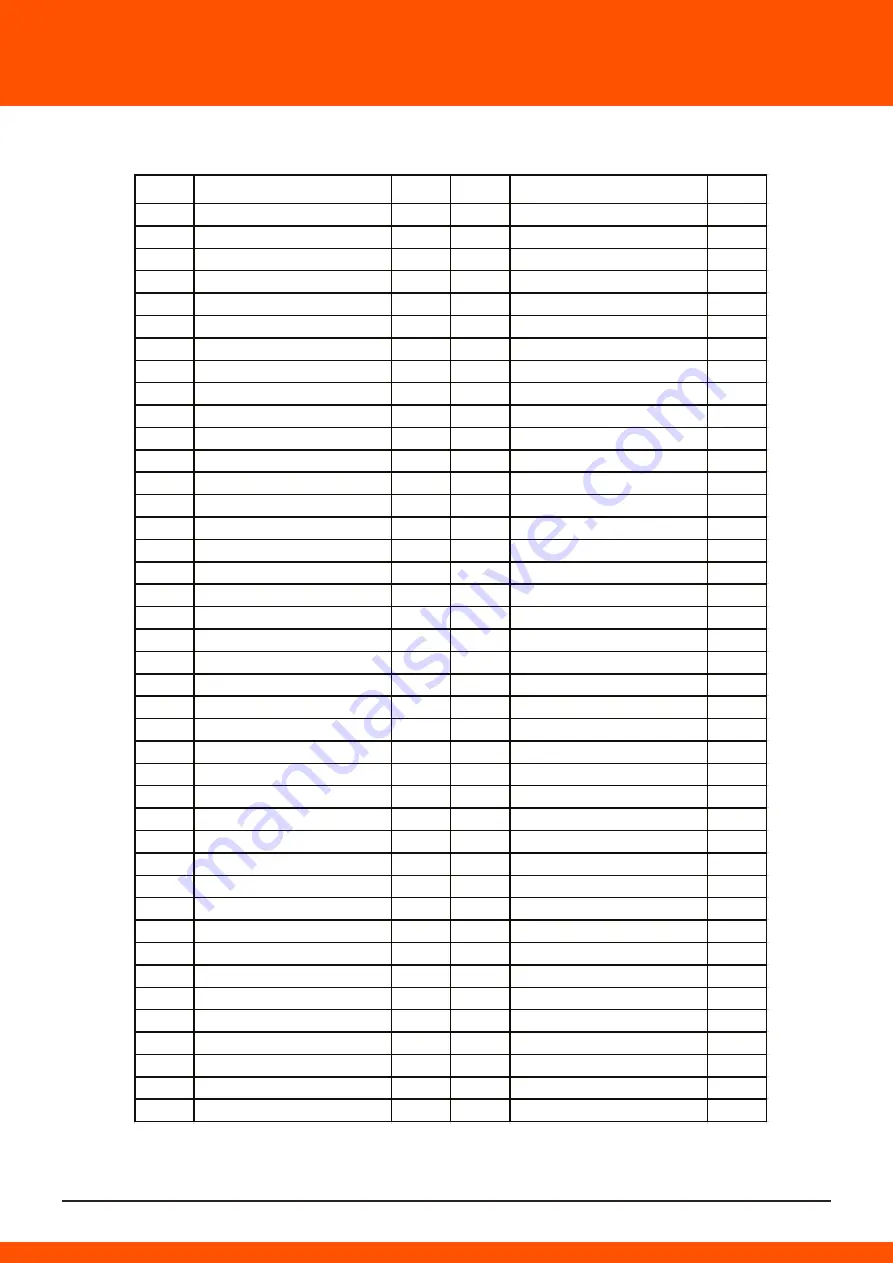
10
READ AND SAVE ALL INSTRUCTIONS FOR FUTURE USE
4. TECHNICAL SPECIFICATIONS
Voltage/Frequency: 220 - 240 V ~ 50 Hz
Power: 1200 W
Speed: 11500-26000 rpm
Working size: 6-8 mm
Functional Description
(
Fig 1&2
)
Your Router has been designed for professional heavy duty routing of wood, wood and plastics
productions.
1. Handle ( left and right )
2. Power
‐
on indicator
3. Carbon brush cap
4. Speed control dial
5. Spindle lock button
6. Collet nut
7. Wing screw for locking parallel guide
5. ASSEMBLY AND ADJUSTMENT
Important: Prior to assembly and adjustment always unplug the tool.
Inserting and removing a bit(Fig.3)
Installing a bit
1. Press and hold down the spindle lock button (5).
2. Using the spanner to loosen the collet nut (6) a few turns and insert a bit
3. Tighten the collet nut (6)and release the spindle lock button(5).
Removing a bit
1. Press and hold down the spindle lock button (5) and using the spanner to loosen the collet nut (6)
completely.
2. Remove the bit.
3. The collet nut screw back.
Note: Never tighten the collet nut without a bit in the collet.
Depth adjustment(Fig.4)
Locate the depth stop (9) on the left
‐
hand side of the router. This continuously adjustable stop is
intended to limit the depth of the cut. Locate the Locking screw for the depth stop (10).
Loosen it by turning it in anticlockwise direction. To move the depth stop up or down to the desired
depth,then tighten the screw.
Locking lever to tighten the heighth of machine body (Fig. 5)
The cutting machine body is spring
‐
tensioned. Take care when releasing the locking lever(13), Grasp
both handles and brace yourself before releasing the lever. Press the housing downwards to the
desire heighth and tighten the locking lever .
When you need to increase the heighth of housing in opposite ways.
CAUTION: The housing of the machine is under spring tension. When you release the locking lever, it
returns to the highest position.
Using the parallel guide (Fig. 6)
The parallel guide can be used for cutting parallel to the edge of the workpiece. Release the three
wing screws and push the parallel guide into the desired distance from the cutter head. Tighten the
three wing screws. Press the guide securely against the edge of the workpiece and execute the cut.
CAUTION: Abnormal vibrations may be due to a blunt cutter head.
Dust extraction outlet (Fig. 7&8)
It is advised to use the dust extraction outlet. You can purchase a suitable commercial
vacuum cleaner or extract the dust via an extractor tube while the cutting machine is in
operation. The outlet must project out of the rear of the machine. Two bolts and nuts are
supplied to attach it. Hold the extractor outlet in position and lay the cutting machine on its side.
Put the screw through the hole of the template guide and router’s baseplate until it projects at the
fastening point for the extractor outlet, Tighten the screw with a suitable screwdriver and moderate
force until the outlet is securely attached. Repeat the procedure at the other side.
CAUTION: Dust may cause respiratory problems. Certain laminated board materials are
carcinogenic. After work, always remove all dust from the machine.
6. OPERATION
Cutting in several operations (Fig. 9)
The length
‐
stop turret(8) can be used to set different depths.
For cutting in depth or in stages, use the length
‐
stop turret as an aid. Using the depth stop(9) with
scale label , set the desired depth to the lowest depth
‐
stop position on the turret. Rotate the turret
so that the highest point is under the depth stop and execute the first cut. Repeat the cut with the
second
‐
highest setting and finally with the last setting. You also can use two positions if the desired
depth can be reached in two operations.
Cutting direction(Fig. 10)
Caution: Always observe the safety instructions and applicable regulations.
Always move your router as indicated (outer edges/inner edges).
To prevent the cutter head from jumping and to obtain a good result, carry out exterior cuts in
anticlockwise and interior cuts in clockwise direction.
NOTE:
-
Check that the bit is correctly installed in the collet.
-
Place the machine on the workpiece before switching on.
-
Select the optimal speed by the speed control dial.
-
Set the cutting depth.
-
For greater cutting depths it is recommended to make shallow cuts.
-
Connect a dust cover.
-
Make sure the lock lever is always locked before switching on
Switching on and off(Fig. 11&12)
1. Connect the plug to the power mains, the power
‐
on indicator is illumed until disconnect from the
power mains.
2. Switch the tool on, keep the lock
‐
off button pressed and press the ON/OFF switch trigger.
3. Switch the tool off, release the ON/OFF switch trigger.
4. Adjust the cutting speed, turn the speed control dial. Position “1” denotes the lowest speed.
Position “6” denotes the highest speed. Turn the dial to increase or decrease the speed. The smaller
the cutter head, the higher the speed. The larger the cutter head, the lower the speed. A cutter head
which runs too fast causes scorching of the workpiece and leaves burnt marks.
CAUTION: Do not change the speed when the machine is working under load. Using the dust
exhaust connection The dust exhaust connection together with an external vacuum cleaner to take
away the dust in dust cover.
If necessary, place an adapter on the dust exhaust.
Checking and replacing the carbon brushes(Fig. 13)
For safety reasons, the machine automatically switches off if the carbon brushes are so worn out
that they no longer have contact with the motor. They must be replaced by a pair similar carbon
brush available through the after
‐
sales service organization or qualified professional person. Loosen
the carbon brush cap anti
‐
clockwise with using a screwdriver, open the cap and remove the old
carbon brushes. If they are 6 mm or less then they must both be replaced. Fit new carbon brushes
and close the cap.
After replaced new carbon brushes, let the machine run with no load for 15 minutes.
CAUTION: The brushes must always be replaced in pairs.
CAUTION: Always disconnect the machine from the power mains before removing any electrical
covers.
7. CLEANING, MAINTENANCE, AND LUBRICATION
1. Before each use, inspect the general condition of the tool. Check for loose
hardware, misalignment or binding of moving parts, cracked or broken parts, damaged electrical
wiring, and any other condition that may affect its safe operation.
2. After Use, wipe external surfaces of the tool with clean cloth.
3. Periodically blow out the motor vent holes with compressed air to prevent the buildup of dust and
particles.
4. Periodically wipe the collet, collet cones, and cutting bits with a light oil to prevent rust.
5. Over time, if the performance of the tool diminishes, or it stops working completely, it may be
necessary to replace the carbon brushes by removing the brush holder cap. This procedure must be
completed by a qualified technician.
6. WARNING! If the supply cord of this power tool is damaged, it must be replaced only by a
qualified service technician.
Caution: Do not use cleaning agents to clean the plastic parts of the tool. A mild detergent on a
damp cloth is recommended. Water must never come into contact with the tool.
Meaning of crossed –out wheeled dustbin:
Do not dispose of electrical appliances as unsorted municipal waste, use separate collection
facilities. Contact you local government for information regarding the collection systems available. If
electrical appliances are disposed of in landfills or dumps, hazardous substances can leak into the
groundwater and get into the food chain, damaging your health and well
‐
being.
No.
Description
Qty
No.
Description
Qty
1
screw ST4.2X16
4
42
spring
1
2
upper cover
1
43
head cover
1
3
screw M4X90
4
44
steel sleeve
Φ
18X
Φ
22X12
3
4
spring washer
Φ
4
5
45
bearing faster nut
1
5
washer
Φ
4
5
46
right handle
1
6
power-on indicator
1
47
cable press plate
1
7
lampshade
1
48
screw ST4.2X12
2
8
housing
1
49
cord &plug
1
9
screw ST4X8
2
50
cord sleeve
1
10
rear cover
1
51
capacitor
1
11
speed control switch
1
52
switch
1
12
nameplate cover
1
53
right handle cover
1
13
brush holder
2
54
front cover
1
14
carbon brush
2
55
spring
1
15
brush holder cap
2
56
lock pin
1
16
brand
1
57
screw M4X14
4
17
stator
1
58
collet
1
18
spring washer
Φ
5
12
59
collet nut
1
19
screw ST4.2X75
2
60
nut
2
20
spring guide rod
1
61
guide rod(short)
1
21
air baffle ring
1
62
pin
Φ
4X17.5
2
22
bearing 608
1
63
guide rod(long)
1
23
armature
1
64
screw M6
1
24
spring
Ⅰ
1
65
turret depth stop
1
25
spring guide axis
1
66
steel ball
Φ
5
1
26
spring
Ⅱ
1
67
spring
1
27
nut
1
68
base
1
28
depth gauge
1
69
screw M6X10
2
29
screw M4X12
1
70
plastic disc
1
30
lever
1
71
screw M4X12
4
31
spring
1
72
screw M5X22
2
32
screw
1
73
nut M5
2
33
screw M4X12
4
74
cleaner adapter
1
34
bearing press plate
1
75
cleaner adapter base
1
35
bearing 6004
1
76
guide rod
2
36
screw ST4.2X16
7
77
bracket
1
37
left handle cover
1
78
guide board
1
38
left handle
1
79
screw M5*12
2
39
screw M5X18
4
80
spanner
1
40
washer
Φ
5
6
81
nameplate
1
41
adjust konb
4