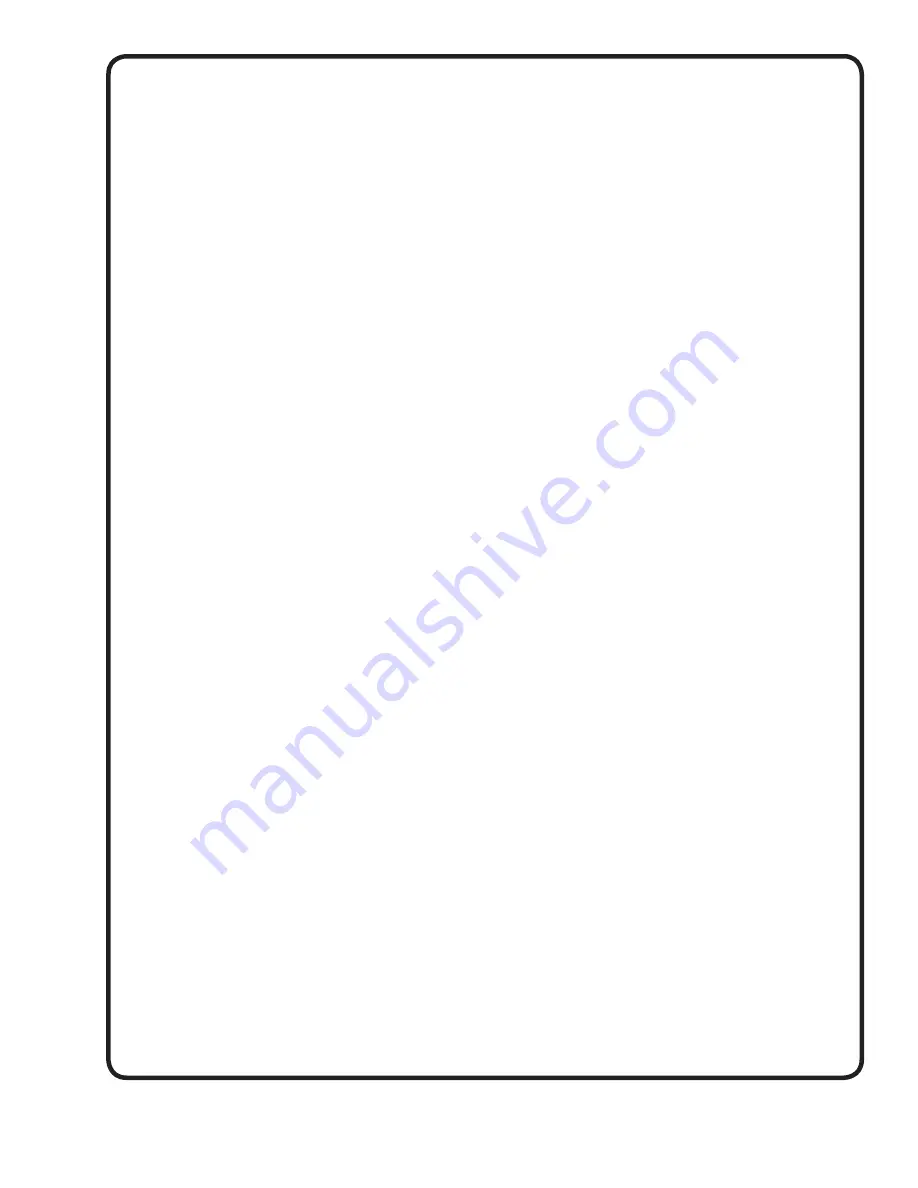
5
D - LUBRICATION
1. Pump should be lubricated with Shell Alvania #2
grease, thru grease fi tting (12) before each day’s
operation.
2. The ball bearings (24) and (26) are of the shielded
type, lubricated by the manufacturer before shipment.
Under normal operating conditions no further lubrication
is required. The lubrication is satisfactory for speeds up
to and including 3600 rpm.
3. Motor bearings should also have periodic attention
and lubrication in accord with motor manufacturers’
recommendations.
4. Under ordinary conditions, a ball bearing will run from
10º to 60ºF (-12º to 16ºC) above surrounding
temperature. Unless the bearing temperature runs above
125ºF (51.6ºC), do not become alarmed.
GENERAL MAINTENANCE AND REPAIR
E - PROPER ADJUSTMENT OF IMPELLER
1. Original impeller adjustment should not be changed until
impeller is worn enough to warrant readjustment. To
reset the impeller:
Remove plug (21) and turn shaft (2) until set screws
(25) in the bearing collar line up with plug hole.
Loosen set screws with hollow head set screw
wrench. Also loosen set screws in the bearing collar
(13). Move shaft (2) toward the pump casing (1) until
impeller (2) touches casing. Move shaft away from
casing until impeller just turns freely without rubbing
casing. Tighten set screws (25) in both bearings, then
turn shaft by hand several times to be certain that it
turns freely. Replace plug (21).
F - PROPER ADJUSTMENT OF STUFFING BOX
1. The liquid being pumped should constantly, yet slowly
drip from the stuffi ng box gland (7) when the pump
is running. This slow drip keeps the shaft and stuffi ng box
packing cooled and lubricated. Tighten gland nuts (17) to
control the required drip. NEVER tighten the gland so as
to entirely stop leakage through stuffi ng box. It increases
the power and wears the shaft in a short time.
G - GENERAL REPAIRS
Whenever it is necessary to dismantle the pump for repairs,
it should be removed from the sub-base. Disconnect the
suction and discharge pipes and remove the four cap
screws holding pump to sub-base. Drain pump by removing
drain plug (4) in the bottom of the pump casing (1).
CLEAN AND INSPECT ALL PARTS
Extreme care should be exercised in keeping the parts
clean. Special precautions should be taken to keep ball
bearings dirt-free while in or out of the pump. The dirt will
damage the ball bearings, thus shortenting the trouble-free
service life of the pump.
Any part which is excessively worn or deteriorated should
be replaced with new parts from factory.
When ordering repairs refer to the illustrations for part
names and the pump name plate on which is stamped
the fi gure number, size and serial number. Without this
information we cannot identify the pump and parts in
question.
H - DISMANTLING
1. Remove casing cap screws (3) and casing (1), also take
off casing gasket (5) which must be kept moist while out
of the pump.
2. Loosen set screw in shaft coupling or pully and remove
from
shaft.
3. Unscrew the cap screws (10) and nuts (17) on the
stuffi ng box gland (7).
4. Loosen the two set screws (25) in the bearing collar (13).
Remove plug (21) and turn shaft until set screws in
bearing (26) line up with plug hole. Loosen both set
screws.
5. Brace support head (11) and tap lightly on end of shaft
(2). Shaft and impeller (2) can now be removed as a
unit.
Stuffi ng box gland (7), packing (8), lantern ring (9),
and packing seat washer (28), may now be removed
from the support head.
6. To remove bearings (24) and (26), remove screws (15)
and bearing cover (14). By pulling on bearing collar (13),
bearing (24) can be removed. Insert a bar into the
coupling end of the support head and push bearing (26)
toward
stuffi ng box.
I - REASSEMBLING
1. Push ball bearing unit which consists of ball bearing
(26) and bearing collar (20) into the support head from
the
stuffi ng box end until fl ush with casting
2. Insert the shaft (2) into the support head and replace
on the shaft the packing seat washer (28), lantern ring
(9),
stuffi ng box gland (7), and slinger (6), After the shaft
is in place, push ball bearing assembly consisting of ball
bearing (24), and thrust bearing collar (13) over shaft into
position.
3. Replace bearing cover (14) and tighten machine screws
(15).