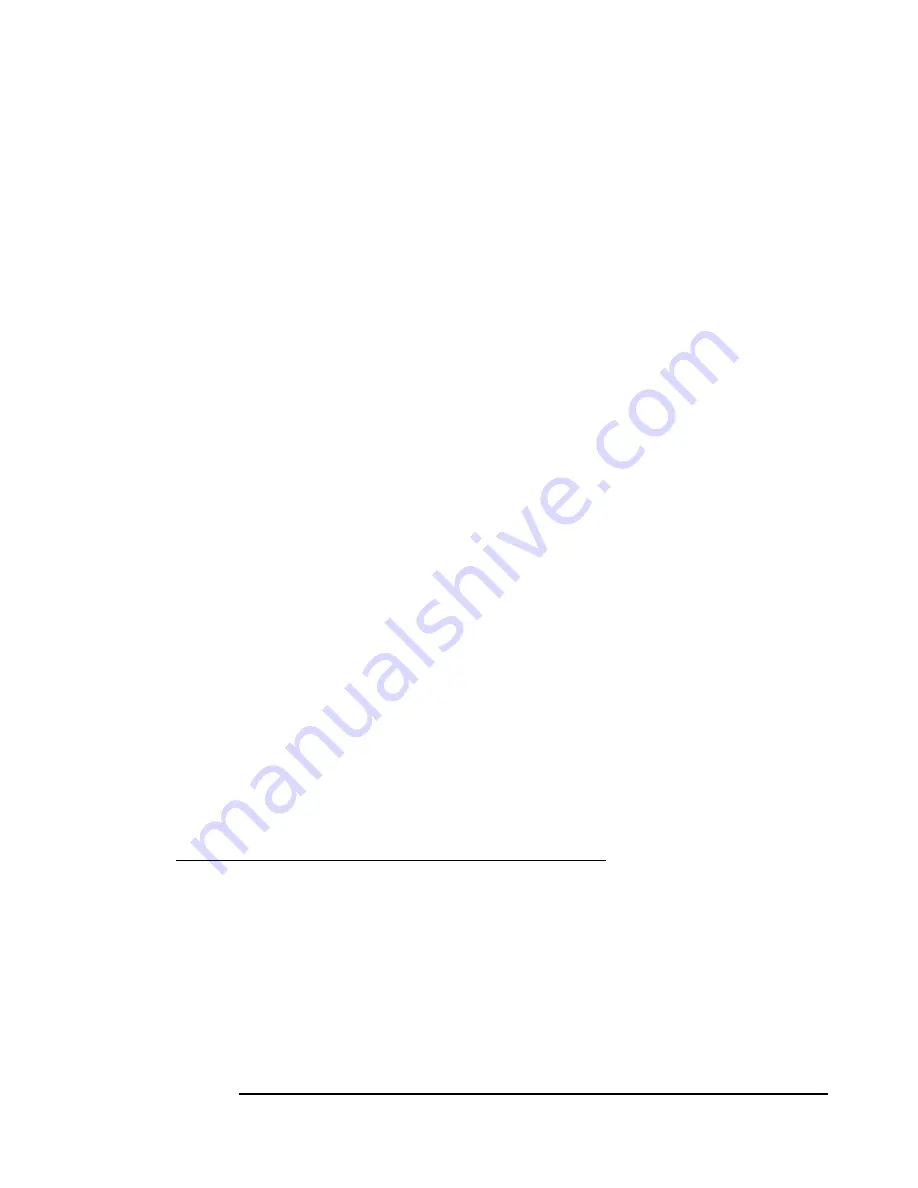
DE
DANIELS
ELECTRONICS
VT-4R150 VHF Project 25 Digital Transmitter Instruction Manual
3-1
3
Transmitter Assembly and Adjustment
The Transceiver RF and Digital Signal Processor module are mounted on the Transmitter Main
Board, and the Microprocessor board plugs into the Digital Signal Processor Board. Two ribbon
cables allow the Microprocessor board to make connection with the Main board. A metal shield is
soldered in place over the Transceiver RF module, and another shield is held in place over the
Digital Signal Processor and Microprocessor boards by screws. The RF Amplifier module is
secured on the Main Board by screws, and an enclosure is formed by an extruded aluminum shell
that slides over the Transmitter Main Board as illustrated in section 5.2). This shell also serves as a
heat sink to remove heat from the Amplifier module and for this reason, it is important that the four
screws that bond the shell to the amplifier module (Screws B in Section (5.2) be installed before
prolonged operation of the transmitter. Moreover, the surface of the Amplifier module that contacts
the shell should be clean and free of foreign material. The enclosure is completed by the installation
of front and rear plates, which are fastened to the Transmitter Main Board (see Transmitter Main
Board Manual for parts lists).
Transmitter alignment is performed on a module by module basis and detailed steps are provided in
the respective manuals. Alignment is simplified by using a SR-3 Sub rack, SM-3 System Monitor,
and RF extender cable to provide transmitter power and signal interconnection. Alternatively,
+9.5 Vdc and +13.8 Vdc as well as any required test signal may be applied directly to the
individual modules. Refer to the corresponding manuals for details.
3.1
Frequency Change
The transmitter is initially aligned at the factory for the frequency stamped on the 'Factory Set
Operating Frequency' label (see section 3.1). This label should list the frequency at which the last
complete transmitter alignment was performed. For a small frequency change, a simple channel
change (see section 2.2) may be all that is required. A larger frequency change may involve the
realignment of other modules. The frequency change in question is the accumulated frequency
change in relation to the frequency stamped on the label. For example, if the frequency is changed
by 0.5 MHz from that stamped on the label, then a second frequency change of 1 MHz in the same
direction would result in a total change of 1.5 MHz. The action taken would be based on the 1.5
MHz value. Failure to perform realignment after a large frequency change could result in unreliable
transmitter operation or transmitter operation that does not conform to the published specifications.
The allowable frequency change is summarized below.
Note: It is advisable to confirm these frequency ranges with the individual module manuals
notably the Amplifier and Synthesizer Module, as they are subject to change with updated
versions. The values in the module manuals take precedent over those tabulated (following
page).
Size
of
Frequency
Change
Modules
to
be
Aligned
Less than ± 1 MHz
No alignment required, check output power
Greater than ± 1 MHz
Transmitter Power Amplifier
3.2
Minor Frequency Change
Changes less than ± 1 MHz from a previously tuned working receive frequency will generally not
require any adjustment. Change the frequency using the Radio Programming Software package.
Verify that the Transmitter Output power is at the desired level.