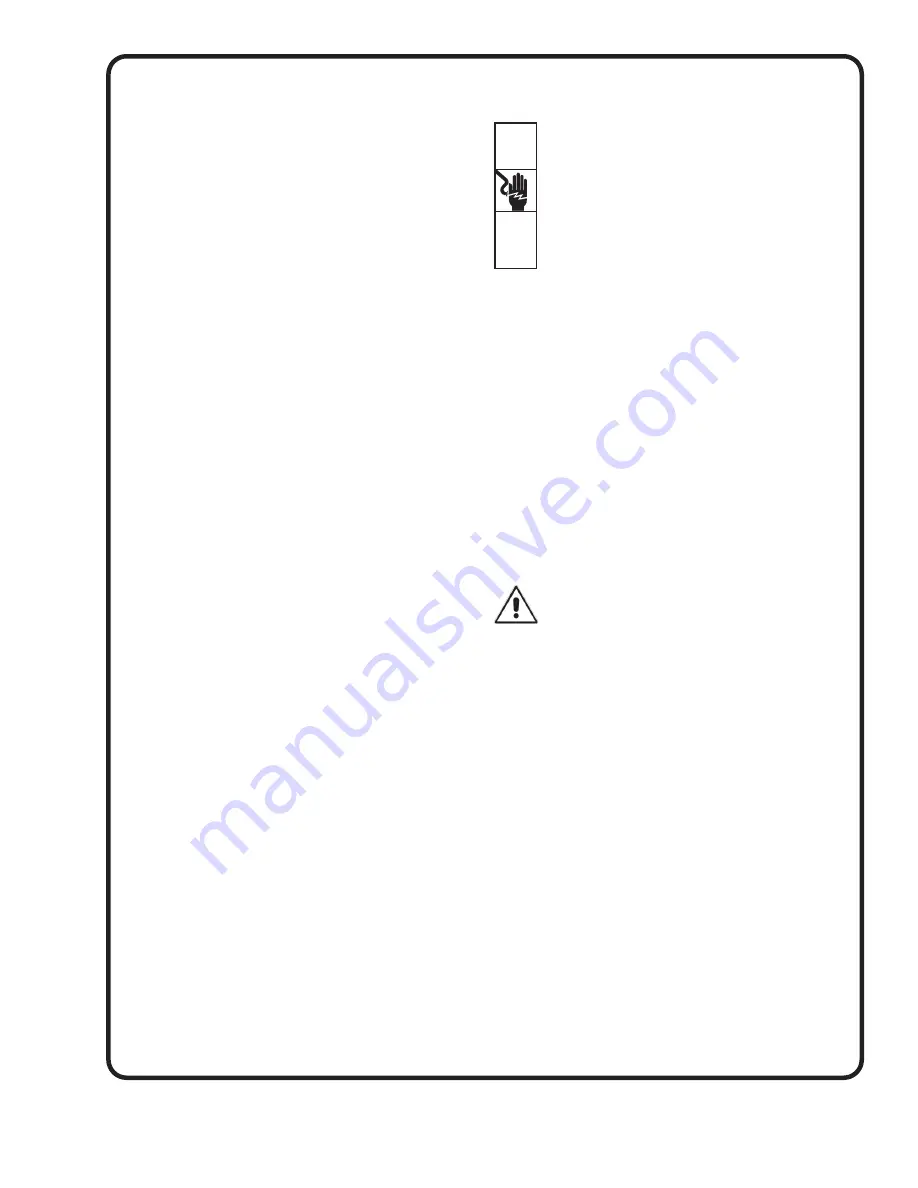
3
GENERAL INFORMATION
To the Purchaser:
Congratulations! You are the owner of one of the finest
pumps on the market today. Burks® Pumps are products
engineered and manufactured of high quality components.
Over eighty years of pump building experience along with a
continuing quality assurance program combine to produce
a pump which will stand up to the toughest pumping
projects.This manual will provide helpful information
concerning installation, maintenance, and proper service
guidelines.
Receiving:
Upon receiving the pump, it should be inspected for
damage or shortages. If damage has occurred, file a claim
immediately with the company that delivered the pump.
If the manual is removed from the crating, do not lose or
misplace.
Storage:
Short Term -
Burks Pumps are manufactured for efficient
performance following long inoperative periods in storage.
For best results, pumps can be retained in storage, as
factory assembled, in a dry atmosphere with constant
temperatures for up to six (6) months.
Long Term -
Any length of time exceeding six (6) months,
but not more than twenty four (24) months. The units
should be stored in a temperature controlled area, a roofed
over walled enclosure that provides protection from the
elements (rain, snow, wind blown dust, etc..), and whose
temperature can be maintained b40 deg. F and
+120 deg. F.
If extended high humidity is expected to be a problem, all
exposed parts should be inspected before storage and all
surfaces that have the paint scratched, damaged, or worn
should be recoated with a water base, air dry enamel paint.
All surfaces should then be sprayed with a rust-inhibiting
oil.
Service Centers:
For the location of the nearest Burks Service Center, check
your Burks representative or Crane Pumps & Systems, Inc.,
in Piqua, Ohio, telephone (937) 778-8947.
INSTALLATION
Pump should be installed in a clean dry area on a solid
surface. It does not necessarily need to be bolted down.
New pipe of proper size to minimize friction losses should
be used on the suction and discharge of the pump. All pipe
joints must be air tight.
Provision must be made in discharge piping to permit
priming.Piping to both suction and discharge of the pump
must be properly supported in order to insure there are no
pipe strains or stresses brought to bear on the pump.
A check valve or foot valve is not necessary in the suction
piping except to maintain the system full of liquid. Where
there is a long, horizontal run in the suction piping, or a
vertical suction lift of 25 feet (15 feet with WPT5, 10 feet
with WT3A, 6 feet with WPT3A) it is advisable to install a
foot valve on the suction pipe.
NOTE: Maximum inlet pressureWTX, WPTX and WSTX
Pumps - 15 PSIWT, WPT and WST Pumps - 100 PSI
WARNING: A faulty motor or wiring can be
a serious electrical shock hazard if it or
surrounding water are accessible to human
contact. To avoid this danger, connect the
motor frame to the power supply grounding
terminal with copper conductor no smaller
than the circuit conductors. In all installations
connect above ground metal plumbing to the
power supply ground per National Code Article
250-80 to prevent electrical shock hazard.
Electrical connections to the motor should be made by
competent electrician. Wiring diagrams shown on the
motor nameplate should be followed for connecting power
supply. Electrical characteristics of supply power must
be the same as that shown on the motor nameplate. A
fuse switch should be installed in the circuit leading to the
pump motor. In wiring 3 phase motors, make sure the shaft
rotation is clockwise when looking at the motor end of the
pump.
OVERLOAD PROTECTION:
All 56 frame, single phase motors, open drip proof, totally
enclosed and explosion proof have built-in overload
protection. All three phase motors must be installed with a
magnectic starter which provides a 3-leg protection for the
motor. Failure to use the correct starter and heater coils
will void warranty.
OPERATION
IMPORTANT Pump Must Be Primed On Initial
Start-Up
Prime the pump by filling the pump case with clean water.
Close disconnect switch to start pump.
MAINTENANCE
LUBRICATION:
No lubrication is required for the liquid end of the pump.
Dual voltage motors, 1/3 thru 3 Hp are equipped with ball
bearings at both ends which are grease packed and sealed
at the factory. No further lubrication is required. 1/3 Hp, 115
Volt only, motors have ball/sleeve bearing construction.
The ball bearing at the pump end requires no lubrication.
The opposite end of the motor has a sleeve type bearing
which may be lubricated periodically by removing the cap
and saturating wick material sith SAE 10 oil.
SHAFT SEAL:
The mechanical shaft seal should be replaced if liquid is
noticed around the motor shaft. Remove case and impeller.
Using two screw drivers to pry on each side, remove seal
stationary seat. Clean seat area of frame, install new
stationary seat with ceramic surface facing out and slide
new rotating element over shaft with hard carbon surface
against ceramic seat. Be sure to keep all surfaces clean.
Lubricating seal parts with water will help the installation
of the seal. Reinstall impeller and pump case.