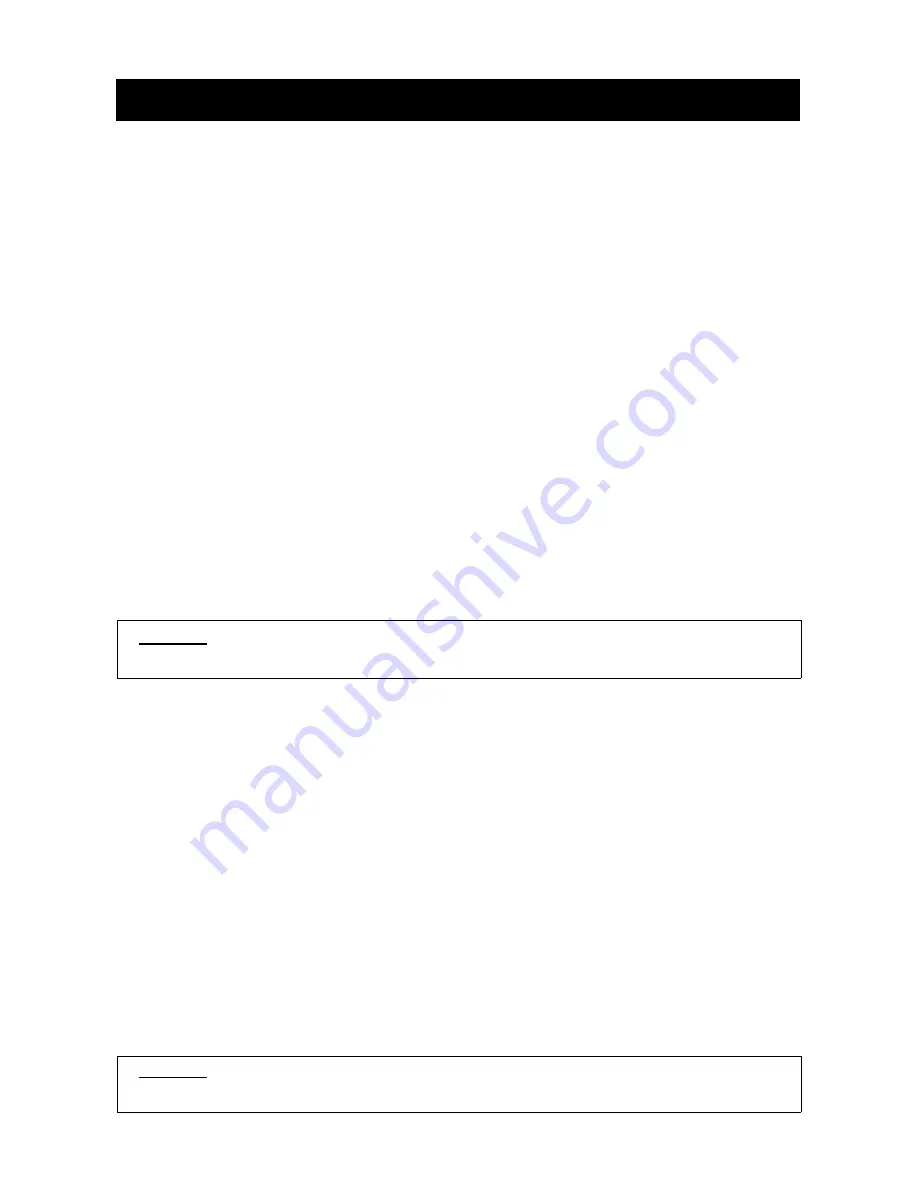
5
SERVICING PRECAUTIONS
u
Electrostatically Sensitive (ES) Devices
Some semiconductor (solid state) devices can be damaged easily by static electricity.
Such components commonly are called Electrostatically Sensitive (ES) Devices.
The examples of typical ES devices are integrated circuits, some field-effect transistors and
semiconductor “chip” components. The following techniques should be used to help reduce the
incidence of component damage caused by static electricity.
1. Immediately before handling any semiconductor component or semiconductor-equipped assembly,
drain off any electrostatic charge on your body by touching a known earth ground. Alternatively,
obtain and wear a commercially available discharging wrist strap device which should be removed for
potential shock reasons prior to applying power to the unit under test.
2. After removing an electrical assembly equipped with ES devices, place the assembly on a conductive
surface such as aluminum foil to prevent electrostatic charge buildup or exposure of the assembly.
3. Use only a grounded-tip soldering iron to solder or unsolder ES devices.
4. Use only an anti-static type solder removal device. Some solder removal devices not classified as
“anti-static” can generate enough electrical charges to damage ES devices.
5. Do not use freon-propelled chemicals. These can generate enough electrical charges to damage ES devices.
6. Do not remove a replacement ES device from its protective package until immediately before you are
ready to install it. (Most replacement ES devices are packaged with leads electrically shorted together
by conductive foam, aluminum foil or comparable conductive material).
7. Immediately before removing the protective material from the leads of a replacement ES device,
touch the protective material to the chassis or circuit assembly into which the device will be installed.
CAUTION
Be sure that no power is applied to the chassis or circuit, and observe all other safety precautions.
8. Minimize bodily motions when handling unpackaged replacement ES devices. (Otherwise harmful
motion such as the brushing together of your clothes fabric or the lifting of your foot from a carpeted
floor can generate enough static electricity to damage an ES devices).
u
General Soldering Guidelines
1. Use a grounded-tip, low-wattage soldering iron with appropriate tip size and shape that will maintain
tip temperature within a 550°F-660°F (288°C-316°C) range.
2. Use an appropriate gauge of RMA resin-core solder composed of 60 parts tin/40 parts lead.
3. Keep the soldering iron tip clean.
4. Throughly clean the surface to be soldered. Use a small wire-bristle (0.5 inch or 1.25cm) brush with a
metal handle. Do not use freon-propelled spray-on cleaners.
5. Use the following soldering technique:
a. Allow the soldering iron tip to reach normal temperature (550°F to 660°F or 288°C to 316°C)
b. Hold the soldering iron tip and solder strand against the component lead until the solder melts.
c. quickly move the soldering iron tip to the junction of the component lead and the printed circuit foil,
and hold it there only until the solder flows onto and around both the component lead and the foil.
d. Closely inspect the solder area and remove any excess or splashed solder with a small wire-bristle brush.
CAUTION
Work quickly to avoid overheating the circuit board printed foil.
Содержание L500B
Страница 1: ...ServiceManual TFT LCD MONITOR Model L500B DAEWOO ELECTRONICS CO LTD OVERSEAS SERVICE DEPT...
Страница 24: ...25 SCHEMATIC DIAGRAM u MAIN88281A...
Страница 25: ...26 SCHEMATIC DIAGRAM u TOP CIRCUIT...
Страница 26: ...27 SCHEMATIC DIAGRAM u BUFFER...
Страница 27: ...28 SCHEMATIC DIAGRAM u POWER DC DC...
Страница 28: ...29 SCHEMATIC DIAGRAM u MEMORY...
Страница 29: ...30 SCHEMATIC DIAGRAM u MICOM...
Страница 30: ...31 SCHEMATIC DIAGRAM u RGB SYNC...
Страница 31: ...32 SCHEMATIC DIAGRAM u TDA8752A...
Страница 32: ...33 EXPLODED VIEW MECHANICAL PARTS LIST...