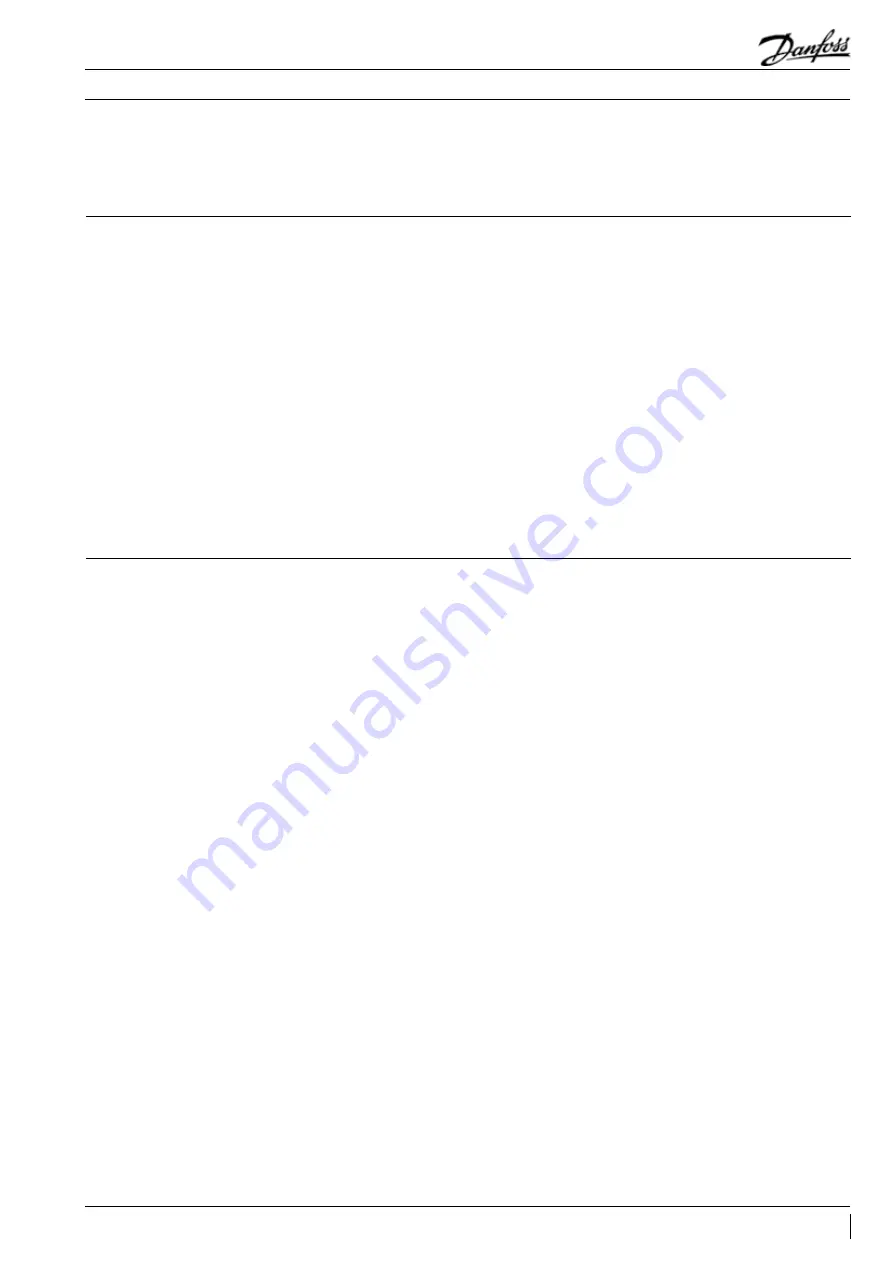
Specific application recommendations
Low load operations
The compressor should be run for a minimum
period to ensure that the oil has sufficient time
to properly return to the compressor sump and
that the motor receives enough cooling under
conditions of lowest refrigerant mass flow.
Brazed plate
heat exchangers
A brazed plate heat exchanger needs very
little internal volume to satisfy the heat
transfer requirements. Consequently, the heat
exchanger offers very little internal volume for
the compressor to draw vapour from the suction
side. The compressor can then quickly enter into
a vacuum condition. It is therefore important
that the expansion device be sized correctly
and that a sufficient pressure differential across
the expansion device be available to ensure
adequate refrigerant feed into the evaporator.
This aspect is of special concern when operating
the unit under low ambient and load conditions.
For further information on these conditions,
please refer to the previous sections.
Due to the small volume of the brazed plate heat
exchanger, no pump-down cycle is normally
required. The suction line running from the heat
exchanger to the compressor must be trapped to
avoid refrigerant migration to the compressor.
When using a brazed plate condenser heat
exchanger, a sufficient free volume for the
discharge gas to accumulate is required in order
to avoid excess pressure build-up. At least 1
meter of discharge line is necessary to generate
this volume. To help reduce the discharge gas
volume immediately after start-up, the supply
of cooling water to the heat exchanger may be
opened before the compressor starts, to remove
superheat and condense the incoming discharge
gas more quickly.
Water utilising systems
Apart from residual moisture in the system
after commissioning, water could also enter the
refrigeration circuit during operation. Water in
the system shall always be avoided. Not only
because it can shortly lead to electrical failure,
sludge in sump and corrosion but in particular
because it can cause serious safety risks.
Common causes for water leaks are corrosion and
freezing.
Corrosion: Materials in the system shall be
compliant with water and protected against
corrosion.
Freezing: When water freezes into ice its volume
expands which can damage heat exchanger
walls and cause leaks. During off periods water
inside heat exchangers could start freezing when
ambient temperature is lower than 0°C. During
on periods ice banking could occur when the
circuit is running continuously at too low load.
Both situations should be avoided by connecting
a pressure and thermostat switch in the safety
line.
39
FRCC.PC.015.A8.02
Application Guidelines