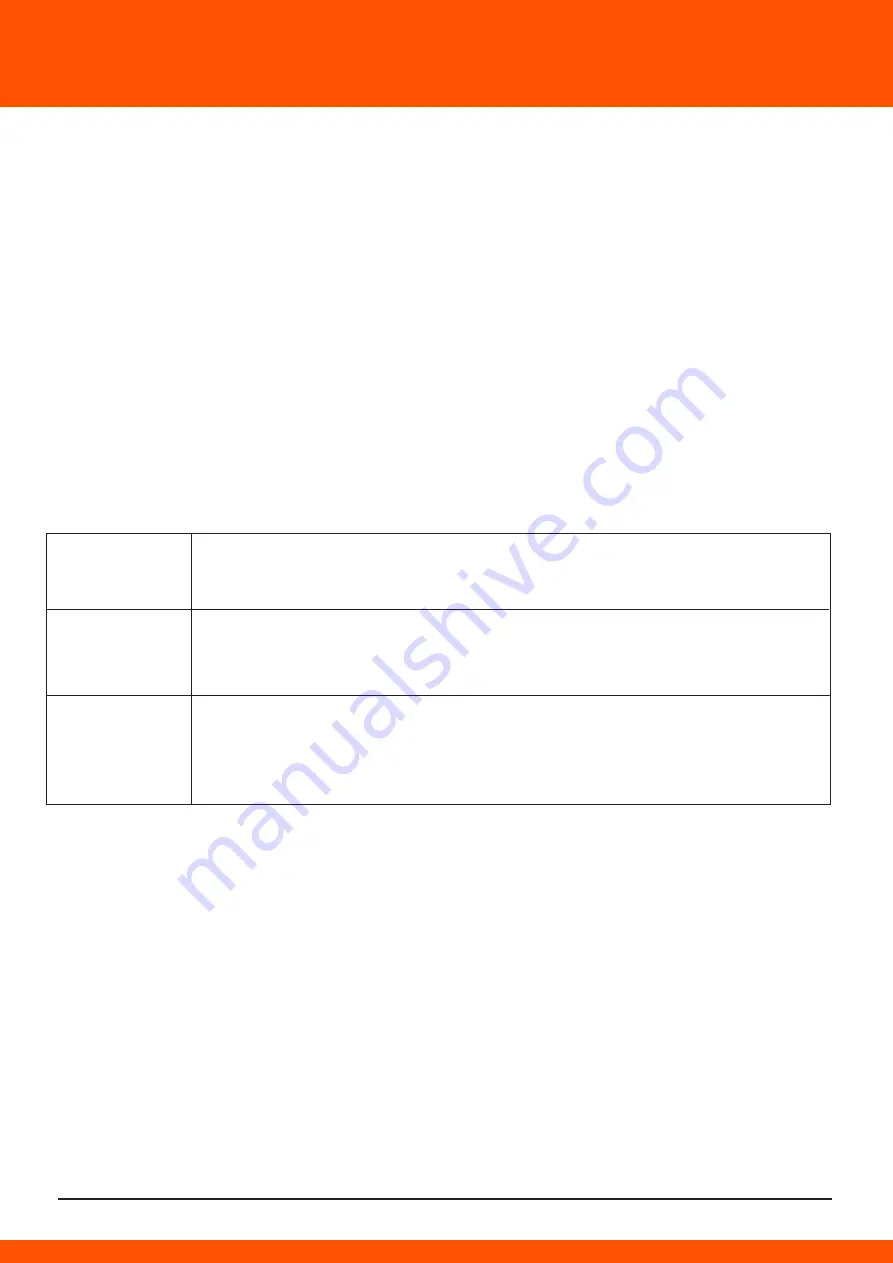
Blown Air Drying
Remove the covers from all apertures to allow the escape of the water-laden air. During drying,
air must be able to flow freely through the generator in order to carry off the moisture.
Direct hot air from two electrical fan heaters of around 1-3 KW into the generator air inlet aper-
tures. Ensure the heat source is at least 300mm away from the windings to avoid over heating
and damage to the insulation.
Apply the heat and plot the insulation value at half hourly intervals. The process is complete
when the parameters covered in the section entitled, 'Typical Drying Out Curve', are met.
Remove the heaters, replace all covers and re-commission as appropriate.
If the set is not to be run immediately ensure that the anticondensation heaters are energized,
and retest prior to running.
Shirt Circuit Method
NOTE: This process shou ld only be performed by a competent engineer familiar with safe
operating practices within and around generator sets of the type in question. Ensure the gene-
rator is safe to work on, initiate all mechanical and electrical safety procedures pertaining to the
genset and the site.
Bolt a short ci rcuit of adequate current carrying capacity, across the main terminals of the
generator. The shorting link should be capable of taking full load current.
Disconnect the cables from terminals "X" and "XX" of the AVR.
Connect a variable de supply to the "X" (positive) and "XX" (negative) field cables. The de
supply must be able to provide a current up to 2.0 Amp at 0-24Volts.
Position a suitable ac ammeter to measure the shorting link current.
Set the de supply voltage to zero and start the generating set. Slowly increase the de voltage to
pass current through the exciter field winding. As the excitation current increases, so the stator
current in the shorting link will increase. This stator output current level must be monitored, and
not allowed to exceed 80% of the generators rated output current.
After every 30 minutes of this exercise: Stop the generator and switch off the separate excita-
tion supply, and measure and record the stator winding IR values, and plot the results.
The resulting graph should be compared with the classic shaped graph. This drying out proce-
dure is complete when the parameters covered in the section entitled 'Typical Drying Out
Curve' are met.
Once the insulation Resistance is raised to an acceptable level minimum value 10MΩ - the de
supply may be removed and the exciter field leads "X" and "XX" re-connected to their terminals
on the AVR.
Rebuild the genset, replace all covers and re-commission as appropriate.
If the set is not to be run immediately ensure that the anticondensation heaters are energised,
and retest the generator prior to running.
Typical Drying Out Curve
Whichever method is used to dry out the generator the resistance should be measured every
half-hour and a curve plotted as shown.(Fig 9)
The illustration shows a typical curve for a machine that has absorbed a considerable amount
of moisture. The curve indicates a temporary increase in resistance, a fall and then a gradual
rise to a steady state. Point 'A', the steady state, must be greater than 1.0MΩ (If the windings
are only slightly damp the dotted portion of the curve may not appear).
For general guidance expect that the typical time to reach point 'A' will be approximately 3
hours for a LV 6 generator.
Drying should be continued after point "A" has been reached for at least one hour.
It should be noted that as winding temperature increases, values of insulation resistance may
significantly reduce. Therefore, the reference values for insulation resistance can only be esta-
blished with windings at a temperature of approximately 20°C.
After drying out, the insulation resistances should be rechecked to verify minimum resistances
quoted above are achieved. On re-testing it is recommended that the main stator insulation
resistance is checked as fol lows:
-Separate the neutral leads.
Ground V and W phase and megger U phase to ground
Ground U and W phase and megger V phase to ground
Ground U and V phase and megger W phase to ground.
If the minimum value of 1.0MΩ is not obtained, drying out must be continued and the test
repeated.
If the minimum value of 1.0MΩ for all components cannot be achieved rewinding or refurbish-
ment of the generator will be necessary.
The generator must not be put into service until the minimum value, Of 1.0MΩ for all compo-
nents, can be achieved.
8.2 BEARINGS
All bearings are supplied from the factory pre-packed with Kluber Asonic GHY 72 grease.
Do not mix kluber Asonic GHY 72 with any grease of different specifications. Mixing grease of
differing specifications will reduce bearing life. The specification for Kluber Asonic FHY 72 is
available on request from the factory.
Sealed for life bearings are fitted with integral seals and are not re-greasable.
BEARING LIFE
IMPORTANT!
The life of a bearing in service is subject to the working conditions and the
environment.
IMPORTANT!
High levels of vibration from the engine or misalignment of the set will
stress the bearing and reduce its service life. If the vibration limits set out
im BS 5000-3 and ISO 8528-9 are exceeded bearing life will be reduced.
Refer to 'vibration’ below.
IMPORTANT!
Long stationary periods in an environment where the generator is subject
to vibration can cause false brinneling, which puts flats on the ball and
grooves on the races, leading to premature failure.
IMPORTANT!
Very humid atmospheric or wet conditions can emulsify the grease causing
corrosion and deterioration of the grease, leading to premature failure of
the
bearings.
HEALTH MONLTORING OF THE BEARINGS
It recommends that the user check the bearing condition, using monitoring equipment, to
determine the state of the bearings. The 'best practice' is to take initial readings as a base line
and periodically monitor the bearings to detect a deteriorating trend. It will then be possible to
plan a bearing change at an appropriate generating set or engine service interval.
VLBRATION
The generators are designed ti withstand the vibration levels encountered on generating sets
built to meet the requirements of ISO 8528-9 and BS5000-3. (Where ISO 8528 is taken to be
broad band measurements and BS5000 refers to the predominant frequency of any vibrations
on the generating set.)
Definition of BSS000-3
Generators shall be capable of continuously withstanding linear vibration levels with amplitudes
of 0.25 mm between 5 Hz and velocities of 9.0 mm/s. Between 8 Hz and 200 Hz when measu-
red at any point directly on the carcass or main frame of the machine. These limits refer Only to
the predominant frequency of v ibration of any complex waveform.
Definition of ISO 8528-9
ISO 8528-9 refers to a broad band of frequencies, the broad band is taken to be between 2
Hertz and 300 Hertz. The table below is an example from ISO 8528-9 (value 1 ). This simplified
table lists the vibration limits by kVA range and speed for acceptable genset operation.
IMPORTANT!
Exceeding either o f the above specifications will have a detrimental effect
on the life of the bearing. This will invalidate the generator warranty. If you
are in any doubt, contact Newage International limited.
If the vibration levels of the generating set are not within the parameters quoted above.
1. consult the genset builder. The genset builder should address the genset design to reduce
the vibration levels as much ad possible.
2. Discuss the impact of not meeting the above levels on both bearing and generator life
expectancy.
Where requested, or deemed necessary, Newage will work with the genset builder in an
attempt to find a satisfactory solution.
BEARING 'SERVICELIFE' EXPECTANCY
Bearing manufacturers recognize that the "service life" of their bearings is dependent upon
many factors that are not in their control, they cannot therefore quote a "service life".
Although "service life" cannot be guaranteed, it can be maximized by attention to the genera-
ting set design. An understanding of the genset application will also help the user to maximize
the service life expectancy of the bearings. Particular attention should be paid to the alignment,
reduction of vibration levels, environmental protection, maintenance and monitoring procedu-
res. We does not quote life expectancy figures for bearings, but suggests practicable replace-
ment intervals based on the L 10 life of the bearing, the grease and the recommendations of
the bearing and grease manufacturers. For general-purpose applications, provid ing the vibra-
tion levels do not exceed the levels stated in ISO8528-9* and BS5000-3* and the ambient
temperature does not exceed 50°C the following approximations can be applied when *
(See section on vibration)
Sealed for life Bearings. - Approximately 30,000hours.
Re-greaseable bearings.- Approximately 40,000hours.
This is provided the correct maintenance is carried out, and only Kluber Asonic GHY 72 grease
(or equivalent) is used in all bearings. It is important to note that bearings in service. Under
good operating conditions, can continue to run beyond the remembered re placement period.
It should also be remembered that the r isk of bearing failure increases with time.
8.3 ALR FILTERS
Air filters for the removal of airborne particulate matter (dus) are offered as an addition to the
standard build option. Filters on it's need to be ordered with the generator. Air filters need to
be charged with oil before the genset is put to work (see 8.3.2) The frequency of fi lter mainte-
nance will depend upon the severity of the site conditions. Regular inspection of the elements
will be required to establish when cleaning is necessary.
Danger!
Removal of filter elements enables access to LIVE parts. Only remove elements
with the generator out of service.
8.3.1 CLEANING PROCEDURE
Remove the filter elements from the filter frames. Immerse of flush the element with a suitable
degreasing agent until the element is cleas.
As an alternative procedure a high-pressure water hose with a flat nozzle can be used. Sweep
the water spray back and forth across the element from the clean side (fine mesh side of
element) holding the nozzle firm ly against the element surface. Cold water may be adequate
depending upon type of contamination although hot water is preferable.
The element can be inspected for cleanliness by looking through the filter towards the light.
When the roughly clean, no cloudy areas will be seen. Dry elements thoroughly before attemp-
ting to carry out the recharging procedure.
8.3.2 RECHARGING (GHARGING) AIR FILTERS
Charging is best done by totally immersing the dry element into a dip tank containing "Filterko-
te Type k" or commercial lubricating oil SAE 20/50. oils of higher or lower viscosity are not
recommended.
Allow elements to completely drain before refitting the elements into the frames and putting
into service.
8.4 FAULT FINDING
IMPORTANT!
Before commencing any faultfinding procedures, examine all wiring for
broken or loose connections.
Two types of AVR can be fitted to the WH generator. The Refer to the generator nameplate for
type of AVR fitted.
8.4.1 MX341 AVR, FAULT FINDING
8.5 SEPARATE EXCITATION TEST PROCEDURE
The generator windings, diode assembly and AVR can be checked using the appropriate
following sections.
8.5.1 GENERATOR WINDINGS, ROTATING DIODES and PERMANENT MAGNET GENERA-
TOR (PMG)
IMPORTANT!
The resistances quoted apply to a standard winding. For generators
having windings or voltages other than those specified refer to fac-
tory for details. Ensure all disconnected leads are isolated and free
from
earth.
IMPORTANT!
Incorrect speed setting will give proportional error in voltage out put.
Checking Generator Windings and Rotating Diodes
This procedure is carried out w ith lead X and XX disconnected at the AVR or transformer
control rectifier bridge and using a 12 volt d. c. Supply to leads X and XX.
Start the set and run at rated speed.
Measure the voltages at the main output terminals U, V and W. if voltages are balanced and
/-10% of the generator nomial voltage, refer to 7 .5.1.1.
Check voltages at AVR terminals 6, 7 and 8. These should be balanced and between 170-250
volts.
If voltages at main terminals are balanced but voltage at 6, 7
and 8 are unbalanced, check continuity of leads 6,7 and 8.
If voltages are unbalanced , refer to 7 .5.1.2.
8.5.1.1 BALANCED MAIN TERMINAL VOLTAGES
If all voltages are balanced within 1 % at the main terminals, it can be assumed that all exciter
windings, main windings and main rotating diodes are in good order ,and the fault is in the
AVR or transformer control. Refer to subsection 7 .3.2 for test procedure.
If voltages are balanced but low, there is a fault in the main excitation windings or rotating
diode assembly. proceed as follows to identity:-
Rectifier Diodes
The diodes on the main rectifier assembly can be checked with a multimeter. The flexible leads
connected to each diode should be disconnected at the terminal end, and the forward and
reverse resistance checked. A healthy diode will indicate a very high resistance ( infinity) in the
reverse direction, and a low resistance in the forward direction. A faulty diode will give a full
deflection reading in both directions with the test meter on the 10,000 ohms scale, or an
infinity reading in both directions. On an electronic digital meter a healthy diode will give a low
reading in one direction, and a high reading in the other.
Replacement of Faulty Diodes
The rectifier assembly is split into two plates, the positive and negative, and the main rotor is
connected across these plates. Each plate carries 3 diodes, the negative plate carrying negati-
ve biased diodes and the positive plate carrying positive biased diodes. Care must be taken to
ensure that the correct polarity diodes are fitted to each respective plate. When fitting the
diodes to the plates they must be tight enough to ensure a good mechanical and electrical
contact, but should not be over-tightened. The recommended torque tightening is 4.06-4.74
Nm (36-42Ib in).
Surge suppressor
The surge suppressor is a metal-oxide varistor connected across the two rectifier plates to
prevent high transient reverse voltages in the fie ld winding from damaging the diodes. This
device is not polarized and will show a virtually infinite reading in both directions with an ordi-
nary resistance meter. If defective this will be visible by inspection, since it will normally fail to
short circuit and show signs of disintegration. Replace if faulty.
If after establishing and correcting any fault on the rectifier assembly the output is still low
when separately excited, then the main rotor, exciter stator and exciter rotor winding resistan-
ces should be checked (see Resistance charts ), as the fault must be in one of these windings.
The exciter stator resistance is measured across leads X and XX. The exciter rotor is conne.
Main Excitation Windingscted to six studs that also carry the diode lead t erminals. The main
rotor winding is connected across the two rectifier plates. The respective leads must be
disconnected before taking the readings.
8.5.1.2 UNBALANCED MAIN TERMINAL VOLTAGES
If voltages are unbalanced, this indicates a fault on the main stator winding or main cables to
the circuit breaker. NOTE: Faults on the stator winding or cables may also cause noticeable
load increase on t he engine when excitation is applied. Disconnect the main cables and sepa-
rate the winding leads U1-U2,(U5-U6),V1-V2,(V5-V6),W1-W2,(W5-W6) to isolate each winding
section. Note: -leads suffixed 5 and 6 apply to 12 wire windings only.
Measure each section resistance values should be balanced and /- 10% fo the value.
Measure insulation resistance between sections and each section to earth.
Unbalanced or incorrect winding resistances and/or low insulation resistances to earth indica-
te rewinding of the stator will be necessary. Refer to removal and replacement of component
assemblies' subsection 8.5.3.
CAUTION! Reference to local electricity regulations or safety rules should be made go
ensure correct earthing procedures h ave been followed.
6.5 PROTECTION
It is the responsibility of the end user and his contractors/subcontractors to ensure that the
overall system protection meets the needs of any inspectorate, local electricity authority of
safety rules, pertaining to the site and it's location. To enable the system designer to achieve
the necessary protection and / or discrimination, fault current curves are available on request
from the factory, together with generator reactance values to enable fault current calculations
to be made.
Warning!
Incorrect inst allation and/or protective systems can result in personal injury
and/or equipment damage. Installers must be qualified to perform electrical
installation
work.
6.6 COMMISSIONONG
Ensure that all external cabling is correct and that all of the generating set manufacturer's
pre-running checks have been carried out before starting the set.
Generators fitted with air filters should have the filters charged with oil prior to commissioning.
Refer to Service section for charging procedure (subsection 7.3.2)
The generator AVR controls will have been adjusted during the generating set manufacturer's
tests and should normally not require further adjustment.
Should malfunction occur during commissioning refer to Service and Maintenance section
'Fault Finding' procedure (subsection? A)
7. ACCESSORIES
Generator control accessories may be f itted, as an option, in the generator terminal box. If
fitted at the time of supply, the wiring diagram(s) in the back of this book shows the connec-
tions. When the options are supplied separately, fitting instructions are provided with the
accessory.
7.1 REMOTE VOLTAGE ADJUST
A remote voltage adjust(hand trimmer) can be fitted.
The remote voltage adjustment potentiometer is connected across AVR terminals 1&2.
These terminals are normally linked.
When the remote voltage adjust potentiometer is used the link across terminals 1 & 2 must be
removed.
On SX440 the link 1&2 is on an adjacent terminal block.
7.2 PARALLEL OPERATION
IMPORTANT!
Failure to meet conditio ns 1, 2 and 3 when closing the circuit breaker, will
generate excessive mechan ical a nd el ectrical stresses, resulting in
equipment
damage.
Understanding of the following notes on parallel operation is useful before attempting the
fitting or setting of the droop kit accessory. When operating in parallel with other generators
or the mains, it is essential that the phase sequence of the incoming generator matches that of
the busbar and also that all of the following conditions are met before the circuit breaker of the
incoming generator is closed on to the busbar (or operational generator).
1. Frequency must match within close limits.
2. voltages must match within close limits.
3. phase angle of voltages must match within close limits.
A variety of techniques, varying from simple synchronising lamps to fully automatic synchroni-
sers, can be used to ensure these conditions are met. Once connected in parallel a minimum
instrumentation level per generator of voltmeter, ammeter, wattmeter (measuring total power
per generator), and frequency meter is required in order to adjust the engine and generator
controls to share KW in relation to engine ratings KVAr in relation to generator ratings.
It is important recognize that:
1. kW are derived from the engine, and speed governor characteristics determine the kW
sharing between sets and.
2. KVAr are derived from the generator, and excitation control characteristics determine the
KVAr sharing.
Reference should be made to the generating set manufacturer's instructions for setting the
governor controls.
7.2.1 DROOP
The most commonly used method of KVAr sharing is to create a generator voltage characteris-
tic that fa lls with a decreasing power factor (increasing KVAr). This is achieved with a current
transformer (C.T.) that provides a signal dependent on current phase angle (i.e. power factor) to
the AVR. The current transformer has a burden resistor on the AVR board, and a percentage of
the burden resistor voltage is summed into the AVR circuit. In creasing droop is obtained by
turning the DROOP control potentiometer clockwise.
The diagrams below indicate the effect of droop in a simple two generator system:
Generally 5% droop at full load current zero power factor is sufficient to ensure KVAr sharing.
If the droop accessory has been supplied with the generator it will have been tested to ensure
correct polarity and set to a nominal leve of droop. The final level of droop will be set during
generating set commissioning. Although nominal droop setting may be factory set it is advisa-
ble to go through the setting procedure below.
7.2.1.1 SETTING PROCEDURE
Depending upon available load the fol lowing settings should be used, laa are based on rated
current level.
0.8 P. F. load (at full load current) set droop to 3%
Zero P. F. load (at full load current ) set droop to 5%
Setting the droop with low power factor load is the most accurate.
Run each generator as a single unit at rated frequency or rated fre4% depending
upon type of governor and nominal voltage. Apply available load to rated current of the
generator. Adj ust 'DROOP' control potentiometer to give droop in line with above table. cloc-
kwise rotation increases amount or droop. Refer to Fig. 5a of 5b for potentiometer locations.
Note 1)
Reverse polarity of the C. T. will raise the generator voltage with load. The polarities S1&S2
shown on the wiring diagrams are correct for clockwise rotation of the generator looking at the
drive end. Reversed rotation requires S1&S2 to be reversed.
Note 2)
The most important aspect is to set all generators equal. The precise level of droop is less
critical.
Note 3)
A generator operated as a single unit with a drop circuit set at rated load 0.8 power factor is
unable to maintain the usual O.S% regulation. A shorting switch can be connected across
S1&S2 to restore regulation for single running.
IMPORTANT!
LOSS OF FUEL to an engine can cause Its generator to motor with conse
quent damage to the generator windings. Reverse power relays should be
fitted to trip main circuit breaker.
IMPORTANT!
LOSS OF EXCITATION to the generator can result in large c urrent oscilla
tions with consequent damage to generator winndings. Excitation loss
detection equipment should be fitted to trip main circuit breaker.
IMPORTANT!
When using this connection arrangement a shorting switch is required
across each C.T. Burden (terminals S1&S2.) The switch must be closed a)
when a generating set is not running and b) when a generating set is selec
ted for single running.
Should 'Asiatic' control of the generator be required, request the diagrams from the factory.
The setting procedure is exactly the same as for DROOP. (Subsection 7.2.1.1)
8. SERVICE AND MAINTENANCE
As part of routine maintenance procedures. Periodic attention to winding condition (particularly
when generators have been idle for a long period ) and bearings is recommended. (Refer to
subsections 8.1 and 8.2 respectively).
When generators are fitted with air filters regular inspection and filter maintenance is required.
(Refer to subsection 8.3).
8.1 WINDING CONDITION
Danger!
Service and fault finding procedures present hazards that can result in severe
personal injury or death. Only personnel qualified to perform electrical and me
chanical service should carry out these procedures. Ensure engine start circuits
are disabled before commencing service or maintenance procedures. Isolate any
anti-condensation heater supply.
Guidance or Typical Insulation Resistance [IR]
Values he following is offered as general information about IR values. The aim is to provide
guidance about the typical IR Values for generator from new through to the point of refurbish-
ment.
New machine
The generators Insulation Resistance, along with many Other critical factors, will have been
measured during the alternator manufacturing process. The generator will have been transpor-
ted with an appropriate packaging suitable for the method of delivery to the Generating Set
assemblers works, where we expect it to be stored in a suitable location protected from adver-
se conditions.
However, absolute assurance that generator will arrive at the Gen-set production line with IR
values still at the factory test levels of above 100MΩ cannot be guaranteed.
At Generating Sat Manufacturers Works The generator should have been transported and
stored such that it will be de livered to the assembly area in a clean dry condition. If held in
appropriate storage conditions the generator IR value should typically be 25MΩ If the unused/-
new generator's IR values fall below 10MΩ then a drying out procedure should be implemented
by one of the processes outlined below before being dispatched to the end customer's site.
Some investigation should be undertaken into the storage conditions of the generator while on
site.
Generators in Service
Whilst It is known that a generator will give reliable service with an IR value of just 10MΩ. For a
relatively new generator to be so low it must have been subjected to inappropriate operating or
storage conditions.
Any temporary reduction in IR values can be restored to expected values by following one of
the drying out procedures.
8.1.1 WINDING CONDITION ASSESSMENT
CAUTION! The AVR should be disconnected and the Resistance Temperature Detec tor
(R.T.D.) leads grounded during this test.
70
Содержание DAGFS Series
Страница 10: ...9 2 Connect the battery red wire for anode black wire for cathode ...
Страница 11: ...10 3 Press diesel pump to exhaust air until feel pressure 4 Turn on the emergency stop button ...
Страница 12: ...11 5 Use the key to turn on the generator keep it running 6 Operating control panel in order STOP Manual Start ...
Страница 14: ...13 Final step Finish set up the generator and then turn on breaker for auto protection ...
Страница 26: ...25 ...
Страница 27: ...26 ...
Страница 28: ...27 ...
Страница 29: ...28 TYPICAL APPLICATIONS ...
Страница 30: ...29 ...
Страница 31: ...30 7 EXPLODING VIEW AND PARTS LIST applies to all models CYLINDER BLOCK ASSEMBLY ...
Страница 34: ...33 CYLINDER HEAD ASSEMBLY ...
Страница 36: ...35 2 4 4 NUMBER PART NAME QUANTITY 34 35 36 Host ring Bolt M10X20 Spring washerφ10 ...
Страница 37: ...36 CRANK AND CONNECTING ROD MECHANISM ...
Страница 39: ...38 VALVE ACTUATING MECHANISM ...
Страница 41: ...40 FUEL SUPPLY SYSTEM ...
Страница 43: ...42 LUBRICATING SYSTEM ...
Страница 46: ...45 COOLING SYSTEM ...
Страница 49: ...48 ELECTRIC SYSTEM ...
Страница 91: ...www daewoopowerproducts com Manufactured under license of Daewoo International Corporation Korea ...