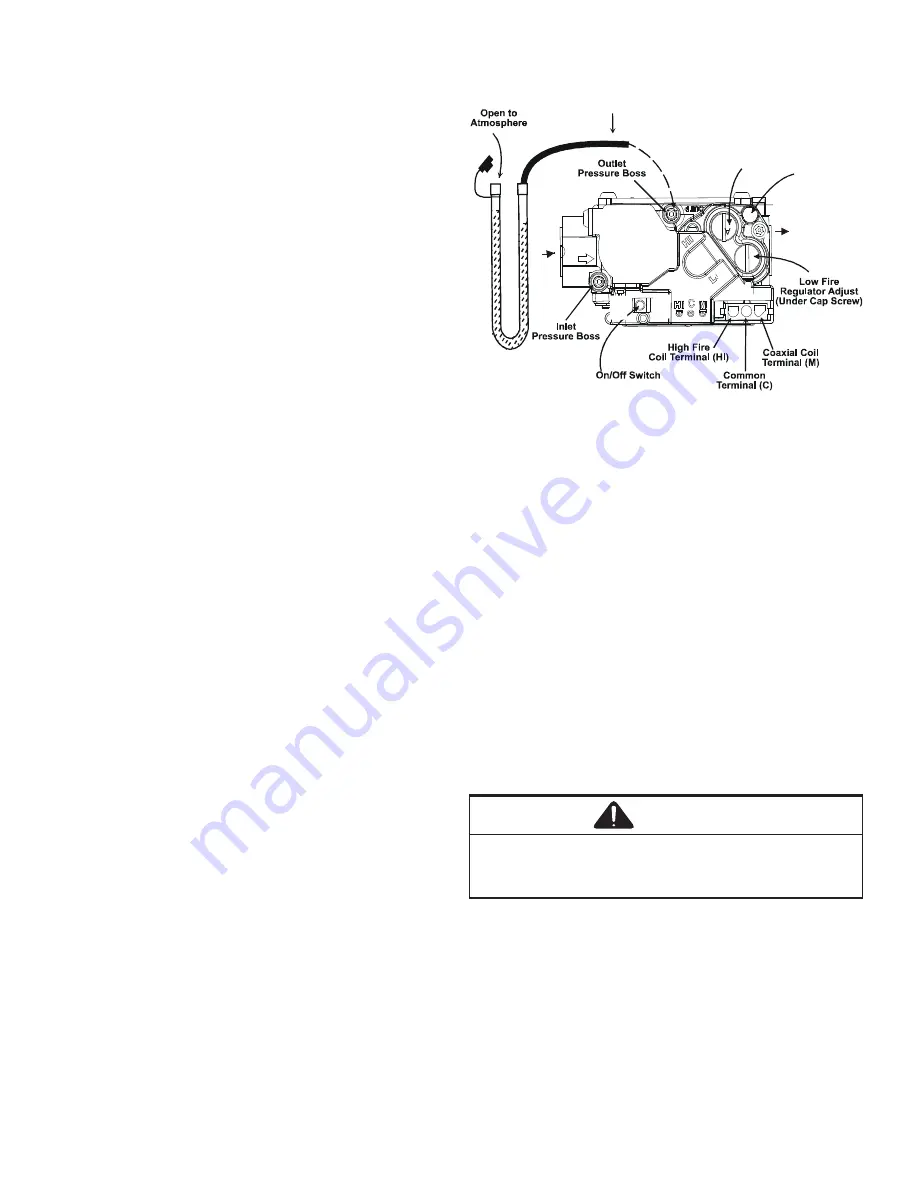
39
SYSTEM OPERATION
Gas Input (Natural Gas Only) Check
It is the responsibility of the contractor to adjust the gas
input to the unit.
To measure the gas input use a gas meter and proceed as
follows:
1. Turn off gas supply to all other appliances except the
unit.
2. With the unit operating, time the smallest dial on the
meter for one complete revolution. If this is a 2 cubic
foot dial, divide the seconds by 2; if it is a 1 cubic foot
dial, use the seconds as is. This gives the seconds per
cubic foot of gas being delivered to the unit.
3. INPUT=GAS HTG VALUE x 3600 / SEC. PER CUBIC FOOT
Example:
Natural gas with a heating value of 1000 BTU per
cubic foot and 34 seconds per cubic foot as determined by
Step 2, then:
Input = 1000 x 3600 / 34 = 106,000 BTU per Hour.
NOTE: BTU content of the gas should be obtained from
the gas supplier. This measured input must not be greater
than shown on the unit rating plate.
Adjust input rate by varying the adjustment of the gas
pressure regulator on the gas valve. All adjustments
must be made with furnace operating at high fire and at
normal operating temperature. A manometer should be
connected to the gas valve to verify pressure is within
the specified range (see following figures for manometer
connections). Clockwise rotation of the pressure regulator
screw increases pressure and gas flow rate. Turn screw
counterclockwise to decrease pressure and gas flow rate.
After adjustment the furnace temperature rise must be
within the range specified on the unit data plate.
NOTE: Thermal efficiency of the furnace is a product
efficiency rating determined under continuous operating
conditions independent of any installed system.
Manometer
Manometer
Hose
High Fire Regulator
Adjust
(Under Cap Screw) Regulator
Vent
Gas Flow
O
N
O
FF
white-rodgers (2-Stage) gas control valve connected
to manometer pressure adjustments
To connect manometer to gas valve:
1. Back outlet pressure tap screw (inside inlet pressure
boss) out one turn (counterclockwise, not more than
one turn).
2. Attach a hose and manometer to the outlet pressure
boss of the valve.
To remove manometer from gas valve:
1. Remove manometer hose from outlet pressure boss.
2. Turn outlet pressure tap screw in to seal pressure port
(clockwise, 7 in-lb. minimum).
3. Turn on electrical power and gas supply to the system.
4. Turn on system power and energize valve.
5. Using a leak detection solution or soap suds, check
for leaks at pressure boss screw. Bubbles forming
indicate a leak. SHUT OFF GAS AND FIX ALL LEAKS
IMMEDIATELY.
CAUTION
To prevent unreliable operation or equipment damage,
the gas manifold pressure must be as specified on the
unit rating plate. Only minor adjustments should be
made by adjusting the gas valve pressure regulator.
6. Relight all other appliances turned off in step 1 of gas
input check. Be sure all pilot burners are operating.
Main Burner Flame Check
Flames should be stable, soft and blue (dust may cause
orange tips but they must not be yellow) and extending
directly outward from the burner without curling, floating
or lifting off.
Содержание DRG0361DH00001S
Страница 20: ...20 SYSTEM OPERATION ...