with nitrogen. We recommend using a solenoid magnet tool to hold the liquid line
solenoid valve(s) open during this procedure.
A deep vacuum gauge capable of registering pressure in microns must be attached to the system on
the liquid line service port before the EEV or TXV and should be at the farthest point in the system for
most accurate vacuum readings. A shut-off valve (suggest a Schrader valve core removal tool) between
the system and vacuum pump should be provided to allow the system pressure to be checked after
evacuation.
Содержание gForce Ultra
Страница 1: ......
Страница 123: ...gForceUltraIOM_11 2022 docx...