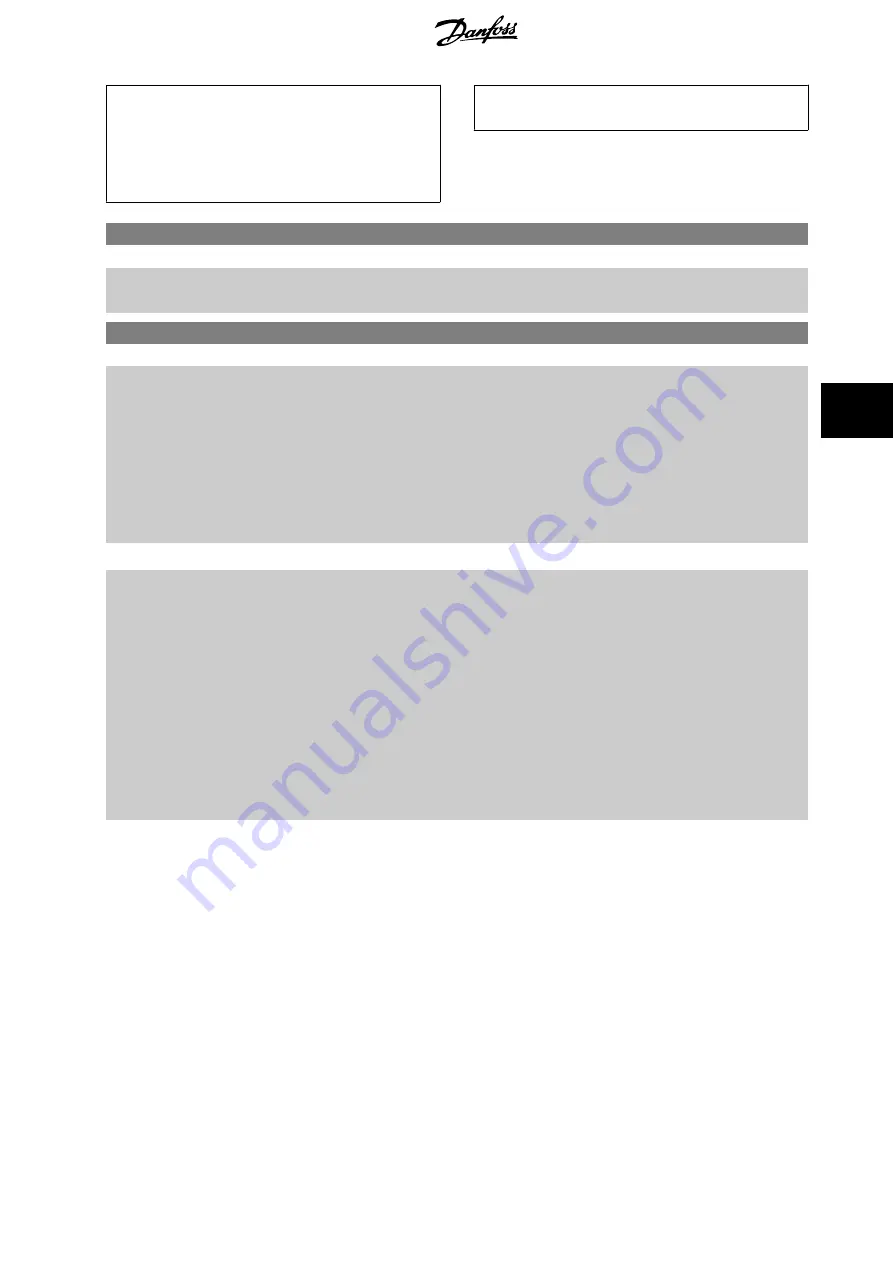
If one of the settings in parameter group 1-2* Motor
Data is changed, par. 1-30
Stator Resistance (Rs)
to
, the advanced motor parame-
ters, will return to default setting.
This parameter cannot be adjusted while the motor
is running.
Full AMA should be run without filter only while re-
duced AMA should be run with filter.
See section:
Application Examples > Automatic Motor Adaptation
in the
Design Guide.
1-71 Start Delay
Range:
Function:
0.0 s*
[0.0 - 120.0 s]
The function selected in par. 1-80
is active in the delay period.
Enter the time delay required before commencing acceleration.
1-73 Flying Start
Option:
Function:
This function makes it possible to catch a motor which is spinning freely due to a mains drop-out.
When par. 1-73
is enabled, par. 1-71
Search direction for flying start is linked to the setting in par. 4-10
Clockwise
[0]: Flying start search in clockwise direction. If not successful, a DC brake is carried
out.
Both Directions
[2]: The flying start will first make a search in the direction determined by the
last reference (direction). If not finding the speed it will make a search in the other direction. If
not successful, a DC brake will be activated in the time set in par. 2-02
DC Braking Time
. Start
will then take place from 0Hz.
[0] *
Disabled
Select
Disable
[0] if this function is not required
[1]
Enabled
Select
Enable
[1] to enable the frequency converter to “catch” and control a spinning motor.
The parameter is always set to [1] Enable when par. 1-10
Motor Construction
= [1] PM non sali-
ent.
Important related parameters:
•
par. 1-58
Flystart Test Pulses Current
•
par. 1-59
Flystart Test Pulses Frequency
Important parameters specifically when par. 1-10
Motor Construction
= [1] PM non salient:
•
par. 2-01
DC Brake Current
•
par. 2-02
DC Braking Time
•
par. 2-03
DC Brake Cut In Speed [RPM]
•
par. 2-04
DC Brake Cut In Speed [Hz]
The Flystart Principle used for PM motors is based on a passive meas-
urement at speeds above 2% of nominal (determined by
par. 1-59
Flystart Test Pulses Frequency
). Below that speed there are
two options:
1.
Either the motor is brought to a halt by using DC Brake (de-
fined in par. 2-01
DC Brake Current
, par. 2-02
DC Braking
Time
, par. 2-03
DC Brake Cut In Speed [RPM]
or par. 2-04
DC
Brake Cut In Speed [Hz]
).
2.
Change the method of speed and direction estimation to an
active scheme based on sending out test pules (defined in
par. 1-58
Flystart Test Pulses Current
and par. 1-59
Flystart
Test Pulses Frequency
).
Current limitations of the Flystart Principle used for PM motors:
•
The speed range is up to 100% Nominal Speed or the field
weakening speed (which ever is lowest).
•
PMSM with high back emf (>300VLL(rms)) and high winding
inductance(>10mH) needed more time for reducing short cir-
cuit current to zero and may be susceptible to error in estima-
tion.
•
Current testing limited to a speed range up to 300Hz. For cer-
tain units the limit is 250Hz; all 200-240V units up to and in-
cluding 2.2kW and all 380-480V units up to and including
4kW.
•
Current testing limited to a machine power size up to 22kW.
•
Prepared for salient pole machine (IPMSM) but not yet verified
on those types of machine.
•
An active measurement function is used to estimate the speed
at very low motor speeds. This function results in good accu-
racy in speed range up to 0-2% of the nominal motor speed.
VLT HVAC Drive High Power Operating In-
structions
6 How to Programme
MG.11.F3.02 - VLT
®
is a registered Danfoss trademark
105
6