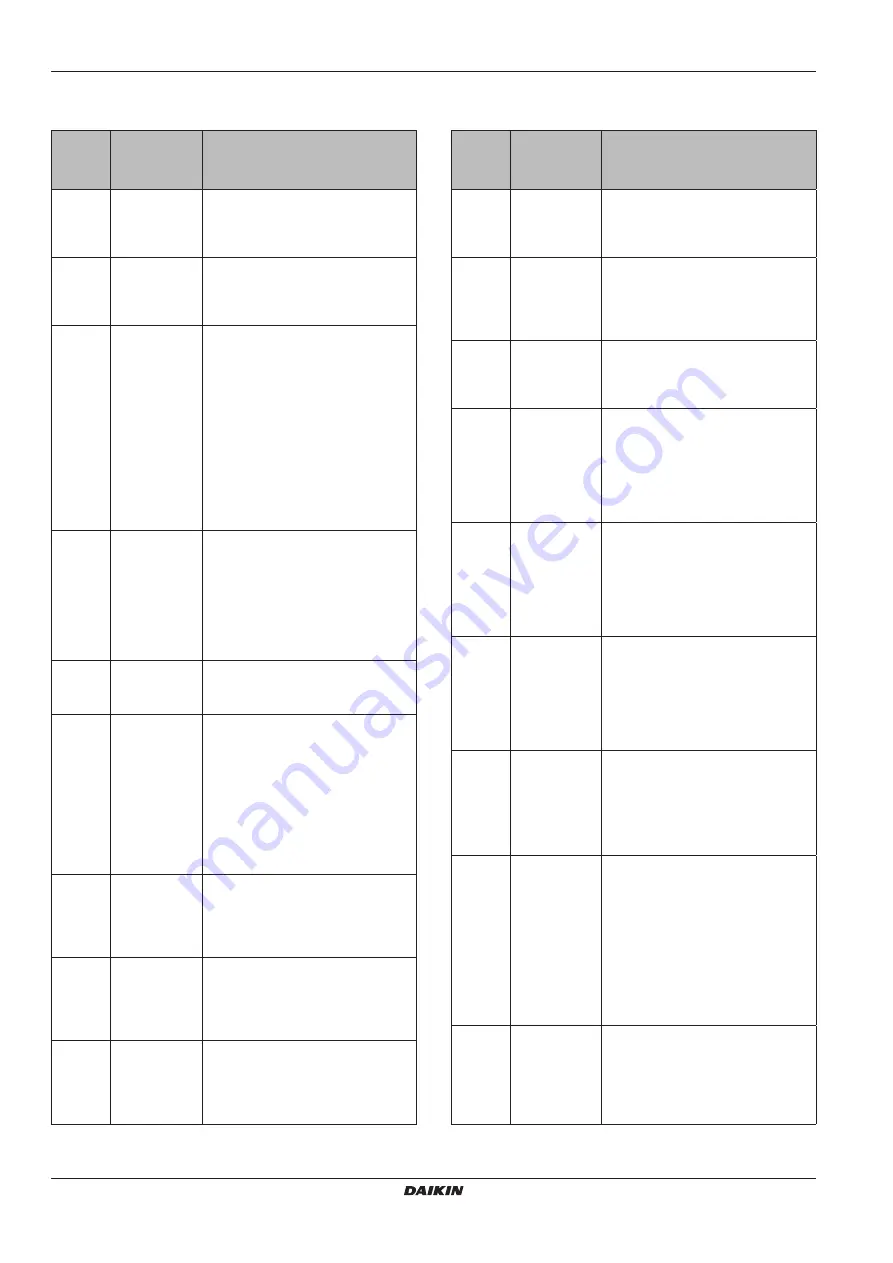
D2CND0 D2CND0 D2CND0
D2CND0 D2TND0 D2TND035A4AA
Wall-mounted condensing boiler
ESIE17 - 09 / 2017.11
Servicing manual
40
10 TROUBLESHOOTING
10 Troubleshooting
ER-
ROR
CODE
REASON
ELIMINATION
10-64
Gas valve
circuit error
Interrupt the power. Check electri
-
cal leads of the gas valve and the
gas valve. Replace the defective
part.
10-65
Gas valve
current error
Interrupt the power. Check electri
-
cal leads of the gas valve and the
gas valve. Replace the defective
part.
11-64
Ignition does
not take
place
Blockage error, restart is not
needed. After third trial, error turns
to lockout, in that case reset is
needed. Check the inlet gas pres
-
sure. Make sure main gas valve is
opened.Check the ignition elec
-
trode and the ionization electrode.
Check ignition transformer. Check
the gas valve. Check the wire har
-
ness. Replace the defective part,
if there are any. Also, check if the
condensate trap is blocked. Check
if the flue duct is installed correctly.
11-65
Flame stabili-
zation fault
Blockage error, restart is not need
-
ed. Check the inlet gas pressure.
Check the ignition electrode and
the ionization electrode. Check
ignition transformer. Check the gas
valve. Check the wire harness.
Replace the defective part, if there
are any.
11-66
Flame signal
loss in safety
time
Also, check if the condensate trap
is blocked. Check if the flue duct is
installed correctly.
11-67
Flame loss
during oper
-
ation
Blockage error, restart is not need
-
ed. Check the ionization electrode.
Check the gas valve. Check the
wire harness. Replace the defective
part, if there are any. Also, check
if the condensate trap is blocked.
Check if the flue duct is installed
correctly. If problem continues,
activate calibration as described in
this manual.
12-64
Ion control
deviation is
too big
Blockage error, restart is not need
-
ed. Check the ionization electrode.
Check the gas valve. Check the
wire harness. Replace the defec
-
tive part, if there are any.
12-65
Ignition
SCOT ac
-
tuators fault
does not take
place
Also, check if the condensate trap
is blocked. Check if the flue duct
is installed correctly. If problem
continues, activate calibration as
described in this manual.
12-66
Ion base val-
ue exceeds
lower factory
limit
Reset the boiler Make a manuel
calibration.Check the ionization
elecktrode, it’s cable connection
and it’s earth cable.Replace, if
defective.
ER-
ROR
CODE
REASON
ELIMINATION
12-67
Ion base val-
ue exceeds
upper factory
limit
Reset the boiler Make a manuel
calibration. Check the fan and
it’s cable connection ,replace if
defective.
12-68
Ion base
value differs
excessively
from previous
value
Check the fan’s suction side.Check
the gas valve and it’s cable connec
-
tion, replace if defective.
12-69
Offset adap
-
tion at limit
Reset the boiler Make a manu
-
el calibration. İncrease the C5
parameter value.İf problem repeats
replace the PCB.
12-70
Offset
adaption not
executable
This is a warning error. Boiler con-
tinues operation but waits the next
adaptation. If the location is windy
and this error repeats, increase the
parameter “Adjustment minimum
capacity (C04)”. Increment can be
2% at each trial.
13-64
Fan speed
error
Reset the boiler, if needed. Check
the silencer-fan connection and be
sure that fan suction is not blocked.
Check fan and it’s cable connec
-
tions for interruptions and shorts,
replace if defective. If error is still
present, replace the PCB.
13-65
Fan speed
error
Reset the boiler, if needed. Check
the silencer-fan connection and be
sure that fan suction is not blocked.
Check fan and it’s cable connec
-
tions for interruptions and shorts,
replace if defective. If error is still
present, replace the PCB.
16-64
Flue tem-
perature
signalize
overheating
Check if the flue duct installed cor
-
rectly. Check flue gas path against
blockage. Check flue temperature
sensor resistance using a multime-
ter connected across the thermis-
tor’s terminal pins.
1J-64
High limit
thermostat
signalize
overheating
Check the radiator valves on the
central heating circuit, open them
if they are closed. Check high limit
thermostat cable connections for
interruptions or shorts, replace if
defective. Check pump max capac
-
ity (P08), increase the parameter
value to 100% if it is not. Check
by-pass valve and plated heat
exchanger against blockage.
80-01
Return
temperature
sensor fault
Check continuity between the sen
-
sor and PCB, replace wire harness
if necessary. Check flue tempera
-
ture sensor resistance using a
multimeter connected across the
thermistor’s terminal pins.
Содержание D2CND028A1AA
Страница 43: ......