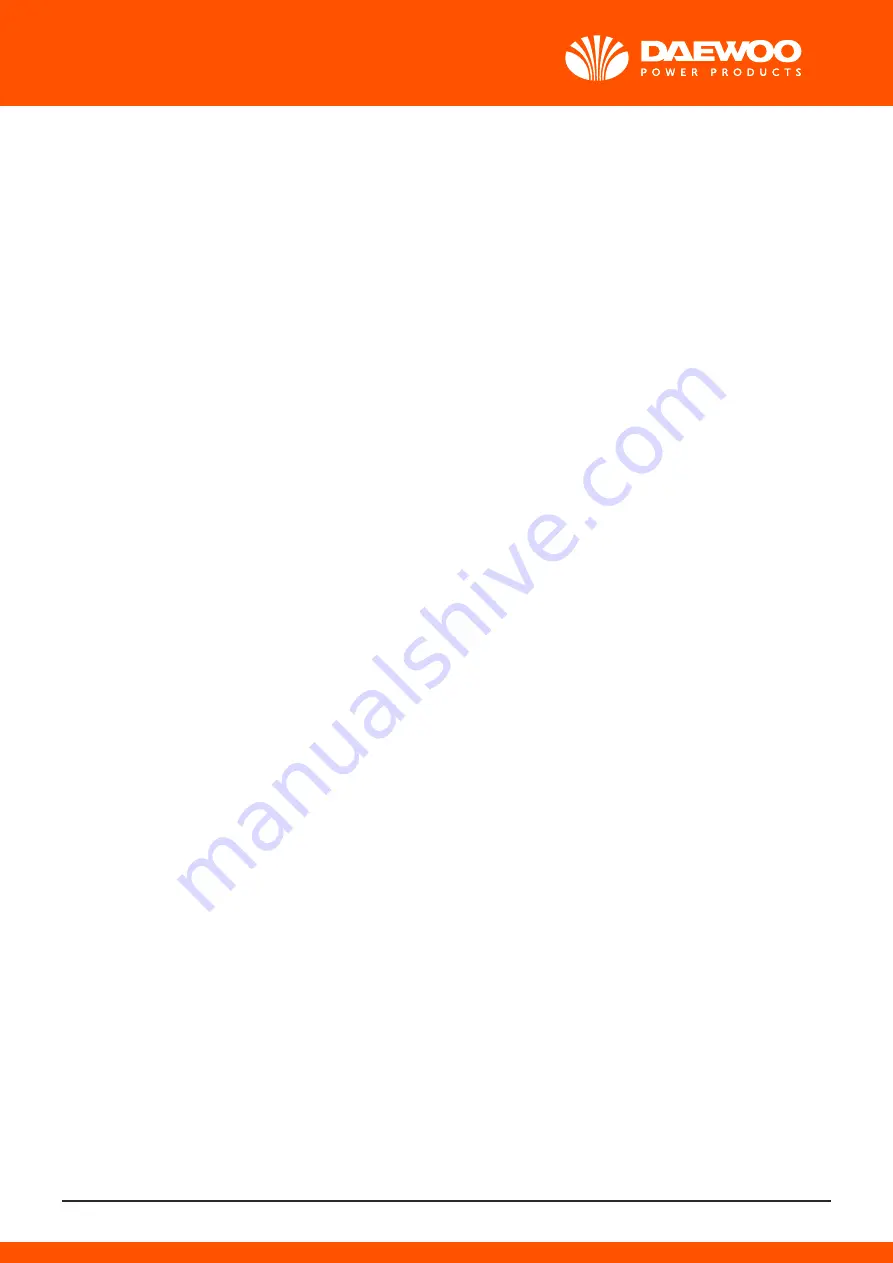
INDEX
1. ON CONSIGNMENT OF THE MACHINE
..............................................................................................
1
2. SERIAL NUMBER PLATE
.........................................................................................................................
8
3. INTRODUCTORY COMMENT
..................................................................................................................
9
4. INTENDED USE
.......................................................................................................................................
10
5. SYMBOLS USED ON THE MACHINE
..................................................................................................
14
6. GENERAL SAFETY REGULATIONS
......................................................................................................
17
7. MACHINE PREPARATION
.......................................................................................................................18
8.
TECHNICAL DATA
.................................................................................................................................
24
9. EXPLODED VIEW
...........
......................................................................................................................
24
WARRANTY
................................................................................................................................................
30
2
27.CLEANING THE SQUEEGEE
The careful cleaning of the whole vacuum unit ensures better drying and cleaning of the floor as well
as greater duration of the suction motor. Proceed as follows for cleaning:
1.Slide the suction tube (1) from the squeegee sleeve.
2.Remove the squeegee (2) from the support arm by unscrewing the hand wheel (3).
3.Use a damp cloth to clean the front and rear rubbers, and also clean the vacuum chamber of the
squeegee body
ATTENTION: this operation must be carried out using gloves to protect against
contact with dangerous solutions.
-
Check the rubber edge, if the rubber edge is severely damaged, you can replace a rubber surface.
If the rubber is completely worn, it needs to be replaced. First unscrew the nut (4), remove the
suction cover (5) and then remove the rubber for replacement.
6.Reassemble the vacuum nozzle on the squeegee body
7.After cleaning, replace the squeegee (2) on the initial support, firstly inserting the left pin of the
squeegee in the left slot of the arm, then the right pin in the right slot, being careful to keep the
spring and washer on the plate of the arm. This can be simplified by first
loosening the hand wheel (3) on the pin. Then tighten the Hand wheel (3) to lock the squeegee in
place
8.Insert the squeegee tube in the appropriate sleeve (1).
28.CLEANING THE SOLUTION TANK FILTER
Careful cleaning of the detergent/water solution filter ensures a better working capacity. Proceed as
follows for cleaning:
1.Check the main switch is on “0” (turn it to this position if necessary)
DAILY MAINTENANCE
PERFORM ALL MAINTENANCEOPERATIONS IN SEQUENCE
25.CLEANING THE RECOVERY TANK
1. Disconnect the tube (1) from its seat, unscrew the drainage cap and empty the recovery tank.
2. Press the button (1) to release and rotate the recovery tank
WARNING: Before performing any maintenance, remove the keys from the panel and disconnect the
battery connector of the machine.
ATTENTION: This operation must be carried out using gloves to protect against contact with dange-
rous solutions.
3.Grip the recovery tank and rotate it until the gas spring is resting on the solution tank
4.Remove the vacuum cover and place it in the rear part of the machine
5.Clean and rinse the recovery tank.
6.Replace the cap on the drainage hose, then replace the vacuum cover.
7.Rotate the recovery tank to its standard position
WARNING: Be careful not to hit the recovery tank float directly, as this would
enable water to enter the vacuum motor connected to it.
26.CLEANING THE RECOVERY TANK FLOAT
1.Press the button (1) to release and rotate the recovery tank
2.Grip the recovery tank and rotate it until the gas spring is resting on the solution tank
3. Remove the vacuum cover and place it in the rear part of the machine
Wash the recovery tank.
available for advice or direct intervention.
Intended use
The scrubbing machine is designed exclusively for the professional cleaning of surfaces and floors
in industrial, commercial and public environments. The machine is only suitable for use in closed -
or at least
covered - locations.
The machine is not suitable for use in the rain, or under water jets. It is forbidden to use the machine
for picking up dangerous dusts or inflammable liquids within places with a potentially explosive
atmosphere.
In addition, it is not suitable as a means of transport for people or object
1. SYMBOLS USED ON THE MACHINE
Main switch or key switch symbol
Used on the instrument panel, to indicate the key switch for machine operation on (ON-I) or
off (OFF-0)
Symbol denoting acoustic alarm
Used to indicate the acoustic alarm button
Symbol of the reverse movement selector
Used to indicate the button for engaging the reverse gear
Brush coupling/uncoupling symbol
Used to indicate the button that couples or uncouples the brush
Symbol indicating the maximum temperature of the water used to fill the solution tank
Symbol indicating the position of the solution tank drain pipe
Symbol indicating the position of the recovery tank drain pipe
Indicates the maximum gradient
GENERAL SAFETY REGULATIONS
The regulations below must be carefully followed in order to avoid harm to the operator and damage
to the machine.
WARNING:
Read the labels on the machine carefully. Do not cover them for any reason and replace them
SYMBOLS USED IN THE MANUAL
Open book symbol with an "i"
Indicates the need to consult the instruction manual
Open book symbol
Used to tell the operator to read the manual before using the machine
Warning
symbol
Carefully read the sections marked with this symbol and observe the
indications, for the safety of the operator and the machine
Warning
symbol
Indicates danger of gas exhalation and leakage of corrosive liquids
Warning
symbol
Indicates operator should take safety measures to avoid damage to
limbs.
Warning
symbol
Indicates the danger of fire.
Do not go near with free flames
Warning
symbol
Indicates that the packed product should be handled with suitable lifting
means that comply with the legal requirements
Disposal
symbol
Carefully read the sections marked with this symbol for machine
disposal
On consignment of machine
When the machine is consigned to the customer, an immediate check must be performed to ensure
all the material mentioned in the shipping documents has been received, and also to check the
machine has not suffered damage during transportation. If this is the case, the carrier must ascer-
tain the extent of the damage at once, informing our customer service office. It is only by prompt
action of this type that the missing material can be obtained, and compensation for damage suc-
cessfully claimed.
Introductory comment
FR70 is a floor scrubbing machine which, by means of the mechanical action of the rotating brush
and the chemical action of a water/detergent solution, can clean any type of flooring. As it advan-
ces, it also collects any removed dirt as well as the detergent solution not absorbed by the floor. The
machine must only be used for this purpose. Even the best machines will only work well if used
correctly and kept in good working order.We therefore suggest you read this instruction booklet
carefully and read it again whenever difficulties arise while using the machine. If necessary, remem-
ber that our customer assistance service (organised in collaboration with our dealers) is always
immediately if they become damaged.
-
The machine must be exclusively used by authorised, trained personnel.
-
Do not use the machine on surfaces with an inclination greater than the one shown on the plate.
-
The machine is not suitable for cleaning rough or uneven floors. Do not use the machine on slopes.
-
If the power supply cable of the battery charger is damaged, contact an Authorised service centre
immediately.
-
In the event of danger, quickly press the emergency button on the command panel.
-
For all maintenance interventions, switch off the machine and disconnect the battery connector
and/or the power supply cable.
-
Children must be supervised to ensure they do not play with the device.
-
During the working of the machine, pay attention to other people and especially to children.
-
Only use the brushes supplied with the machine, or those specified in the "CHOOSING AND USING
THE BRUSHES" paragraph of the instruction manual. The use of other brushes could compromise
safety levels.
WARNING
-
The machine is not suitable for use by children and persons with reduced physical, mental and
sensory capabilities, or people who lack experience and knowledge.
-
The machine must not be used or stored outdoors, in damp conditions or directly exposed to rain.
-
The storage temperature must be between -25 and +55 ; do not store outdoors in damp condi-
tions.
-
Conditions of use: room temperature between 0 and 40 with relative humidity between 30 and
95%.
-
The socket for the machine's power cable (electric version) or for the battery charger power cable
(battery version) must be correctly earthed.
-
Adapt the speed to the adhesion conditions.
-
Do not use the machine as a means of transport.
-
The machine does not cause harmful vibrations.
-
Do not use the machine in an explosive atmosphere.
-
Do not vacuum inflammable liquids.
-
Do not use the device to collect dangerous powders.
-
Do not mix different types of detergent as this may produce harmful gases.
-
The machine is not suitable for cleaning carpets.
-
Do not place any liquid containers on the machine.
-
Avoid working with the brushes when the machine is standing still, so as not to damage the floor.
-
In the event of a fire, use a powder extinguisher. Do not use water.
-
Do not knock against shelving or scaffolding, where there is a danger of falling objects. The opera-
tor must always be equipped with the appropriate safety devices (gloves, shoes, helmet, goggles,
etc.).
-The machine is designed to carry out the scrubbing and drying operations simultaneously. Different
operations should only be carried out in areas where the passage of unauthorised persons is prohi-
bited. Signal the presence of damp floors with suitable signs.
-
If the machine does not work properly, check this is not caused by failure to carry out routine
maintenance. Otherwise, ask for intervention of the authorised technical assistance centre.
-
If you need to replace any components, request the ORIGINAL spare parts from an Authorised
dealer and/or Retailer.
-
Restore all electrical connections after any maintenance interventions.
-
Before using the machine, check that all the hatches and covers are positioned as shown in this
Use and Maintenance Manual.
-
Do not remove the guards that can only be removed with the aid of tools, except for maintenance
work (see the relevant paragraphs)
-
Do not wash the machine with direct water jets or with pressurised water, nor with corrosive subs-
tances.
-
To prevent scaling in the solution tank filter, do not fill the tank with detergent solution many hours
before using the machine.
-
Do not use acid or basic solutions that could damage the machine and/or harm people.
-
Have the machine checked by an authorised technical assistance centre every year.
-
When disposing of consumable materials, observe the laws and regulations in force.
-
When your machine has reached the end of its long working life, dispose of the materials it contains
(especially oils, batteries and electronic components) in an appropriate manner, taking into account
that the machine itself was constructed using 100% recyclable materials.
-
The batteries must be removed from the machine before its disposal. The batteries must be dispo-
sed of in a safe manner, fully observing the laws and regulations in force.
MACHINE PREPARATION
1. HANDLING THE PACKAGED MACHINE
The machine is contained in specific packaging with a pallet for the handling with fork trucks. The
packages cannot be placed on top of each other.
The total weight of the machine and packaging is 220 kg
The dimensions of the packaging is as follows: FR70
A: 1230 mm
B: 630 mm
C : 1320 mm
1.Remove the outer package
2. The machine is fixed to the pallet with wedges which block the wheels
3.Disengage the electronic brake, turn the lever (1) (on the rear right-hand side of the machine)
clockwise
4.Remove the wedges
5.Use a chute to get the machine down from the pallet, pushing it backwards. Do not assemble the
rear squeegee before unloading the machine, and avoid violently jolting the brush head. To assem-
ble the squeegee, read the “SSEMBLING THE SQUEEGEE”aragraph
6. Keep the pallet for any future transport needs
ATTENTION: if the product is delivered in cardboard containers, handle the
packed product with suitable lifting means that comply with the legal requirements
WARNING: During this operation, check there are no people or objects near
the machine
2. HOW TO MOVE THE MACHINE
1. Check the solution tank and recovery tank are empty; if necessary, empty them
2. Check that the brush head and squeegee are in the raised position
3. Place it on a pallet using a chute
4. Check that the key switch is in the "0" position and remove the key
5. Secure the machine to the pallet using wooden wedges
6. Engage the electronic brake
3.INSTERUMENT PANEL LWELEMENTS
The instrument panel components are identified as follows:
1. Level indicator for battery/hour meter
2. Horn button
3. Forward or back
4. Automatic install the brush or remove the brush
5. Control water size
6. AUTO automatic mode
7. ECO energy saving mode
4. STEERING COLUMN ELEMENTS
The elements on the left side of the steering column are:
8. Squeegee body lifting lever
9. Brush head body lifting lever
11. Main key switch
5. FOOTBOARD ELEMENTS
The components on the front right part of the foot board are:
12. Drive pedal
13. Emergency button
14. Detergent solution level tube
15. Recovery tank release button
6. SIDE MACHINE ELEMENTS
The elements on the left-hand side of the machine are:
16. Fast filler clean water
17. Water-detergent filler cap
7. REAR MACHINE ELEMENTS
The elements on the rear of the machine are:
19. .Recovery tank cover
20. Blinking light (optional)
21. Recovery tank drain pipe
22. Squeegee suction tube
8. FRONT MACHINE ELEMENTS
The elements on the front of the machine are:
25. Detergent solution filter
26. Detergent tank drainage tap
9. TYPE OF BATTER
To power the machine it is necessary to use:
-
liquid-electrolyte lead traction batteries
-
sealed traction batteries with gas recombination or gel technology.
OTHER TYPES MUST NOT BE USED.
The batteries must meet the requirements laid out in the norms: CEI EN 60254-1:2005-12 (CEI 21-5)
+ CEI
EN 60254-2:2008-06 (CEI 21-7)
For a good operating performance, we suggest the use of four 12V - 100 Ah/C5 battery cases
10. BATTERY MAINTENANCE AND DISPOSAL
For maintenance and recharging, respect the instructions provided by the battery manufacturer.
Particular attention must be paid when choosing the battery charger, if not supplied, since there are
different kinds according to the type and capacity of the battery.
When the battery reaches the end of its working life, it must be disconnected by expert, trained
personnel
then removed from the battery compartment with the aid of suitable lifting devices.
DEAD BATTERIES
ARE CLASSIFIED AS DANGEROUS WASTE AND MUST BE DELIVERED TO THE AUTHORISED
BODIES FOR CORRECT DISPOSAL.
WARNING: You are advised to always wear protective gloves, to avoid the risk
of serious injury to your hands.
WARNING: You are advised to only lift and move the batteries with lifting and
transportation means suitable for the specific weight and size
11.HANDLING - INSERTING BATTERIES
The batteries must be housed in the special compartment beneath the seat carter. They should be
handled using lifting equipment that is suitable in terms of both weight and coupling system. They
must also satisfy the requirements of the CEI 21-5 Standard. The dimensions of the battery com-
partment are: 362mm x 354mm x H290mm.
WARNING:For battery maintenance and daily recharging, you must carefully
follow the instructions provided by the manufacturer or retailer. All installation
and maintenance operations must be carried out by specialised personnel.
WARNING: You are advised to use airtight batteries only, to avoid the leakage
of acids!
WARNING: You are advised to always wear protective gloves, to avoid the risk
of serious injury to your hands.
To insert batteries proceed as follows:
1.Lock the machine by activating the electronic brake, then turn the lever (1) (on the rear right-hand
side of the machine) anticlockwise
2. Make sure the recovery tank is empty, otherwise empty it completely
3.Press the button (2) to release and rotate the recovery tank
4.Grip the recovery tank and rotate it as far as it will go
ATTENTION: You are advised to only lift and move the batteries with lifting and transporta
tion means suitable for the specific weight and size
5.House the batteries in the compartment, positioning the poles “+”and “-”opposite each other
12.BATTERY CONNECTION AND BATTERY CONNECTORS
1.Connect the batteries in series to the "+" and "-" poles using the supplied jumper cable
2. Connect the battery connector cable to the "+" and "-" poles in order to obtain the terminal volta-
ge of
24V
3.Connect the battery connector cable (2) to the machine connector (1)
4.Rotate the seat support until it is in the working position
WARNING: All installation and maintenance operations must be carried out by
expert personnel, trained at the specialized assistance centre
13.BATTERY CHARGER CONNECTION
In order not to cause permanent damage to the batteries, it is essential to avoid their complete
discharge: arrange the recharge within a few minutes of the switching on of the "discharged batte-
ries" blinking light.
WARNING: Never leave the batteries completely discharged, even if the machine is not being
used. Check the battery charger is suitable for the batteries
installed, in terms of both capacity and type.
To connect the battery charger you must:
1.Move the machine near to the battery charger
2. Make sure the recovery tank is empty, otherwise empty it completely
3.Check the key switch is on “0”; if this is not the case, turn the key of the main switch anticlockwise
to “0”
4.Press the button (1) to release and rotate the recovery tank
5.Grip the recovery tank and rotate it as far as it will go
The coupling connector of the battery charger is supplied inside the
bag containing this instruction booklet, and must be fitted to the battery
charger cables as shown in the instructions.
WARNING: This process must be carried out by qualified personnel. An incorrect connection
of the connector may cause problems with machine functioning.
6.Disconnect the electric system connector from the battery connector
7. Connect the battery charger cable to the battery connector
8.Connect the recently wired cable to the external battery charger
WARNING: Carefully read the use and maintenance instructions of the battery charger that is
used for charging.
WARNING: Keep the recovery tank open for the duration of the battery recharging cycle to allow gas
fumes to escape
10. After the charging cycle is complete, the battery connector must be connected to the machine
connector
WARNING: Danger of gas exhalation and leakage of corrosive liquids.
WARNING: Danger of fire: do not go near with free flames
14.FORWARD WORK SPEED
This machine is equipped with electronic traction control. To move the machine, turn the key to “ON
– I” then press the drive pedal (1), adjusting the speed by altering the degree of pressure on the
pedal.
To move the machine backwards, press the button (2) on the instrument panel, then immediately
press the pedal (1). Adjust the speed by altering the degree of pressure on the pedal.
WARNING! The reverse speed is lower than the forward speed to comply with current health and
safety standards.
15. SOLUTION TANK
The recovery tank must be completely empty each time the solution tank is filled. Remove the inlet
cap (1) located on the left side of the machine.
WARNING: The recovery tank must be completely empty each time the solution tank is filled.
Check that the solution filter cap (2), under the solution tank in the front right of the machine, is
properly closed.
Check that the solution tank drainage tap (3) (under the solution tank in the right part of the brush
head body) is well closed.
16.FILLING THE SOLUTION TANK
The solution tank can be filled in two different ways:
1.removing the inlet cap (1) and filling with the aid of a rubber tube
2.using the rubber cap (2); this supports the water hose on its own, but be sure to remove the inlet
cap
(1) to allow the proper vent of air.
Remove the inlet cap (1) and fill with clean water at a temperature of not more than50 . The amount
inside the tank can be seen by means of the level pipe on the front left of the seat. The solution tank
has a maximum capacity of about 65 liters. Add the liquid detergent to the tank in the concentration
and manner indicated on the detergent manufacturer's label. The formation of excess foam could
damage the suction motor, so use only the minimum amount of detergent that is necessary.
WARNING: Always use detergents whose manufacturer's label indicates their suitability for scrub-
bing machines. Do not use acid or alkaline products or solvents without this indication. Acid or
alkaline maintenance detergents can be used, as long as they have pH values between four and ten,
and do not contain oxidising agents, chlorine or bromine formaldehyde, mineral solvents.
WARNING: Protective gloves should always be worn before handling
detergents or acidic or alkaline solutions to avoid serious injury to hands.
ATTENTION: Always use low foam detergent. To avoid the production of
foam, before starting to clean, put a minimum quantity of antifoam liquid into
the recovery tank. Do not use pure acids.
17. RECOVERY TANK
Make sure the recovery tank is empty, otherwise empty it completely.
Check the cap of the drainage tube (1) (on the rear of the machine) is correctly closed.
18.ASSEMBLING THE SQUEEGEE
The squeegee, that for reasons of packaging comes disassembled from the machine, must be
assembled while assembling the machine. Proceed as follows for assembly:
1.Lift the squeegee, turning the left-hand lever (1) to move it clockwise
2.Turn the main switch key anticlockwise to the "0" position
3.Remove the key from the instrument panel
4.Loosen the knobs (2) and (3) in the squeegee pre-assembly
5.(2), making sure the washer and spring adhere in the upper part of the squeegee support
6.knob (3), making sure the washer and spring adhere in the upper part of the squeegee support
7.Insert the suction hose (4) in the squeegee sleeve
ATTENTION: these operations must be carried out using protective gloves to avoid any possible
contact with the edges or tips of metal objects.
19. ADJUSTING THE SQUEEGEE INCLINATION
the squeegee body as follows:
1.Loosen the lock nut (1)
2.Turn the screw (2) clockwise to increase the bend of the rubber in the central part of the squee-
gee.
3.When fully adjusted, fix the lock nut (1)
20.EMPTY SOLUTION TANK DEVICE
To check the quantity of water in the solution tank there is a suitable level indicator tube (1) placed in
front of the driver seat.
WORK
21.WORK
Before beginning to work, it is necessary to:
1.make sure the recovery tank is empty, otherwise empty it completely
2.check the key switch (3) is on “0”; if this is not the case, turn the key of the main switch anticloc-
kwise to “0”
3.connect the battery connector (2) to the electric system connector (1)
4.check the electronic brake (4) is engaged
5.sit on the driver’s seat
6.Turn the key of the main switch a quarter of a rotation clockwise (to position ON). The display on
the nstrument panel will immediately come on.
11.Lower the brush head by turning the right level(6)clockwise, then lower the squeegee turning the
left lever (7) anticlockwise.
WARNING: As soon as the forward movement pedal is activated with the brush head in its work
position, the solenoid valve will start working and will begin dispensing detergent solution. As soon
as the squeegee is in its work position, the vacuum motor will switch on and being working.
12.Press the accelerator pedal (8) to start moving the machine
WARNING: To stop the machine, remove your foot from the accelerator (8). The machine will begin
to stop.
13.To make a reverse movement, press the reverse buttonon the steering wheel simultaneously with
the pedal (8).
WARNING: During reverse movements, the squeegee must be lifted off the floor. To do this, turn the
lever (7) clockwise.
During the first metres, check there is sufficient solution and that the squeegee dries perfectly. The
machine will now begin to work with full efficiency until the battery is flat or until the detergent
solution has finished.
22.OVERFLOW DEVICE
The machine is NOT equipped with an overflow device, because the capacity of the recovery tank is
greater than the capacity of the solution tank. In extraordinary cases, there is a mechanical device
(float) on the lid that, when the recovery tank is full, shuts off the air to the suction motor intake to
protect it; the sound of the vacuum motor will then be deeper. In this case, raise the brush head and
squeegee off the floor by means of the respective knobs on the steering column. After about 15-25
seconds, the vacuum
motor will switch off. Then empty the recovery tank via the drainage hose (1).
It is good practice when restoring the level of the solution tank, to empty the
recovery tank through the special drainage pipe (1).
23.EMERGENCY BUTTON
If there are any problems while you are working, press the emergency button (1) beneath the seat.
This command interrupts the electric circuit between the batteries and the machine system, so the
machine
stops and the electric brake is triggered. To resume work (after resolving the problem), switch off the
key (2), move the button (1) to its standard position, then switch the key (2) back on again.
AT THE END OF WORK
24. AT THE END OF WORK
At the end of the work, and before carrying out any type of maintenance, perform the following
operations:
1.Lift the brush head by turning the right lever (2) anticlockwise, then lift the squeegee turning the
left
lever (3) clockwise. The vacuum motor switches off after a few seconds.
2.Bring the machine to the place provided for draining the water
3.Turn the machine off by turning the key one quarter turn anticlockwise and remove it from the
panel.
WARNING: Before performing any maintenance, remove the keys from the panel and disconnect the
battery connector of the machine.
4.Disconnect the tube (4) from its seat, unscrew the drainage cap and empty the recovery tank.
WARNING:This operation must be carried out using gloves to protect against
contact with dangerous solutions.
5.Slide the suction tube (5) from the squeegee sleeve
6.Remove the squeegee from the support arm (6) by unscrewing the hand wheels (7).
7.Clean well both the squeegee and the rubbers with a jet of water.
8.After cleaning the squeegee and rubbers, replace the squeegee on the initial support, firstly
inserting the left pin of the squeegee in the left slot of the arm, then the right pin in the right slot,
being careful to keep the spring and washer on the plate of the arm. This can be simplified by first
loosening the hand wheel on the pin. Tighten the hand wheel to lock the squeegee in place.
9. Finally insert the squeegee tube in the special sleeve.
10. If you need to empty the solution tank, move the knob downwards
11. Lower the brush head body by means of the relevant lever on the steering column
12.Move the tap (8) outside the brush head body
13.Rotate the tap (8) anticlockwise and wait until the solution tank is empty
14.Close the tap (8) and reposition it on the brush head body
15.Raise the brush head body by means of the relevant lever on the steering column
16.Sit on the driver¡¯s seat
17.Insert the key into the ignition switch and turn it a quarter turn clockwise (to position ON)
18.Park the machine in a closed place, in an area where it cannot cause damage to people or other
property, but also be protected from an accidental fall of objects.
19.Turn the ignition key a quarter turn anticlockwise (OFF position) and remove the key
20.Lift the recovery tank and disconnect the battery connector
ATTENTION: do not leave the machine unattended without first removing the
start-up switch key and applying the parking brake. In addition, do not park the
machine in open places or on sloping floors.
2.Open the filler cap (1)
WARNING: before performing any maintenance, remove
the keys from the panel and disconnect the battery connector
WARNING: these operations must be carried out using gloves to protect against contact with
dangerous solutions.
3.Close the water tap by shifting the relevant knob (on the left part of the steering column) upwards
4.Loosen the filter cap (2) on the front of the machine
5.Remove the internal filter cartridge and rinse everything thoroughly with running water
6.Reassemble all the elements
WEEKLY MAINTENANCE
29.CLEANING THE SUCTION HOSE
Whenever suction seems to be unsatisfactory, check that the suction tube is not obstructed. If
necessary
clean with a jet of water as follows:
1.Make sure the recovery tank is empty, otherwise empty it completely
2.Check the main switch is on “0” (turn it to this position if necessary)
3.Disconnect the suction hose from the squeegee nozzle (1)
WARNING:
This operation must be carried out using gloves to protect against contact with dangerous solu-
tions.
4.Detach the aspiration tube from the seat on the recuperation tank (2)
5.Clean it with a water jet introduced from the side where it is connected to the tank
6.Reassemble all the elements
30. CLEANING THE BRUSH
Thorough cleaning of the brush will guarantee a better working capacity. Proceed as follows for
cleaning:
1.Check the main switch is on “1” (turn it to this position if necessary)
2.Raise the brush head by turning the right-hand lever (1) anticlockwise
3. Press the brush release button (2) on the steering wheel
4.As soon as the button is pressed, you will see the question “RELEASE” on the screen
5.Press the brush release button (2) on the steering wheel again, to confirm
WARNING :During this operation, check there are no people or objects near the brush.
6.Take the brush and clean it under a flowing jet of water
7.Reassemble it on the brush head body
EXTRAORDINARY MAINTENANCE
connector
1.Turn the wing nuts (2) in the horizontal position
2.Remove the front rubber-pressing blades (3)
3.Remove the rubber (4) and replace it
4.To replace the rubber, proceed in reverse order
WARNING: These operations must be carried out using gloves to protect against contact
with dangerous solutions.
TROUBLESHOOTING
31.THE MACHINE DOES NOT START
1.Check that batteries are charged
2.Make sure the electric system connector is connected to the battery connector
3.Check the key switch is ON/I
32.INSUFFICIENT WATER ON THE BRUSHES
1.Check there is water in the solution tank
2.Check that the water/detergent solution release adjustment knob (1) is open
3.Clean the solution filter (2) located at the front of the machine
33. THE SQUEEGEE DOES NOT DRY PERFECTLY
1.Check the squeegee is clean
2.Check the squeegee settings (see “MACHINE PREPARATION”)
3.Clean the entire vacuum unit (see”WEEKLY MAINTENANCE”)
4.Replace the rubbers, if worn
34.THE MACHINE DOES NOT CLEAN WELL
1.Check the state of wear and tear of the brushes and, if necessary, replace them. The brushes
should
be changed when the bristles are about 15 mm long. To replace them, see “REPLACING THE
BRUSHES”, or “DISASSEMBLING THE BRUSHES”and “ASSEMBLING THE BRUSHES”. Working
with over-worn brushes may cause damage to the floor.
2.Use a different kind of brush to the one fitted as standard. For cleaning floors where the dirt is
particularly resistant, we recommend the use of special brushes supplied upon request and accor-
ding
to needs (see “CHOOSING AND USING THE BRUSHES”).
35.EXCESSIVE FOAM PRODUCTION
Check that a low foam detergent has been used. If necessary, add a small quantity of antifoam
liquid to the recovery tank. Remember that, when the floor is not very dirty, more foam is generated.
In this case the detergent solution
36.THE SUCTION MOTOR DOES NOT FUNCTION
1.Check whether the recovery tank is full and, if necessary, empty it
2.Check the float switch on the suction cap (see also “CLEANING THE RECOVERY TANK” in the
paragraph “DAILY MAINTENANCE”)
37.THE BRUSH MOTOR DOES NOT WORK
WARNING: To avoid damaging the floor, the motor only starts up when the machine is moved
forwards
1.Check that the base is lowered during start-up
2.The operator must be properly seated in the driving position
3.Check no thermal protection device has intervened.
4.Check the correct connection of the motor to the terminal under the footboards.
DISPOSAL
To dispose of the machine, take it to a demolition centre or an authorised collection centre.
Before scrapping the machine it is necessary to remove and separate the following materials and
send them to the appropriate collection centres in accordance with the environmental hygiene
regulations currently in force:
brushes
filter
electric and electronic parts*
batteries
plastic parts (tanks and handlebars)
metal parts (levers and frame)
(*) In particular, to scrap the electric and electronic parts, contact your area distributor.
CHOOSING AND USING THE BRUSHES
POLYPROPYLENE BRUSH (PPL)
Used on all types of floors. Good resistance to wear and tear, and hot water (no greater than 60 .
The Polypropylene brush is non-hygroscopic and therefore retains its characteristics even when
working in wet conditions.
NYLON BRUSH
Used on all types of floors. Excellent resistance to wear and tear, and hot water (even over 60 ). The
nylon is hygroscopic and so tends to lose its characteristics over time when working in wet condi-
tions.
ABRASIVE BRUSH
The bristles of this type of brush are charged with highly aggressive abrasives. It is used to clean
very dirty floors. To avoid floor damage, work only with the pressure strictly necessary.
THICKNESS OF THE BRISTLES
Thicker bristles are more rigid and are therefore used on smooth floors or floors with small joints.
On uneven floors or those with deep joints, it is advisable to use softer bristles which can enter the
gaps more easily.
Remember that when the bristles are worn and therefore too short, they will become rigid and are
no longer able to penetrate and clean deep down. In this case, like with over-large bristles, the
brush tends to jump.
PAD HOLDER
The pad holder is recommended for cleaning shiny surfaces. There are two types of pad holder:
1.The traditional pad holder is fitted with a series of anchor points that allow the abrasive floor pad
to be held and dragged while working.
2.The gentre lock type pad holder not only has anchor points, but also a snap-type central locking
system in plastic that allows the abrasive floor pad to be perfectly centred and held without any risk
of it becoming detached. This type of holder is especially suitable for machines with several bruses,
where the centring of the abrasive floor pads is difficult
8. TECHNICAL DATA
Working width: mm 560
Squeegee width: mm 800
Working capacity: 3500
㎡
/ h
Disc brush: No. / Ø mm
1 / 560
Disc brush rotations RPM 200
Brush motor V/W 24/550
Maximum pressure on the brushes KG
23
Traction motor: 24/500 V/W
Traction wheel (number / diameter / width) No. / (Ømm / mm)
2 / (225 / 64)
Maximum forward speed
km/h 0-5.5
Maximum gradient with full load
%
10
Suction vacuum:
No. /(V/W)
1 / (24 / 500)
Solution tank:
Mbar 700
Front elastic wheel (diameter / width) Ømm / mm 175/60
Solution tank L
70
Recovery tank
L
70
Steering diameter
mm
1980
Machine length
mm
1265
Machine length with optional item-holder tray
mm
1320
Machine height
mm
1030
Machine height with optional blinking light kit
mm
1230
Machine width (without squeegee) mm
600
Machine width (without squeegee) with optional tool-holder kit mm
630
Battery compartment(L*W*H)
mm
362x354x290
Rated battery voltage
V/Ah 12/100
Battery weight (max) KG
80
Machine weight (empty and without batteries) 110 Kg
Gross weight in running order (m bat water + operator) 220 Kg
pressure level : 65 dB (A)