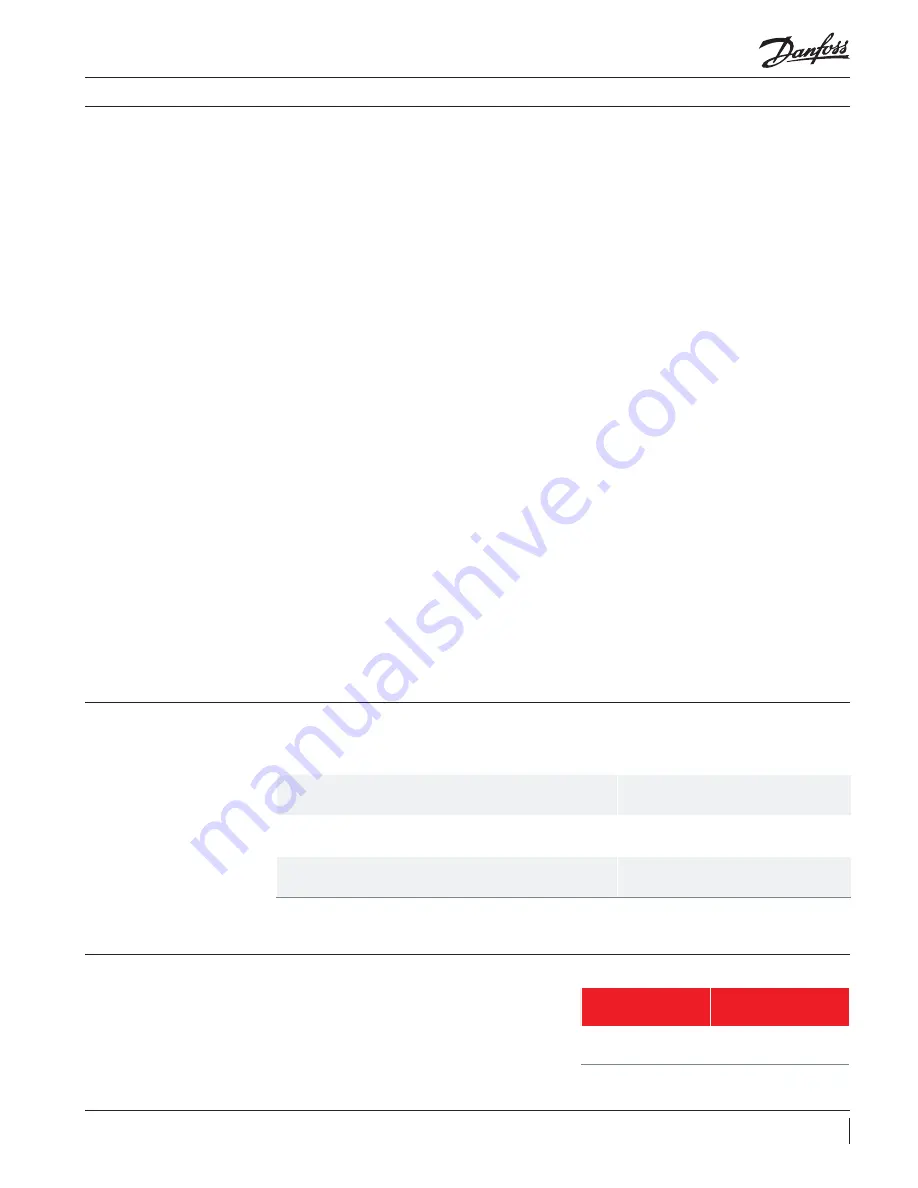
Application guidelines
45
FRCC.PC.014.A4.22
For brazing the suction and discharge connec-
tions, the following procedure is advised:
• Make sure that no electrical wiring is connect-
ed to the compressor.
• Protect the terminal box and compressor
painted surfaces from torch heat damage (see
diagram).
• Remove the Teflon gaskets when brazing roto-
lock connectors with solder sleeves.
• Use only clean refrigeration-grade copper
tubing and clean all connections.
• Use brazing material with a minimum of 5%
silver content.
• Purge nitrogen or CO
2
through the compres-
sor in order to prevent against oxidation and
flammable conditions. The compressor should
not be exposed to the open air for extended
periods.
• Use of a double-tipped torch is recommended.
• Apply heat evenly to area A until the brazing
temperature is reached. Move the torch to area
B and apply heat evenly until the brazing tem-
perature has been reached there as well, and
then begin adding the brazing material. Move
the torch evenly around the joint, in applying
only enough brazing material to flow the full
circumference of the joint.
• Move the torch to area C only long enough to
draw the brazing material into the joint, but
not into the compressor.
• Remove all remaining flux once the joint has
been soldered with a wire brush or a wet cloth.
Remaining flux would cause corrosion of the
tubing.
Ensure that no flux is allowed to enter into the
tubing or compressor. Flux is acidic and can cause
substantial damage to the internal parts of the
system and compressor.
The polyolester oil used in VSH compressors is
highly hygroscopic and will rapidly absorb mois-
ture from the air. The compressor must therefore
not be left open to the atmosphere for a long pe-
riod of time. The compressor fitting plugs shall be
removed just before brazing the compressor. The
compressor should always be the last component
brazed into the system
Before eventual unbrazing the compressor or any
system component, the refrigerant charge must
be removed from both the high- and low-pres-
sure sides. Failure to do so may result in serious
personal injury. Pressure gauges must be used to
ensure all pressures are at atmospheric level.
For more detailed information on the appropriate
materials required for brazing or soldering, please
contact the product manufacturer or distributor.
For specific applications not covered herein,
please contact Danfoss for further information.
Installation
System pressure test
Always use an inert gas such as nitrogen for
pressure testing. Never use other gasses such as
oxygen, dry air or acetylene as these may form an
inflammable mixture. Do not exceed the follow-
ing pressures:
Pressurize the system on HP side first then LP side
to prevent rotation of the scroll. Never let the
pressure on LP side exceed the pressure on HP
side with more than 73 psig.
Maximum compressor test pressure (low side)
483 psig for VSH088 & 117
438 psig for VSH170
Maximum compressor test pressure (high side)
645 psig
Maximum pressure difference between high and low side
of the compressor
537 psi
Leak detection
Leak detection must be carried out using a mix-
ture of nitrogen and refrigerant or nitrogen and
helium, as indicated in the table below. Never use
other gasses such as oxygen, dry air or acetylene
as these may form an inflammable mixture.
Pressurize the system on HP side first then LP
side.
Leak detection
with refrigerant
Leak detection
with a mass spectrometer
Nitrogen & R410A
Nitrogen & Helium