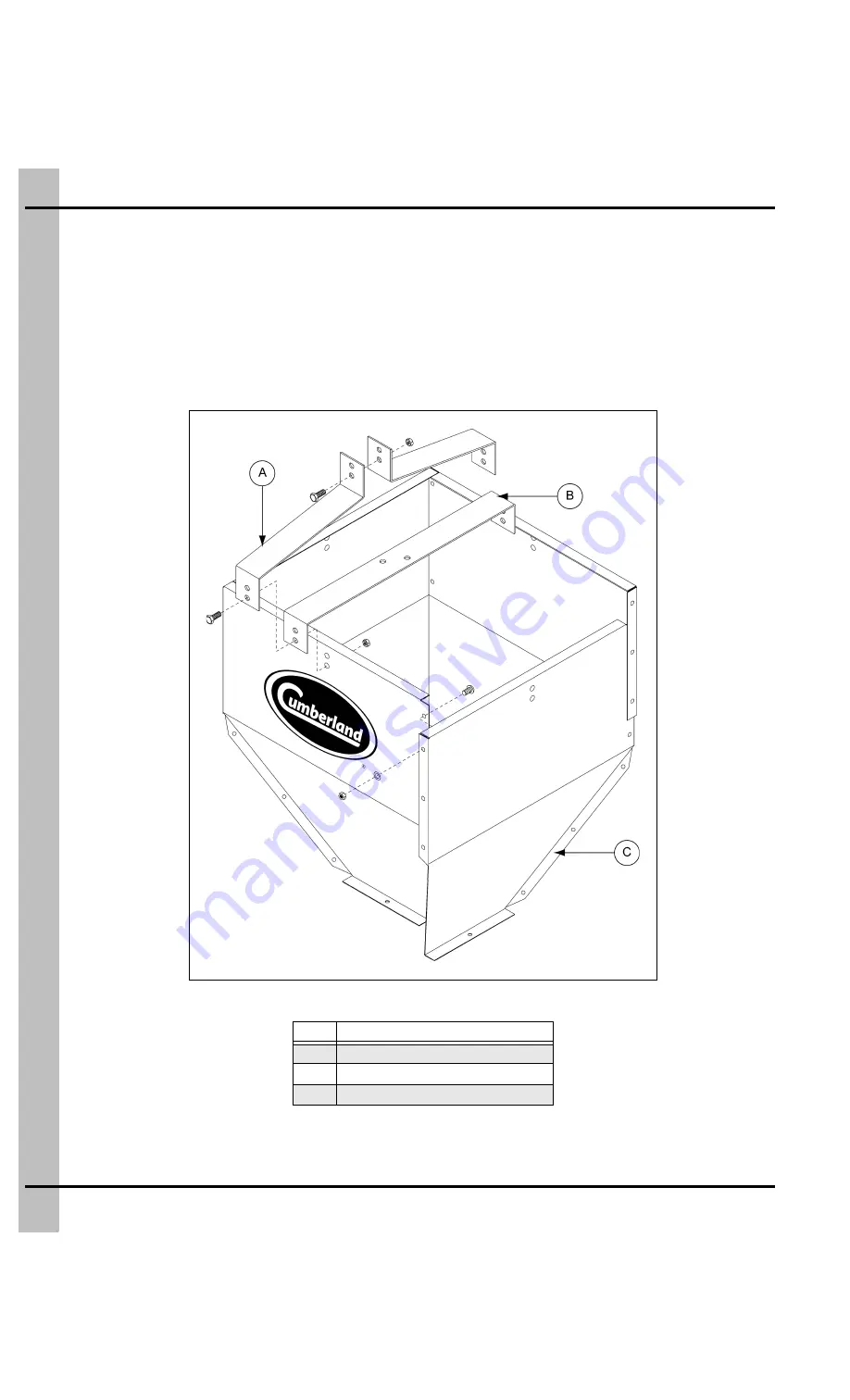
5. Installation
28
PNEG-499
Cycle Plus Pan Feeder
Feed Hopper Assembly
The hopper panels are packaged eight (8) in a box (two (2) hoppers per box). Assemble the hopper panels
with the side flanges on the outside of the hopper. The head of the bolts should be to the inside of the
hopper to help prevent feed from bridging.
Install the hopper brace and hanger brackets in the holes at the top of the hopper. Additional bolts
and nuts are provided to plug the extra holes at the top of the hopper. Use the bottom hole only on the
top of the hanger brackets to bolt them together. The top hole is to be used suspend the hopper with
an ‘‘S-Hook’’.
Figure 5X
Ref #
Description
A
Hanger Bracket
B
Hopper Brace
C
Hopper Panel
Содержание PNEG-499
Страница 1: ...PNEG 499 Cycle Plus Pan Feeder Installation and Operation Manual PNEG 499 Date 01 01 15...
Страница 2: ...2 PNEG 499 Cycle Plus Pan Feeder...
Страница 48: ...48 PNEG 499 Cycle Plus Pan Feeder NOTES...
Страница 52: ...52 PNEG 499 Cycle Plus Pan Feeder NOTES...
Страница 53: ...7 Parts List PNEG 499 Cycle Plus Pan Feeder 53 Grilled Centerhouse Control Unit Components...