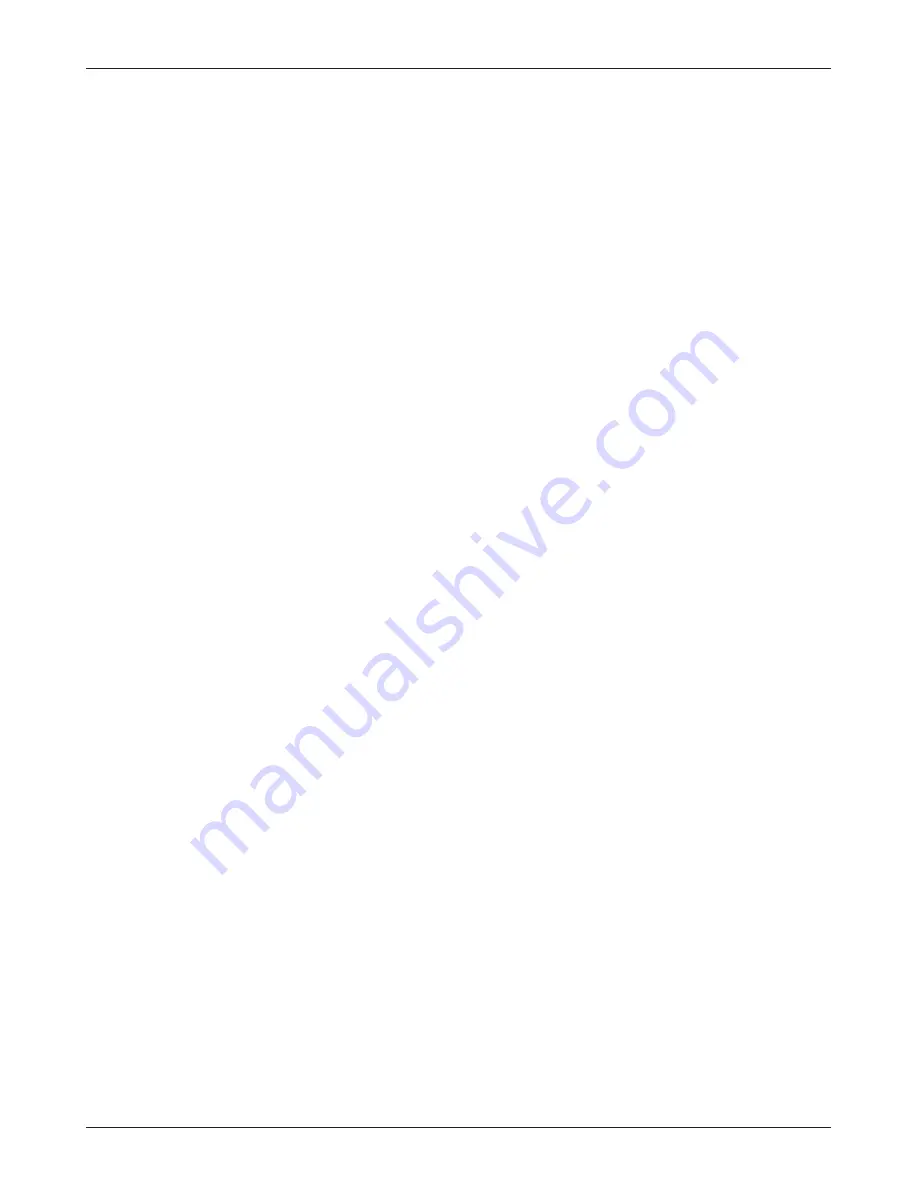
Curtis 1230 Manual,
Rev. C
53
6 — VEHICLE PERFORMANCE ADJUSTMENT
9
Hydraulic system tuning
Tuning the hydraulic system is more straightforward than tuning the drive sys-
tem, because the parameters are not as inter-related. Nonetheless, it is important
that the effect of these programmable parameters be understood; please refer
to the description of the hydraulic parameters on pages 39–41.
If your application does not use a hydraulic throttle (standard wiring
configuration B), it does not need to be tuned; set the Lift/Lower PV Min
values to 0%, the Lift/Lower PV Max values to 100%, and the Lift/Lower Accel
and Decel rates to 0. If your application includes a hydraulic throttle (standard
wiring configuration C), use the following tuning procedure.
9
-a
. Select the appropriate Hydraulic Throttle Type (2 or 4), and then
set the other throttle parameters: Hydraulic Throttle Deadband, Hydraulic
Throttle Max, and Hydraulic Throttle Map. Initially, use these default settings:
DB=10%, throttle max=100%, and map=50%.
9
-b
. Tune the active throttle range. Adjust the deadband and throttle
max settings using the multi-step procedures outlined for their traction throttle
equivalents on page 48.
9
-c
. If variable-speed Lower is desired, set the Variable Lower parameter
to On.
9
-d
. Set the Lift/Lower PV Max and Min values based on the valve
manufacturer’s ratings.
9
-e
. Fine-tune the Lift PV Max and Min values by watching the Prop
Valve PWM value (Monitor >
Outputs
> Prop Valve PWM) while you operate
the throttle. Slowly increase the Lift throttle until the Lift cylinder begins to
rise; use the displayed Prop Valve PWM value for Lift PV Min (Program >
System >
Hydraulics
> Lift PV Min). Push the throttle further until the Lift
speed is no longer increasing; use the displayed Prop Valve PWM value for
Lift PV Max.
9
-f
. Fine-tune the Lower PV Max and Min values using the procedure
described in step 9-e for their Lift equivalents.
9
-g
. To further tune the Lift response, adjust the Lift Accel and Decel
rates. Similarly, to further tune the Lower response, adjust the Lower Accel
and Decel rates.
9
-h
. If a bump is felt at the end of Lift operations, increase the Lift
PV Hold Delay value to allow the hydraulic fluid to stop flowing before the
proportional valve closes.
Note: Once a valve/motor/controller combination has been tuned, the parameter
values can be made standard for that system or vehicle model. Any changes
in the hydraulic system or the controller will require that the system be tuned
again to provide optimum performance.
Содержание MultiMode 1230
Страница 2: ......