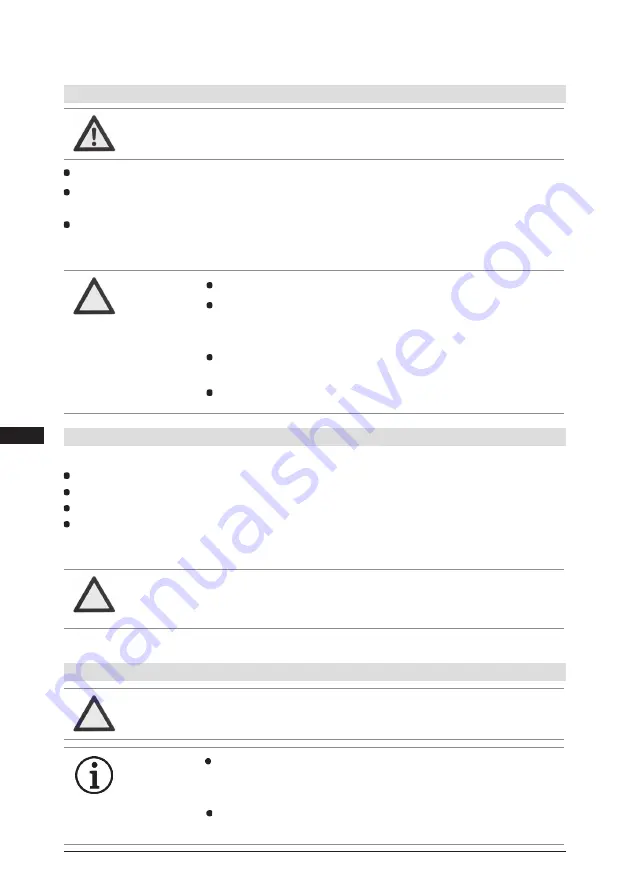
D
GB
CN
E
I
TR
CN
14 | AQ450736920607en-000201
© Danfoss | Climate Solutions | 2023.07
5
|
Commissioning
Make sure that the suction and discharge line valves are open.
With the compressor switched off, add the liquid refrigerant directly to the condenser or receiver,
breaking the vacuum.
If the refrigerant needs topping up after starting the compressor, it can be topped up in vapour
form on the suction side, or, taking suitable precautions, also in liquid form at the inlet to the
evaporator.
After starting, check the compressor's oil level.
Drive motor in operating condition "High idle".
Compressor run time min. 10 minutes.
The system should have reached operating points.
Check oil level. As the installation location of the compressor can differ in practice (inclinations), it
is recommended that the oil level is checked in both sight glasses. The oil level must be visible in
at least one sight glass.
5.5 Refrigerant charge
5.6 Oil level check
5.7 Shaft seal
CAUTION
Wear personal protective clothing such as goggles and protective
gloves!
ATTENTION
Avoid overfilling the system with refrigerant!
To avoid shifts in concentration, zeotropic refrigerant blends
(e.g. R407C) must always be added to the refrigerating plant in
liquid form.
Do not pour liquid refrigerant through the suction line valve on the
compressor.
It is not permissible to mix additives with the oil and refrigerant.
ATTENTION After a compressor is replaced, the oil level must be checked again.
If the level is too high, oil must be drained off (risk of oil impact,
reduced performance of the air-conditioning system).
ATTENTION
Failure to observe the following instructions can cause loss of
refrigerant and damage to the shaft seal!
INFO
The shaft seal seals and lubricates with oil. An oil leakage of
0.05 ml per operating hour is therefore normal. This applies
particularly during the run-in phase (200 - 300 h).
To trap and collect leaked oil, the FK40 is fitted with an inte
-
grated leak oil trapping device with oil reservoir (P.6, Fig. 1).