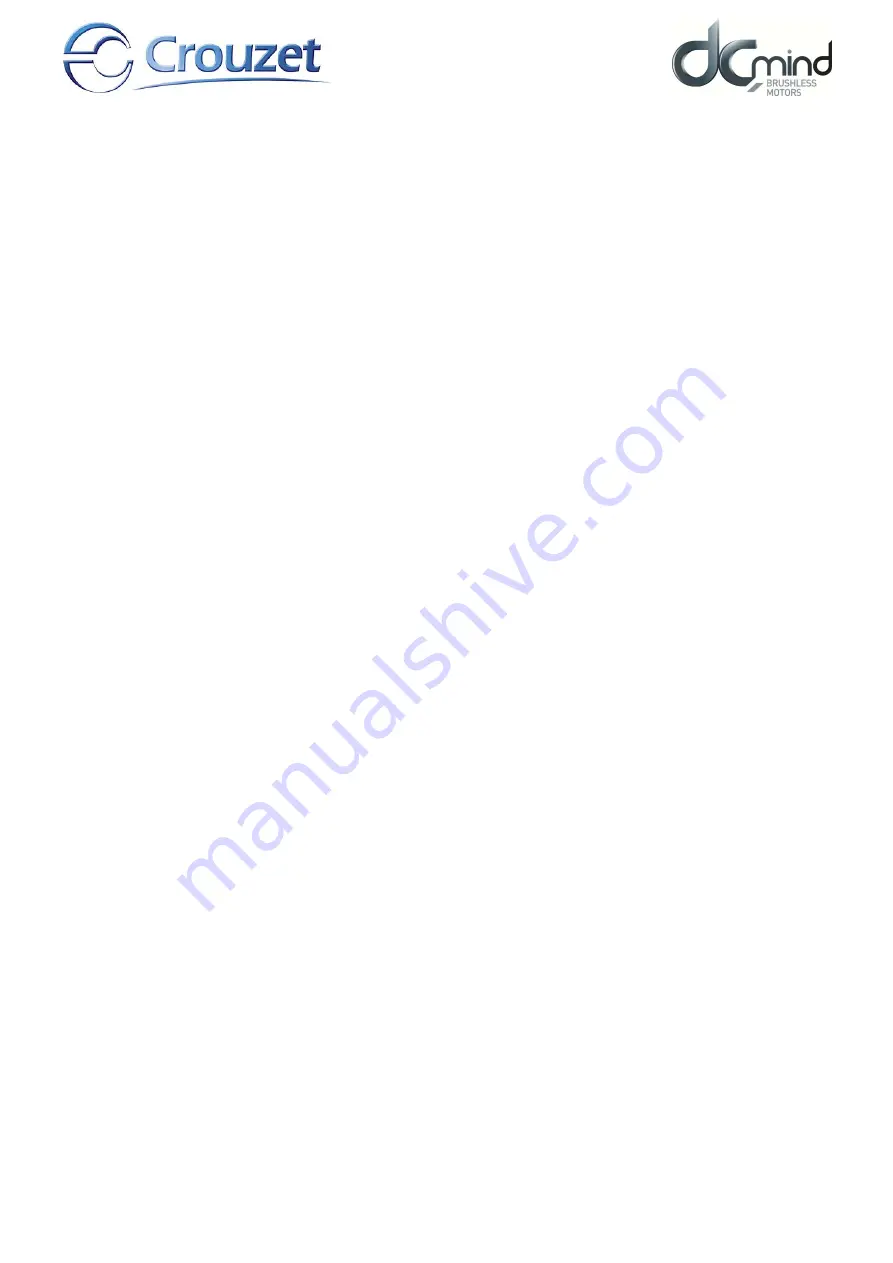
SMI21
162
15.6.
Terminology and Abbreviations
Encoder
Mounted on the motor, the angular position sensor provides frequency pulses proportional to the motor
speed.
Degree of protection
The degree of protection is a standard definition used for electrical equipment that aims to describe the
protection against penetration of solids and liquids inside the motor casing (for example IP54M). The M
indicates that the tests are conducted with the motor running.
This value cannot take account of the seal around the output shaft, for which the installer must take
responsibility.
Axial forces
Longitudinal traction or compression forces affecting the shaft.
Radial forces
Radial forces affecting the shaft.
Direction of rotation
Positive or negative direction of rotation of the motor shaft. The positive direction of rotation is clockwise
rotation of the motor shaft, when looking at the motor from the output shaft.
Nominal speed
Motor speed of rotation when nominal torque is applied.
Nominal current
Current drawn by the motor when nominal torque is applied.
Nominal torque
Maximum applicable torque in continuous duty on the motor shaft.
Firmware
Control software embedded in the motor.
Bootloader
Function available in the HMI which can be used to update the firmware.
Commonly used abbreviations:
HMI:
Human-Machine Interface
SMI21:
Trade name of the new CROUZET brushless range
Homing:
Initialization phase for finding the limits
AON:
Type of digital inputs/outputs (All Or Nothing)
PWM:
Pulse Width Modulation
FWD:
Forward
REV:
Reverse
NO:
Normally Open
NC:
Normally Closed
EMC:
Electromagnetic Compatibility