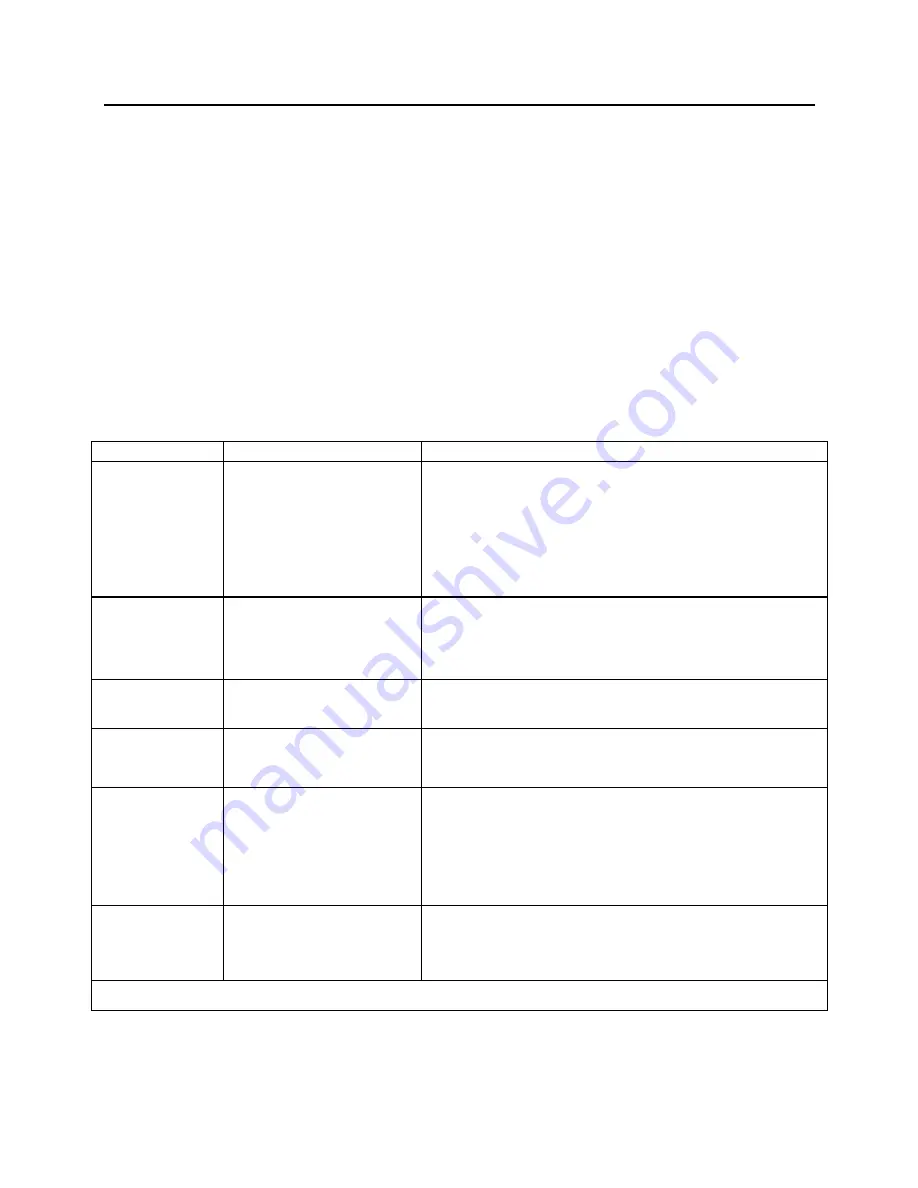
6
Warranty
We make every effort to assure that its products meet high
quality and durability standards, and warrants to the original
purchaser that this product is free from defects in materials
and workmanship for the period of one year from the date of
purchase. This warranty will not apply to damage due
directly or indirectly, to misuse, abuse, negligence or
accidents, repairs or alterations outside our facilities,
criminal activity, improper installation, normal wear and tear,
or to lack of maintenance.
We shall in no event be liable for
death, injuries to persons or property, or for incidental,
contingent, special or consequential damages arising from
the use of our product. Some states do not allow the
exclusion or limitation of incidental or consequential
damages, so the above limitation of exclusion may not apply
to you.
Custom Shop Customer Service contact: (619) 909-2110,
[email protected]
THIS WARRANTY IS EXPRESSLY IN LIEU OF ALL
OTHER WARRANTIES, EXPRESS OR IMPLIED,
INCLUDING THE WARRANTIES OF MERCHANTABILITY
AND FITNESS.
To take advantage of this warranty, the product or part must
be returned to us with transportation charges prepaid. Proof
of purchase date and an explanation of the complaint must
accompany the merchandise. The polisher's serial number
must also be intact. If our inspection verifies the defect, we
will either repair or replace the product at our election or we
may elect to refund the purchase price if we cannot readily
and quickly provide you with a replacement. We will return
repaired products at our expense. If we determine there is
no defect, or that the defect resulted from causes not within
the scope of our warranty, then you must bear the cost of
returning the product. This warranty gives you specific legal
rights and you may also have other rights which varies from
state to state.
Troubleshooting
Problem
Possible Causes
Likely Solutions
Tool will not start.
1. Cord not connected.
2. No power at outlet.
3. Tool’s thermal reset breaker
tripped (if equipped).
4. Internal damage or wear.
(Carbon brushes or switch,
for example.)
1. Check that cord is plugged in.
2. Check power at outlet. If outlet is unpowered, turn off tool and
check circuit breaker. If breaker is tripped, make sure circuit is right
capacity for tool and circuit has no other loads.
3. Turn off tool and allow to cool. Press reset button on tool.
4. Have technician service tool.
Tool operates
slowly.
1. Excess pressure applied to
workpiece.
2. Power being reduced by
long or small diameter
extension cord.
1. Decrease pressure, allow tool to do the work.
2. Eliminate use of extension cord. If an extension cord is needed,
use one with the proper diameter for its length and load. See
Extension Cords
in
GROUNDING
section.
Performance
decreases over
time.
Carbon brushes worn or
damaged.
Have qualified technician replace brushes.
Excessive noise or
ratting
Internal damage or wear.
(Carbon brushes or bearings,
for example.)
Have technician service tool.
Overheating.
1. Forcing tool to work too fast.
2. Blocked motor housing
vents.
3. Motor being strained by long
or small diameter extension
cord.
1. Allow tool to work at its own rate.
2. Wear ANSI-approved safety goggles and NIOSH-approved dust
mask/respirator while blowing dust out of motor using compressed
air.
3. Eliminate use of extension cord. If an extension cord is needed,
use one with the proper diameter for its length and load. See
Extension Cords
in
GROUNDING
section.
Tool does not
sand or polish
effectively.
1. Accessory loose.
2. Accessory damaged, worn
or wrong type for the
material.
1. Confirm accessory arbor is correct and Outer Flange/Arbor Nut is
tight.
2. Check condition and type of disc accessory. Use only proper type
of disc accessory in good condition.
Follow all safety precautions whenever diagnosing or servicing the tool. Disconnect power supply before service.