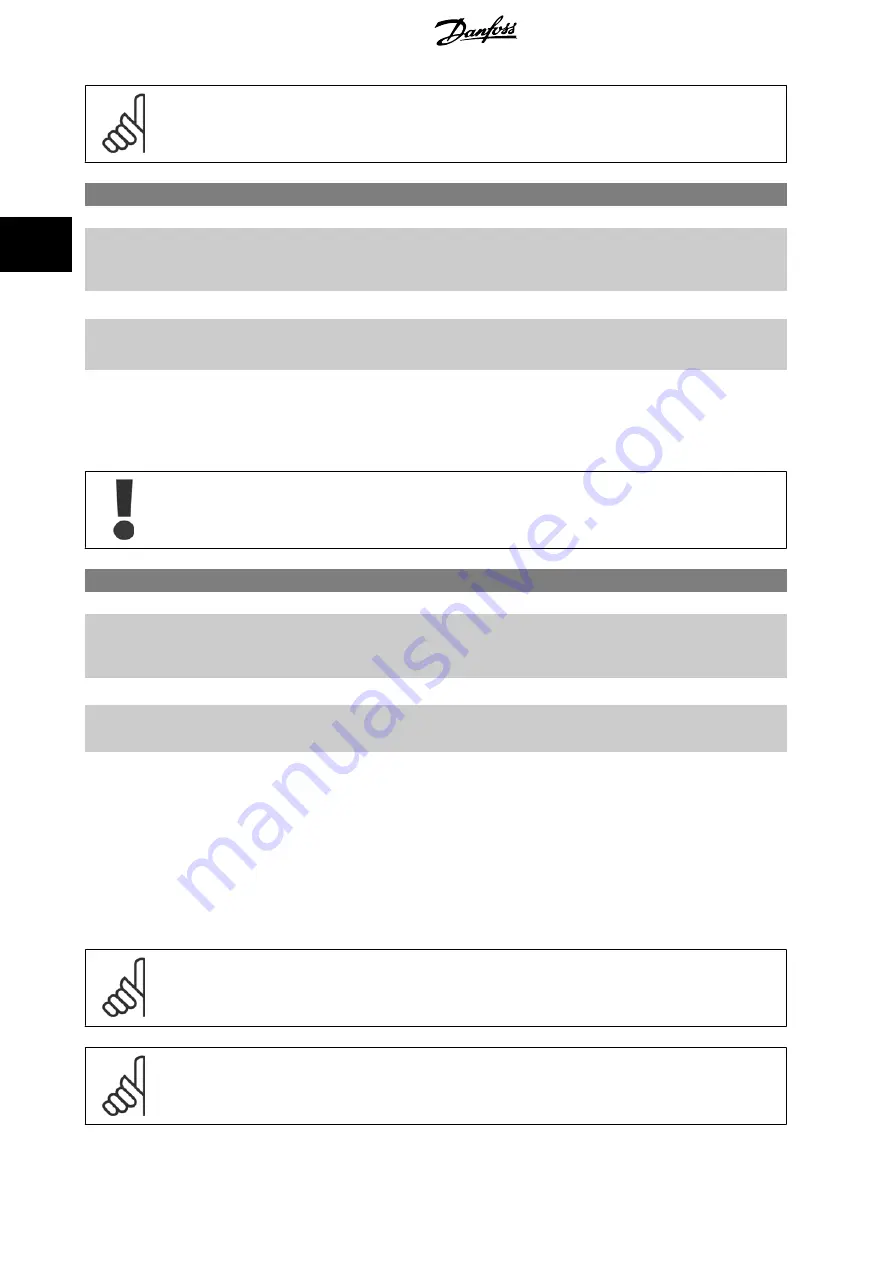
NB!
This parameter cannot be changed while the motor is running.
1-28 Motor Rotation Check
Option:
Function:
Following installation and connection of the motor, this function allows the correct motor rotation
direction to be verified. Enabling this function overrides any bus commands or digital inputs, except
External Interlock and Safe Stop (if included).
[0] *
Off
Motor Rotation Check is not active.
[1]
Enabled
Motor Rotation Check is enabled. Once enabled, Display shows:
“Note! Motor may run in wrong direction”.
Pressing [OK], [Back] or [Cancel] will dismiss the message and display a new message: “Press [Hand on] to start the motor. Press [Cancel] to abort”.
Pressing [Hand on] starts the motor at 5 Hz in forward direction and the display shows: “Motor is running. Check if motor rotation direction is correct.
Press [Off] to stop the motor”. Pressing [Off] stops the motor and resets par.1-28
. If motor rotation direction is incorrect, two
motor phase cables should be interchanged. IMPORTANT:
Mains power must be removed before disconnecting motor phase cables.
1-29 Automatic Motor Adaptation (AMA)
Option:
Function:
The AMA function optimizes dynamic motor performance by automatically optimizing the advanced
motor parameters par.1-30
) while the motor
is stationary.
[0] *
Off
No function
[1]
Enable complete AMA
performs AMA of the stator resistance R
S
, the rotor resistance R
r
, the stator leakage reactance X
1
,
the rotor leakage reactance X
2
and the main reactance X
h
.
[2]
Enable reduced AMA
performs a reduced AMA of the stator resistance R
s
in the system only. Select this option if an LC
filter is used between the frequency converter and the motor.
Activate the AMA function by pressing [Hand on] after selecting [1] or [2]. See also the section
Automatic Motor Adaptation
. After a normal sequence,
the display will read: “Press [OK] to finish AMA”. After pressing the [OK] key the frequency converter is ready for operation.
Note:
•
For the best adaptation of the frequency converter, run AMA on a cold motor
•
AMA cannot be performed while the motor is running
NB!
It is important to set motor par. 1-2* Motor Data correctly, since these form part of the AMA algorithm. An AMA must be performed
to achieve optimum dynamic motor performance. It may take up to 10 min., depending on motor power rating.
NB!
Avoid generating external torque during AMA
3 Parameter Description
ADAP-KOOL
®
Drive Programming Guide
48
MG.11.N1.02 - VLT
®
is a registered Danfoss trademark
3
Содержание ADAP-KOOL Drive
Страница 14: ...2 How to Programme ADAP KOOL Drive Programming Guide 14 MG 11 N1 02 VLT is a registered Danfoss trademark 2...
Страница 201: ...ADAP KOOL Drive Programming Guide 3 Parameter Description MG 11 N1 02 VLT is a registered Danfoss trademark 201 3...
Страница 222: ...4 Parameter Lists ADAP KOOL Drive Programming Guide 222 MG 11 N1 02 VLT is a registered Danfoss trademark 4...