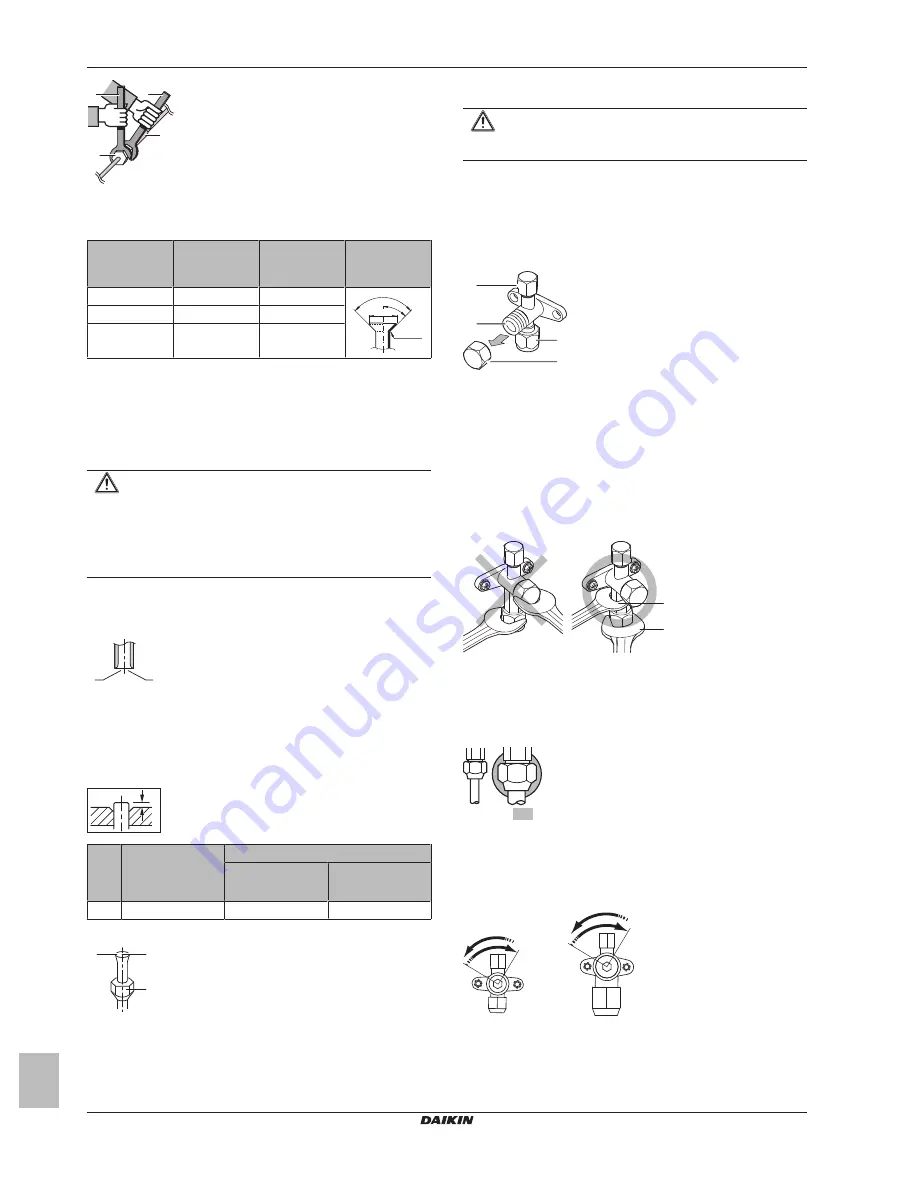
6 Installation
Installer reference guide
14
RXF50+60B2_RXF71A2_RXP50~71L2_(A)RXM42~71N2_RXJ50N2_
RXA42+50B2
R32 split series
4P513661-6B – 2018.05
a
b
c
d
a
Torque wrench
b
Spanner
c
Piping union
d
Flare nut
Piping size
(mm)
Tightening
torque (N•m)
Flare
dimensions (A)
(mm)
Flare shape
(mm)
Ø6.4
15~17
8.7~9.1
R=0.4~0.8
45° ±2
90°±2
A
Ø12.7
50~60
16.2~16.6
Ø15.9
63~75
19.3~19.7
6.4.4
Pipe bending guidelines
Use a pipe bender for bending. All pipe bends should be as gentle
as possible (bending radius should be 30~40 mm or larger).
6.4.5
To flare the pipe end
CAUTION
▪ Incomplete flaring may cause refrigerant gas leakage.
▪ Do NOT re-use flares. Use new flares to prevent
refrigerant gas leakage.
▪ Use flare nuts that are included with the unit. Using
different flare nuts may cause refrigerant gas leakage.
1
Cut the pipe end with a pipe cutter.
2
Remove burrs with the cut surface facing down so that the
chips do NOT enter the pipe.
a
b
a
Cut exactly at right angles.
b
Remove burrs.
3
Remove the flare nut from the stop valve and put the flare nut
on the pipe.
4
Flare the pipe. Set exactly at the position as shown in the
following figure.
A
Flare tool for R32
(clutch type)
Conventional flare tool
Clutch type
(Ridgid-type)
Wing nut type
(Imperial-type)
A
0~0.5 mm
1.0~1.5 mm
1.5~2.0 mm
5
Check that the flaring is properly made.
a
b
c
a
Flare’s inner surface MUST be flawless.
b
The pipe end MUST be evenly flared in a perfect circle.
c
Make sure the flare nut is fitted.
6.4.6
Using the stop valve and service port
CAUTION
Do NOT open the valves before flaring is complete. This
would cause refrigerant gas leakage.
To handle the stop valve
Take the following guidelines into account:
▪ The stop valves are factory closed.
▪ The following figure shows the stop valve parts required when
handling the valve.
c
d
a
b
a
Service port and service port cap
b
Valve stem
c
Field piping connection
d
Stem cap
▪ Keep both stop valves open during operation.
▪ Do NOT apply excessive force to the valve stem. Doing so may
break the valve body.
▪ ALWAYS make sure to secure the stop valve with a spanner, then
loosen or tighten the flare nut with a torque wrench. Do NOT place
the spanner on the stem cap, as this could cause a refrigerant
leak.
a
b
a
Spanner
b
Torque wrench
▪ When it is expected that the operating pressure will be low (e.g.
when cooling will be performed while the outside air temperature
is low), sufficiently seal the flare nut in the stop valve on the gas
line with silicon sealant to prevent freezing.
Silicon sealant; make sure there is no gap.
To open/close the stop valve
1
Remove the stop valve cover.
2
Insert a hexagon wrench (liquid side: 4 mm, gas side: 4 mm)
into the valve stem and turn the valve stem:
Counterclockwise to open.
Clockwise to close.
3
When the stop valve CANNOT be turned any further, stop
turning. The valve is now open/closed.
Содержание ARXM50N2V1B
Страница 28: ...4P513661 6B 2018 05 Copyright 2018 Daikin ...