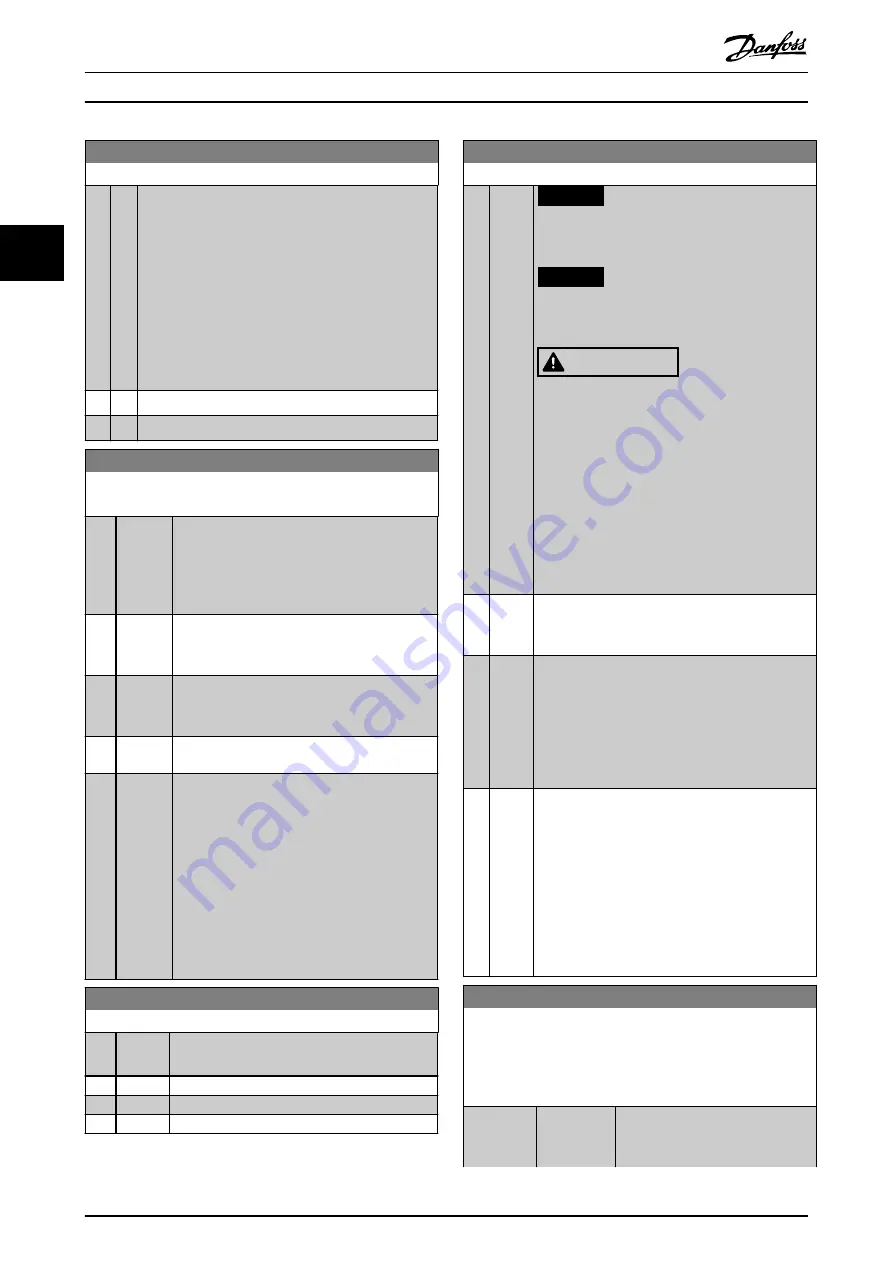
14-51 DC-Link Compensation
Option: Function:
The rectified AC-DC voltage in the frequency converter's
DC link is associated with voltage ripples. These ripples
can increase in magnitude with increased load. These
ripples are undesirable because they can generate
current and torque ripples. A compensation method is
used to reduce these voltage ripples in the DC link. In
general, DC-link compensation is recommended for
most applications, but pay attention when operating in
field weakening as it can generate speed oscillations at
the motor shaft. In field weakening, turn off DC-link
compensation.
[0] Off Disables DC-link compensation.
[1] On Enables DC-link compensation.
14-52 Fan Control
Select minimum speed of the main fan.
Option:
Function:
[0]
*
Auto
Select
[0] Auto
to run fan only when internal
temperature in frequency converter is in range
35
°
C (95
°
F) to approximately 55
°
C (131
°
F).
Fan runs at low speed below 35
°
C (95
°
F), and
at full speed at approximately 55
°
C (131
°
F).
[1]
On 50%
The fan always runs at 50% speed or above. The
fan runs at 50% speed at 35
°
C (95
°
F), and at
full speed at approximately 55
°
C (131
°
F).
[2]
On 75%
The fan always runs at 75% speed or above. The
fan runs at 75% speed at 35
°
C (95
°
F), and at
full speed at approximately 55
°
C (131
°
F).
[3]
On
100%
The fan always runs at 100% speed.
[4]
Auto
(Low
temp
env.)
This option is the same as
[0] Auto
, but with
special considerations around and below 0
°
C
(32
°
F). In option
[0] Auto
there is a risk that the
fan starts running around 0
°
C as the frequency
converter detects a sensor fault and thus
protects the frequency converter while reporting
warning 66, Heat sink Temperature Low
. Option
[4]
Auto (Low temp env.)
can be used in very cold
environments and prevents the negative effects
of this further cooling and avoids
warning 66,
Heat sink Temperature Low
.
14-53 Fan Monitor
Option:
Function:
Select the frequency converter action if a fan
fault is detected.
[0]
Disabled
[1]
*
Warning
[2]
Trip
14-55 Output Filter
Option:
Function:
NOTICE
This parameter cannot be adjusted while the
motor is running.
NOTICE
Reset the frequency converter after selecting
[2] Sine-Wave Filter Fixed
.
CAUTION
OVERHEATING OF FREQUENCY
CONVERTER
When using sine-wave filters, there is a risk
of overheating of the frequency converter,
which can result in personal injury and
equipment damage.
Always set
to
[2] Sine-wave fixed
when using a sine-wave
filter.
Select the type of output filter connected.
[0]
*
No
Filter
This is the default setting and should be used with
dU/dt filters or high frequency common mode (HF-
CM) filters.
[1] Sine-
Wave
Filter
This setting is only for backwards compatibility. It
enables operation with flux control principle when
parameter 14-56 Capacitance Output Filter
and
parameter 14-57 Inductance Output Filter
are
programmed with the output filter capacitance and
inductance. It does not limit the range of the
switching frequency.
[2] Sine-
Wave
Filter
Fixed
This parameter sets a minimum allowed limit to the
switching frequency and ensures that the filter is
operated within the safe range of switching
frequencies. Operation is possible with all control
principles. For flux control principle, program
parameter 14-56 Capacitance Output Filter
and
parameter 14-57 Inductance Output Filter
(these
parameters have no effect in VVC
+
and U/f). The
modulation pattern is set to SFAVM, which gives the
lowest acoustic noise in the filter.
14-56 Capacitance Output Filter
Compensation function of the LC filter requires the per phase
equivalent star-connected capacitance of the filter (3 times the
capacity between 2 phases when capacitance is delta
connection).
Range:
Function:
Size related
*
[0.1 - 6500
uF]
Set the capacitance of the output
filter. The value can be found on the
filter label.
Parameter Descriptions
VLT
®
AutomationDrive FC 301/302
198
Danfoss A/S © 10/2018 All rights reserved.
MG33MP02
3
3
Содержание VLT AutomationDrive FC 302
Страница 2: ......