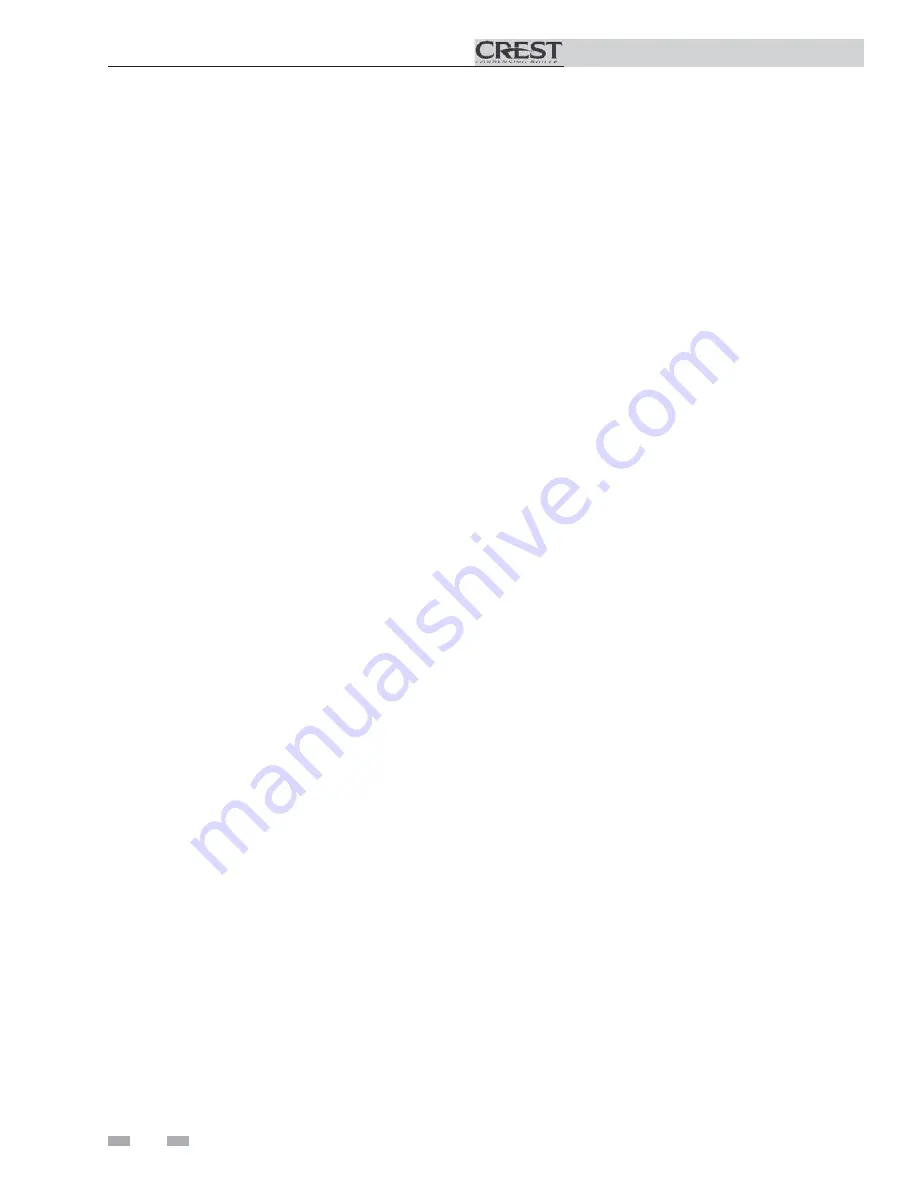
1
Service
Service Manual
22
HWG Rate Limiting
This parameter determines the maximum rate to be used when
heating a HWG tank. This setting may be used when the tank
is unable to accept all of the BTU’s available from the boiler.
This parameter may be adjusted by the installer by accessing
parameter
F10
.
HWG Type
This parameter gives the installer a choice of piping the Hot
Water Generator (HWG) directly to the boiler, or as a zone in
the heating system. This parameter can be adjusted through
parameter
F11
. For direct HWG select
Normal
, for treating the
HWG as a zone, select
Zone
.
HWG System Pump Mode (Type Zone Only)
This parameter allows the installer to determine how the system
pump responds to a HWG call for heat. The parameter can be
adjusted through parameter
F12
. Select
Always Off
if you want
the system pump to always turn off during a HWG call for heat.
Select
Always On
if you want the system pump to always turn
on during a HWG call for heat. Select
Normal
if you want the
system pump to ignore the HWG call for heat and operate based
on the System Pump Mode setting only.
Service Mode Timeout
The Service Mode allows the installer to set the unit to any firing
rate for the purpose of combustion analysis. The delay sets the
length of time the boiler will stay in the Service Mode if no keys
have been pressed before going back to its original state. This
parameter can only be changed by the installer by accessing
parameter
F11
.
Controlling Sensor
The SH controlling sensor parameter selects the sensor the
control will use to regulate the boiler firing rate. This parameter
is adjustable by the installer by accessing parameter
F12
. The
sensor selections are as follows: The outlet sensor regulates the
firing rate based on the outlet water temperature of the boiler
and the inlet sensor regulates the firing rate based on the inlet
water temperature of the boiler. If the outlet sensor is selected,
and the optional system supply sensor is connected, the control
will regulate the firing rate based on the system supply sensor
temperature. If the inlet sensor is selected, and the optional
system return sensor is installed, the control will regulate the
firing rate based on the system return temperature.
Inlet Control Time Delay
When the inlet sensor is selected as the controlling sensor, the
SMART TOUCH control will start by controlling the outlet/
system supply temperature to the SH set point. After a time
delay, the control will start to increase and regulate the system
supply temperature in order to maintain the inlet/system return
temperature to the SH set point. This time delay should be long
enough for the heated water to work its way through the system
loop and be measured by the inlet/system return sensor. This
time delay is adjustable by the installer by accessing parameter
F13
.
Freeze Protection Burner On
If running the pumps does not prevent the inlet
temperature from falling closer to freezing, the SMART
TOUCH control will fire the burner at low fire if in the ON
state. The installer can adjust the temperature at which the
burner fires by adjusting parameter
F4
.
Freeze Protection Burner Differential
Once the burner has started firing due to a low inlet
temperature, the inlet temperature must increase by this
amount before the burner turns back off. The installer can
adjust this differential by accessing parameter
F5
.
HWG/SH Switching Time
When a boiler has a HWG demand and it receives a space
heating demand, the SMART TOUCH control will start
a timer. Once the timer expires, it will stop the HWG
demand and service the space heating demand. This
feature does not apply when the HWG is programmed as a
zone, or in Cascade. The installer can adjust the length of
time the boiler will service the HWG demand by accessing
parameter
F6
.
SH/HWG Switching Time
When a boiler has a space heating demand and it receives
a HWG demand, it will immediately switch to the HWG
demand and start a timer. Once the timer has expired, the
boiler will switch back to the space heating demand and
start another timer. Once this timer expires, it will switch
back to the HWG demand. This feature does not apply
when the HWG is programmed as a zone, or in Cascade.
The installer can adjust the length of time the boiler will
service the space heating demand by accessing parameter
F7
.
Anti-Cycling Time
Once a SH demand has been satisfied, a set amount of time
must elapse before the control will respond to a new SH
demand. The control will block the new heat demand and
anti-cycling will be shown in the display until the time has
elapsed or the water temperature drops below parameter
F9. This parameter can be changed by the installer by
accessing parameter
F8
.
Anti-Cycling Differential
The control will bypass the anti-cycling time if the inlet
water temperature drops too much. The control will use
the inlet water temperature at the time the boiler shut off
as the starting point. If the inlet temperature drops below
this temperature parameter the control will abort anti-
cycling and allow the boiler to fire. This parameter can be
changed by the installer by accessing parameter
F9
.
Содержание FBN0751
Страница 54: ...3 Troubleshooting 54 NOTES...
Страница 55: ...3 Troubleshooting 55 NOTES...