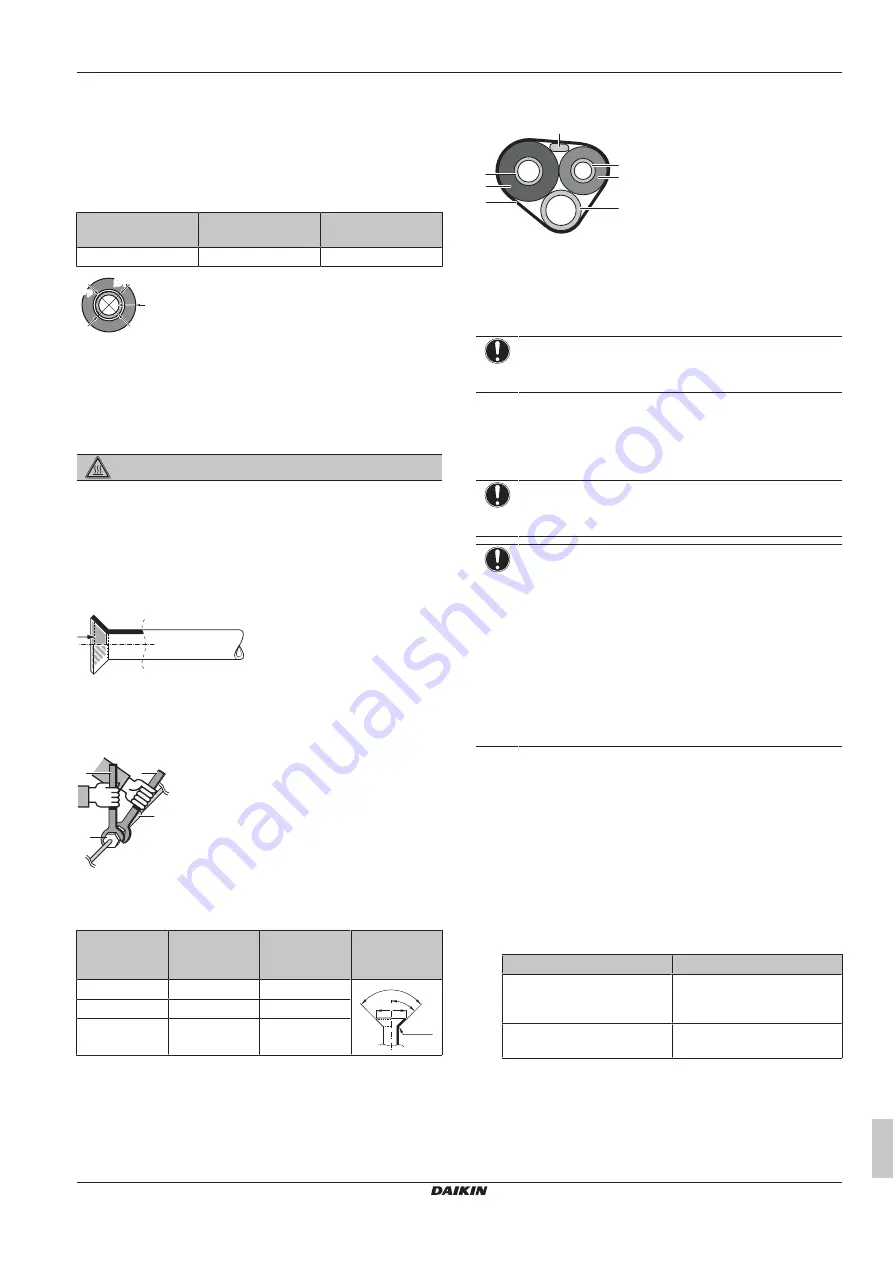
6 Piping installation
Installation manual
11
FTXP20~3 ATXP20~35N5V1B
Daikin room air conditioner
3P650253-9H – 2022.10
6.1.2
Refrigerant piping insulation
▪ Use polyethylene foam as insulation material:
▪ with a heat transfer rate between 0.041 and 0.052 W/mK (0.035
and 0.045 kcal/mh°C)
▪ with a heat resistance of at least 120°C
▪ Insulation thickness
Pipe outer diameter
(Ø
p
)
Insulation inner
diameter (Ø
i
)
Insulation thickness
(t)
6.4 mm (1/4")
8~10 mm
≥10 mm
Ø
i
Ø
i
t
Ø
p
Ø
p
If the temperature is higher than 30°C and the humidity is higher
than RH 80%, the thickness of the insulation materials should be at
least 20 mm to prevent condensation on the surface of the
insulation.
6.2
Connecting the refrigerant piping
DANGER: RISK OF BURNING/SCALDING
6.2.1
Guidelines when connecting the
refrigerant piping
Take the following guidelines into account when connecting pipes:
▪ Coat the flare inner surface with ether oil or ester oil when
connecting a flare nut. Tighten 3 or 4 turns by hand, before
tightening firmly.
▪ ALWAYS use 2 wrenches together when loosening a flare nut.
▪ ALWAYS use a spanner and torque wrench together to tighten the
flare nut when connecting the piping. This to prevent nut cracking
and leaks.
a
b
c
d
a
Torque wrench
b
Spanner
c
Piping union
d
Flare nut
Piping size
(mm)
Tightening
torque (N•m)
Flare
dimensions (A)
(mm)
Flare shape
(mm)
Ø6.4
15~17
8.7~9.1
R=
0.4~0.8
±2
45°
90°
±2
ØA
Ø9.5
33~39
12.8~13.2
Ø12.7
50~60
16.2~16.6
6.2.2
To connect the refrigerant piping to the
indoor unit
▪
Pipe length
. Keep refrigerant piping as short as possible.
1
Connect refrigerant piping to the unit using
flare connections
.
2
Insulate
the refrigerant piping, interconnection cable and drain
hose on the indoor unit as follows:
c
a
b
f
d
g
e
a
Gas pipe
b
Gas pipe insulation
c
Interconnection cable
d
Liquid pipe
e
Liquid pipe insulation
f
Finishing tape
g
Drain hose
NOTICE
Make sure to insulate all refrigerant piping. Any exposed
piping might cause condensation.
6.3
Checking the refrigerant piping
6.3.1
To check for leaks
NOTICE
Do NOT exceed the unit's maximum working pressure (see
"PS High" on the unit name plate).
NOTICE
ALWAYS use a recommended bubble test solution from
your wholesaler.
NEVER use soap water:
▪ Soap water may cause cracking of components, such
as flare nuts or stop valve caps.
▪ Soap water may contain salt, which absorbs moisture
that will freeze when the piping gets cold.
▪ Soap water contains ammonia which may lead to
corrosion of flared joints (between the brass flare nut
and the copper flare).
1
Charge the system with nitrogen gas up to a gauge pressure of
at least 200 kPa (2 bar). It is recommended to pressurize to
3000 kPa (30 bar) in order to detect small leaks.
2
Check for leaks by applying the bubble test solution to all
connections.
3
Discharge all nitrogen gas.
6.3.2
To perform vacuum drying
1
Vacuum the system until the pressure on the manifold indicates
−0.1 MPa (−1 bar).
2
Leave as is for 4-5 minutes and check the pressure:
If the pressure…
Then…
Does not change
There is no moisture in the
system. This procedure is
finished.
Increases
There is moisture in the
system. Go to the next step.
3
Vacuum the system for at least 2 hours to a manifold pressure
of −0.1 MPa (−1 bar).
4
After turning the pump OFF, check the pressure for at least
1 hour.
5
If you do NOT reach the target vacuum or CANNOT maintain
the vacuum for 1 hour, do the following: