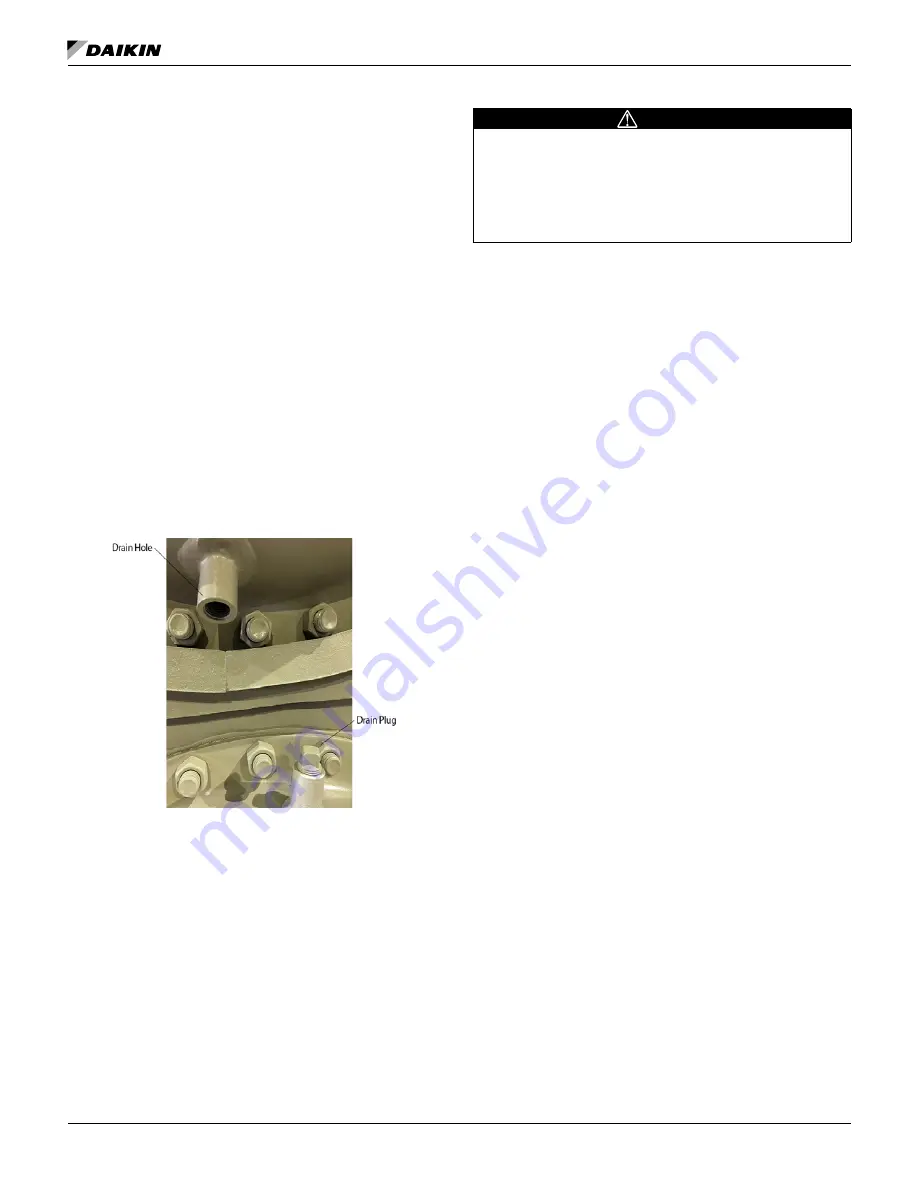
IOM 1266-2 • MAGNITUDE
®
MODEL WME CHILLERS
18 www.DaikinApplied.com
I
nsTallaTIon
• water pressure gauge connection taps and gauges at the
inlet and outlet connections of both vessels for measuring
water pressure drop.
NOTE:
This product, in its standard configuration, is
equipped with a shell and tube evaporator with
carbon steel shell and copper tubes. The water or
other fluid used in contact with the wetted surfaces of
the heat exchangers must be clean and non-corrosive
to the standard materials of construction. Daikin
Applied makes no warranty as to the compatibility
of fluids and materials. Non-compatible fluids may
void the equipment warranty. If the compatibility of
the fluid with the standard materials of construction
is in question, a professional corrosion consultant
should administer the proper testing and evaluate
compatibility.
Vessel Drains at Startup
The unit is drained of water at the factory. Units are shipped
with the drain plug in the top water box drain hole and no plug
in the bottom drain hole. Drain plugs for each vessel head
are shipped separately in the control box. Be sure to install
the bottom drain plugs prior to filling the vessel with fluid. See
Figure 16: Drain Plug Installation
Water Quality Guidelines
The water quality provided by the owner/occupant/operator/
user to a chiller system should minimize corrosion, scale
buildup, erosion, and biological growth for optimum efficiency
of HVAC equipment without creating a hazard to operating
personnel or the environment. Strainers must be used to
protect the chiller systems from water-borne debris. Daikin will
not be responsible for any water-borne debris damage or water
side damage to the chiller heat exchangers due to improperly
treated water.
Water systems should be cleaned and flushed prior to chiller
installation. Water testing and treatment should be verified
during initial chiller installation/commissioning and maintained
on a continuous basis by water treatment professionals (see
Limited Product Warranty).
WARNING
The improper use of detergents, chemicals, and additives
in the chiller system water may adversely affect chiller
performance and potentially lead to repair costs not covered
by warranty. Any decision to use these products is at the
discretion of the owner/occupant/operator/user and as such
they assume full liability/responsibility for any damage that
may occur due to their use.
Variable Fluid Flow Rates
Both excessively high and low fluid flow rates should be
avoided. Extremely high fluid flow rates and high tube
velocities will result in high fluid pressure drops, high pumping
power, and potential tube erosion or corrosion damage.
Extremely low fluid flow rates and low velocities should also
be avoided as they will result in poor heat transfer, high
compressor power, sedimentation and tube fouling.
If it is decided to vary the evaporator or condenser water flow
rate, the flow rate should not exceed the minimum or maximum
limits. Additionally, the rate of change for the evaporator flow
rate should not exceed 50% of the current value per minute.
Water Volume
All chilled water systems need adequate time to recognize a
load change to avoid short cycling of the compressors or loss
of control. The potential for short cycling usually exists when
the building load falls below the minimum chiller plant capacity
or on close-coupled systems with very small water volumes.
Assuming that there are no sudden load changes and that
the chiller plant has reasonable turndown, a rule of thumb
of “gallons of water volume equal to two to three times the
chilled water gpm flow rate” is often used. For a more accurate
determination of minimum system volume, consult Chiller Plant
Design Application Guide, AG 31-003.
A properly designed storage tank should be added if the
system components do not provide sufficient water volume.
Water Temperature Guidelines
The maximum temperature of water entering the chiller
evaporator on standby must not exceed 115°F (46.1°C).
Maximum temperature entering the evaporator on startup must
not exceed 90°F (32°C).
Reducing Condenser Entering Water
Temperature
Magnitude
®
WME chillers can start and run with entering
condenser water temperatures as low as 40°F (4.4°C). The
WME chillers can also start and maintain operation with
inverted conditions, meaning the entering condenser water
temperature can be lower than the leaving chilled water
temperature. Contact your local Daikin Applied sales office
if your application requires a condenser entering water
temperature lower than 40°F (4.4°C).
Содержание Magnitude WME Series
Страница 4: ...Intentionally Left Blank...