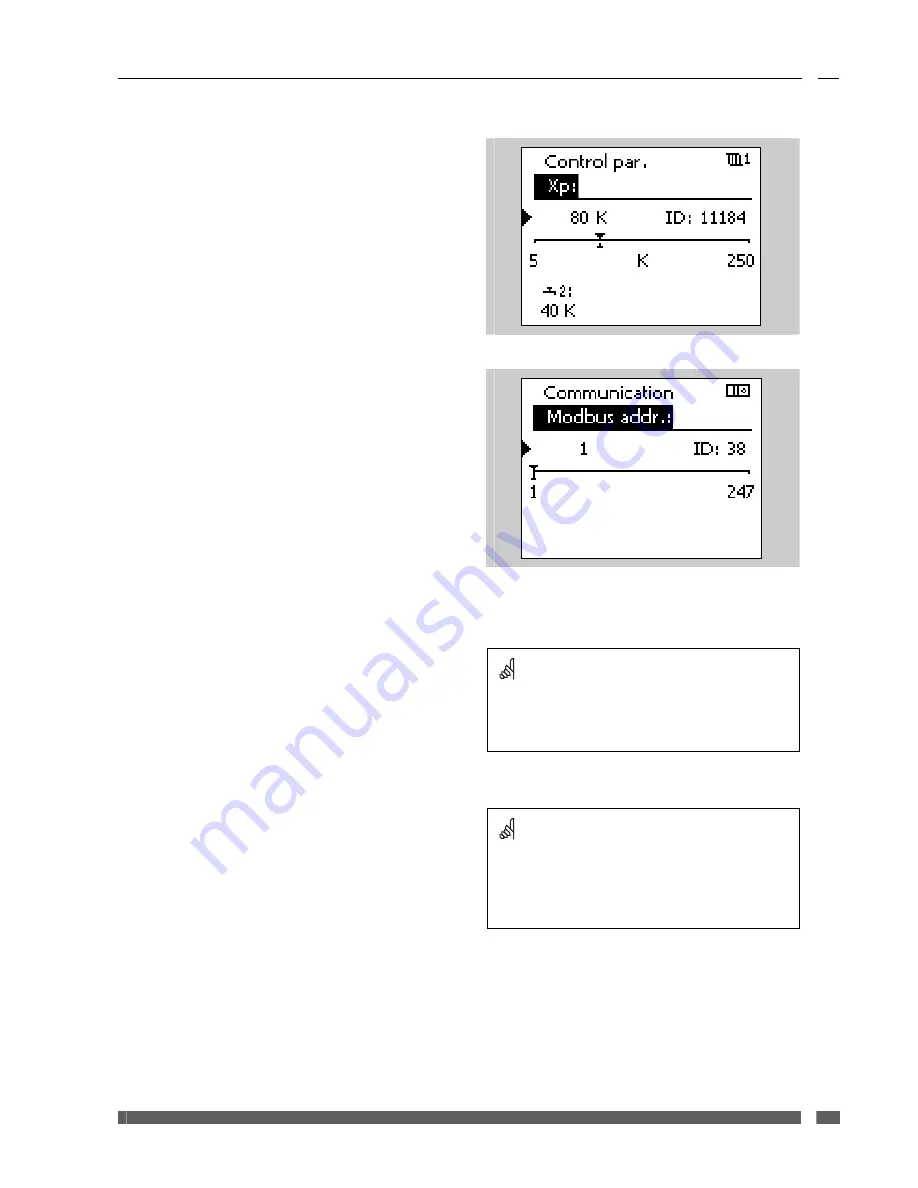
Instructions
ECL Comfort 210 / 310, communication description
6.
ECL 210/310 Modbus description
This section describes the overall ECL 210/310 Modbus
communication interface.
Parameter naming
The parameters are overall divided into two functional sections,
the application – and system parameters.
Application parameters depend on the used application, e.g.
“A266.1”, and include parameters such as temperature set-points,
schedules and control properties etc. The parameters are as rule of
thumb located in the address range 11000 – 13999. The 1000
th
decimal indicates the ECL Comfort circuit number, i.e. 11xxx is
circuit 1, 12xxx is circuit 2, 13xxx is circuit 3. The number of
applicable circuits depends on the Application, e.g. “A266.1” has 2
circuits (1 heating circuit and 1 DHW circuit).
System parameters include parameters such as system
information, raw values, communication settings, output override,
input configuration and time & date.
Some of the Parameter NUmbers (PNU’s) can be seen directly in
the ECL display – the ID number.
The application parameters are named (numbered) in accordance
with their name in the ECL Comfort.
A partial list of parameters can be found in the appendix.
Figure 6-1: Display parameter number examples
6.1
Modbus address
The valid Modbus address range is 1 – 247. The default Modbus
address is 1.
Address 254 is used as service address and may only be used when
one ECL is connected, e.g. USB service port or Modbus/TCP.
The Modbus address can be changed by writing to PNU 38.
Modbus address changes take effect immediately.
It is recommended only to change the Modbus address
directly at the ECL or via the Modbus USB interface.
6.2
RS-485 Baud rate
The baud rate for the RS-485 bus can be changed by writing 9 (for
baud rate 9600), 19 (for baud rate 19200) or 38 (for baud rate
38400, this is default) to PNU 39 via Modbus. Attempts to write any
other values are rejected.
All devices on a network must have the same baud rate.
The ECL menu for changing the baud rate was not included until
ECL software version 1.30 so for previous versions it could only be
changed through communication.
Baud rate changes take effect immediately.
Care must be taken if the baud rate is changed via the
Modbus interface because the communication connection
will be lost due to the change.
Danfoss District Energy
VI.LG.V3.02
DEN-SMT/DK
11