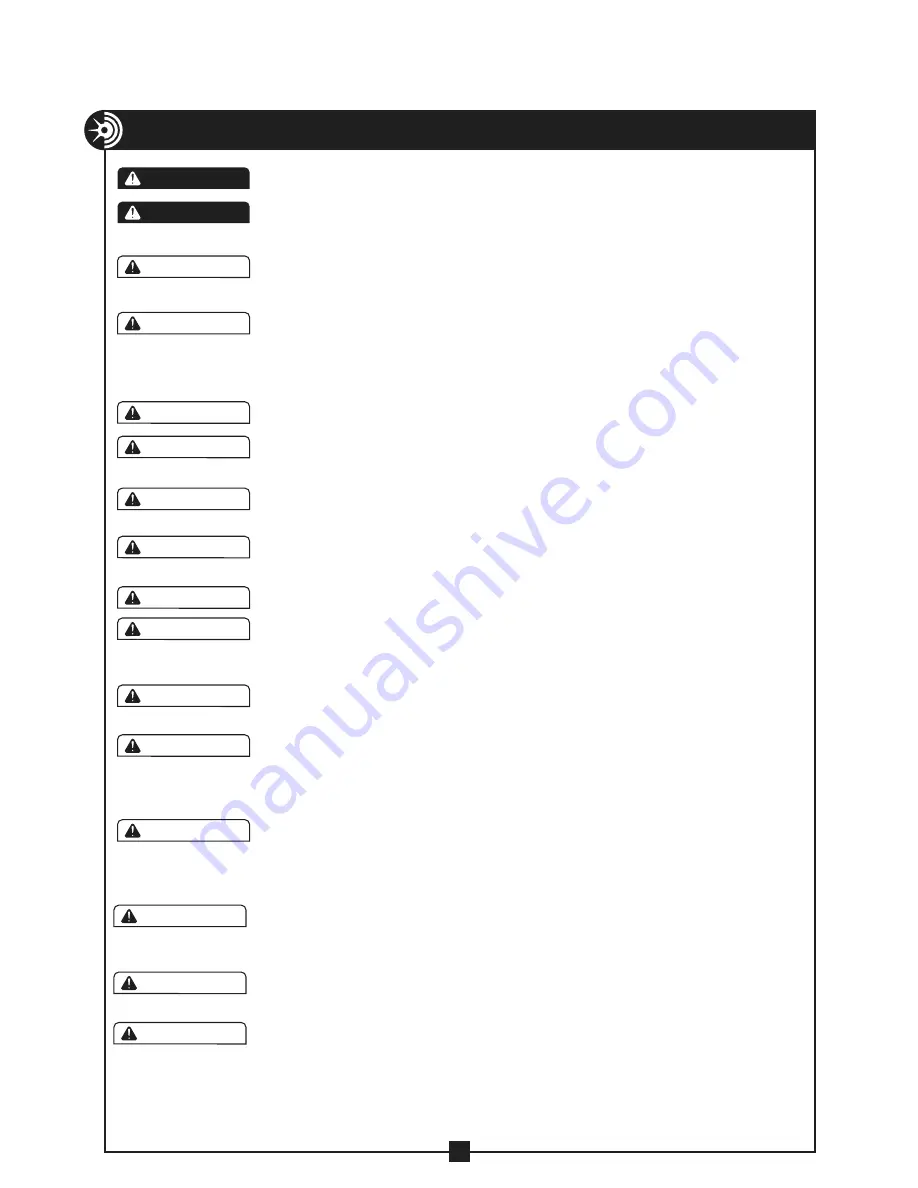
NEVER operate the bender in an explosive atmosphere.
NEVER operate the bender in wet or damp locations.
DO NOT expose the bender to rain.
ALWAYS disconnect the bender from the hydraulic pump before
servicing and when not in use.
ALWAYS inspect the bender before operating. Replace any
damaged, missing or worn parts. Check for alignment of moving
parts, binding of moving parts, breakage of parts and any other
conditions that may affect its operation.
NEVER alter this equipment. Doing so will void the warranty.
ALWAYS keep hands and feet away from pinch points such as
bending shoes, follow bars, saddles, conduit and other moving parts.
ALWAYS use appropriate bending shoe, follow bar and saddle for
the size conduit to be bent.
NEVER allow the carriage with vise to contact any component of
the bender or bending table during a bend.
ALWAYS keep conduit under control when unloading.
ALWAYS keep the path of the bending conduit clear of
obstructions. Make sure all obstacles are clear of the bending
path BEFORE you bend the conduit.
ALWAYS wear approved safety glasses when the bender is
in operation.
ALWAYS wear proper apparel. Do not wear loose clothing, gloves,
neckties, rings, bracelets, or other jewelry which may
get caught in moving parts. Non-slip footwear is recommended.
Wear protective hair covering to contain long hair.
NEVER stand in direct line with the hydraulic cylinder while
operating or servicing the bender. Some parts of the cylinder
are under high pressure and can be propelled with considerable
force.
NEVER stand in direct line with the follow bar while operating the
bender. The follow bar is under high pressure during use and can
be propelled with considerable force.
ALWAYS read and understand the safety and operating instructions
supplied with your hydraulic pump.
ALWAYS keep children away. All visitors should remain a safe
distance from work area.
3
3
IMPORTANT SAFETY INFORMATION
WARNING
DANGER
CAUTION
WARNING
DANGER
CAUTION
WARNING
DANGER
CAUTION
WARNING
DANGER
CAUTION
WARNING
DANGER
CAUTION
WARNING
DANGER
CAUTION
WARNING
DANGER
CAUTION
WARNING
DANGER
CAUTION
WARNING
DANGER
CAUTION
WARNING
DANGER
CAUTION
WARNING
DANGER
CAUTION
WARNING
DANGER
CAUTION
WARNING
DANGER
CAUTION
WARNING
DANGER
CAUTION
WARNING
DANGER
CAUTION
WARNING
DANGER
CAUTION