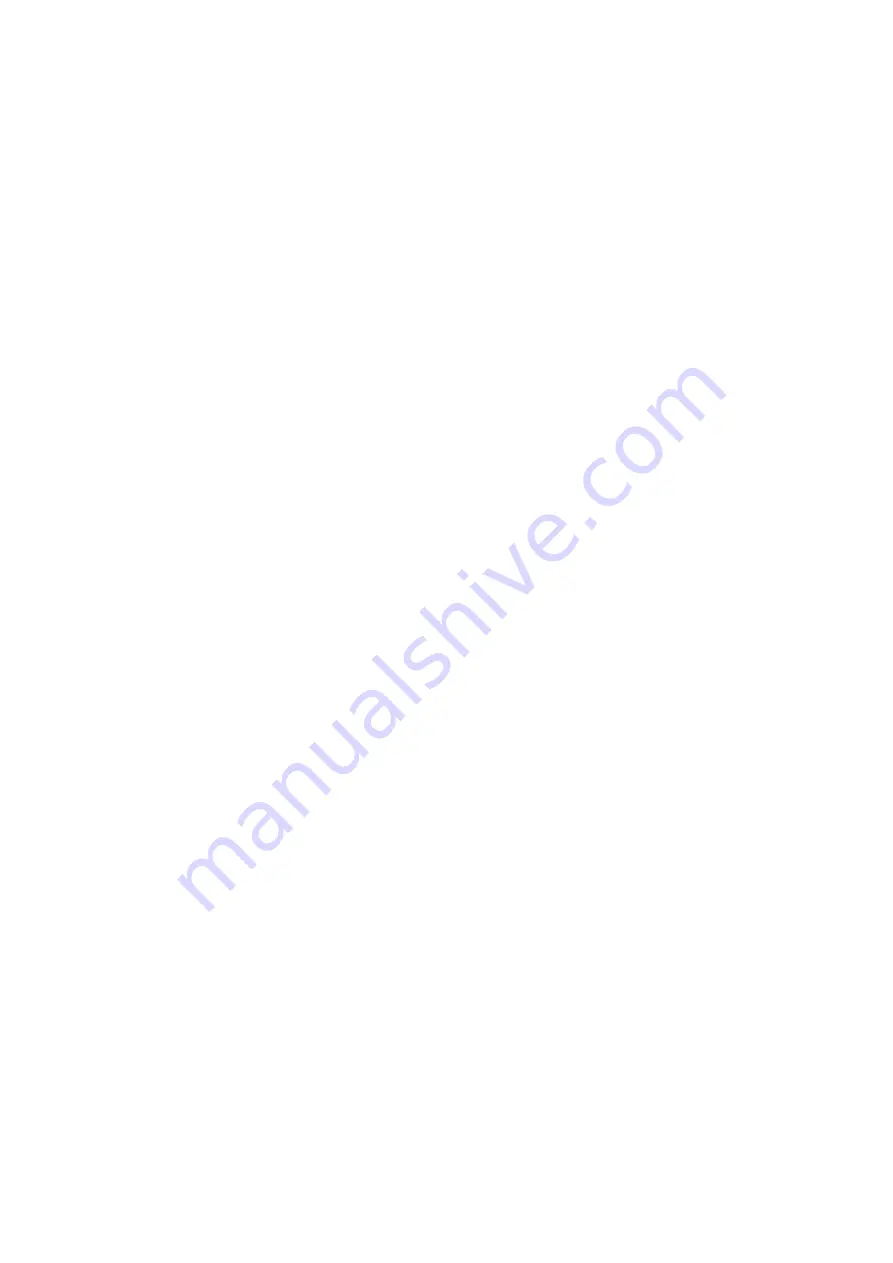
No. P10224
P. 33 / 47
11. APPLIED FUNCTION (continued)
⑧
Error in primary/secondary current detection wire
The WARNING lamp lights and the welding power source stops automatically due to the
current detection wire error. Start the welding power source after turning off the CONTROL
POWER switch and checking to make sure connector CN11 or CN14 of the P.C.B.P6906P is
not removed.
⑨
Control power
±
15 V error/input voltage shortage
When control power
±
15 V drops, or the input voltage becomes under 414V, the WARNING
lamp lights and the welding power source stops automatically. To cancel the error, start the
welding machine again after turning off CONTROL POWER switch and checking the
nonpresence of error in the welding power source.
⑩
Arc voltage detection wire error
The WARNING lamp lights and the welding power source stops automatically for arc voltage
detection wire error. In this case, turn on the POWER switch after turning off the POWER
switch and checking to make sure if there is no error arc voltage detection wire or electrode.
⑪
Microcomputer error
When any microcomputer error is detected, the WARNING lamp lights and the welding
machine stops automatically.
⑫
Communication error with robot
When communication between the welding machine and the robot control device has failed, the
WARNING lamp lights and the welding machine stops automatically. In this case, turn off the
POWER switch and connect again.
⑬
Gas check error
The WARNING lamp flashes and the welding power machine stops automatically, when
starting the equipment by pressing the GAS switch on the front panel set to CHECK, or when
more than two minutes has passed after GAS switch was set to CHECK. Set the GAS switch to
WELD to cancel the error.
⑭
Encoder error
The WARNING lamp lights and the welding power source stops automatically, if the signals
from encoder are disconnected by breaking while using the only wire feeder mounted an encoder.
In this case, solve any cause of the error before connecting the POWER switch. The error is
canceled by receiving control signals from a robot.
⑮
Secondary transistor error
The WARNING lamp lights and the welding power source stops automatically when surge
voltage of the secondary transistor is excessively high. In this case, after canceling the error,
following the instructions described in 11.5, turn on the POWER switch again.