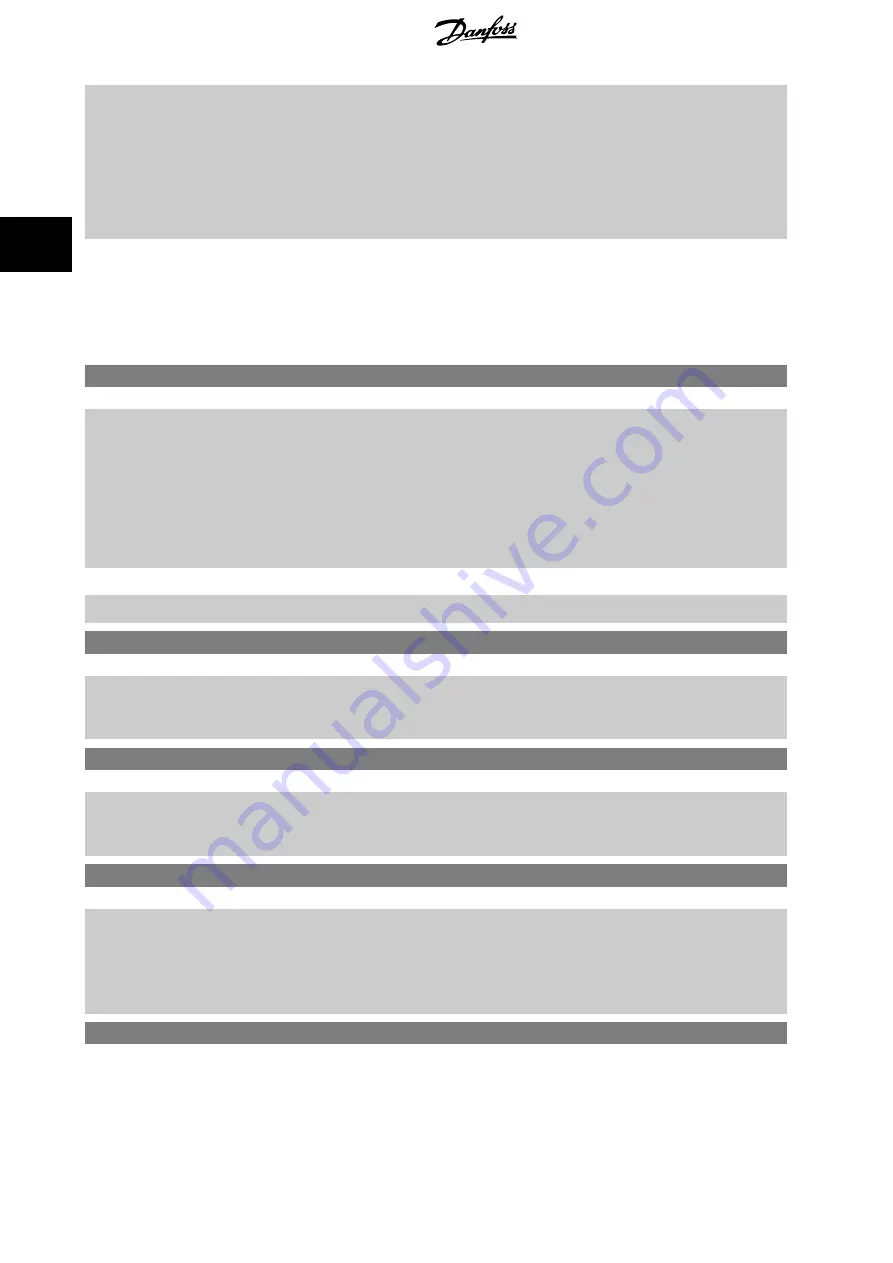
[3]
Start speed cw
Only possible with VVC+.
Connect the function described in par. 1-74
Start Speed (RPM)
and par. 1-76
Start Current
in the
start delay time.
Regardless of the value applied by the reference signal, the output speed applies the setting of the
start speed in par. 1-74 or par. 1-75 and the output current corresponds to the setting of the start
current in par. 1-76
Start Current
. This function is typically used in hoisting applications without
counterweight and especially in applications with a Cone-motor, where the start is clockwise, fol-
lowed by rotation in the reference direction.
[5]
VVC+/Flux clockwise
for the function described in par. 1-74 only (
Start speed in the start delay time
). The start current
is calculated automatically. This function uses the start speed in the start delay time only. Regardless
of the value set by the reference signal, the output speed equals the setting of the start speed in
par. 1-74.
Start speed/current clockwise
[3] and
VVCplus/Flux clockwise
[5] are typically used in
hoisting applications.
Start speed/current in reference direction
[4] is particularly used in applica-
tions with counterweight and horizontal movement.
1-73 Flying Start
Option:
Function:
This function makes it possible to catch a motor which is spinning freely due to a mains drop-out.
When par.1-73
is enabled, par. 1-71
Start Delay
has no function.
Search direction for flying start is linked to the setting in par.4-10
.
Clockwise
[0]: Flying start search in clockwise direction. If not successful, a DC brake is carried out.
Both Directions
[2]: The flying start will first make a search in the direction determined by the last
reference (direction). If not finding the speed it will make a search in the other direction. If not
successful, a DC brake will be activated in the time set in par.2-02
. Start will then
take place from 0 Hz.
[0] *
Disabled
Select
Disable
[0] if this function is not required
[1]
Enabled
Select
Enable
[1] to enable the frequency converter to “catch” and control a spinning motor.
1-74 Start Speed [RPM]
Range:
Function:
0 RPM*
[0 - 600 RPM]
Set a motor start speed. After the start signal, the output speed leaps to set value. Set the start
function in par. 1-72
Start Function
to [3], [4] or [5], and set a start delay time in par. 1-71
Start
Delay
.
1-75 Start Speed [Hz]
Range:
Function:
0 Hz*
[0.0 - 500.0 Hz]
Set a motor start speed. After the start signal, the output speed leaps to set value. Set the start
function in par. 1-72
Start Function
to [3], [4] or [5], and set a start delay time in par. 1-71
Start
Delay
.
1-76 Start Current
Range:
Function:
0.00 A*
[0.00 - par. 1-24 A]
Some motors, e.g. cone rotor motors, need extra current/starting speed to disengage the rotor. To
obtain this boost, set the required current in par.1-76
. Set par. 1-72
Start Function
to [3] or [4], and set a start delay time in par. 1-71
Start
Delay
.
This parameter can be used for hoist applications (cone rotor).
1-77 Compressor Start Max Speed [rpm]
Range:
Function:
0 rpm*
[0.0 - max output speed]
The parameter enables “High Starting Torque”. This is a function, where the Current Limit and
Torque Limit are ignored during start of the motor. The time, from the start signal is given until the
3 Parameter Description
ADAP-KOOL
®
Drive Programming Guide
52
MG.11.N1.02 - VLT
®
is a registered Danfoss trademark
3
Содержание ADAP-KOOL Drive
Страница 14: ...2 How to Programme ADAP KOOL Drive Programming Guide 14 MG 11 N1 02 VLT is a registered Danfoss trademark 2...
Страница 201: ...ADAP KOOL Drive Programming Guide 3 Parameter Description MG 11 N1 02 VLT is a registered Danfoss trademark 201 3...
Страница 222: ...4 Parameter Lists ADAP KOOL Drive Programming Guide 222 MG 11 N1 02 VLT is a registered Danfoss trademark 4...