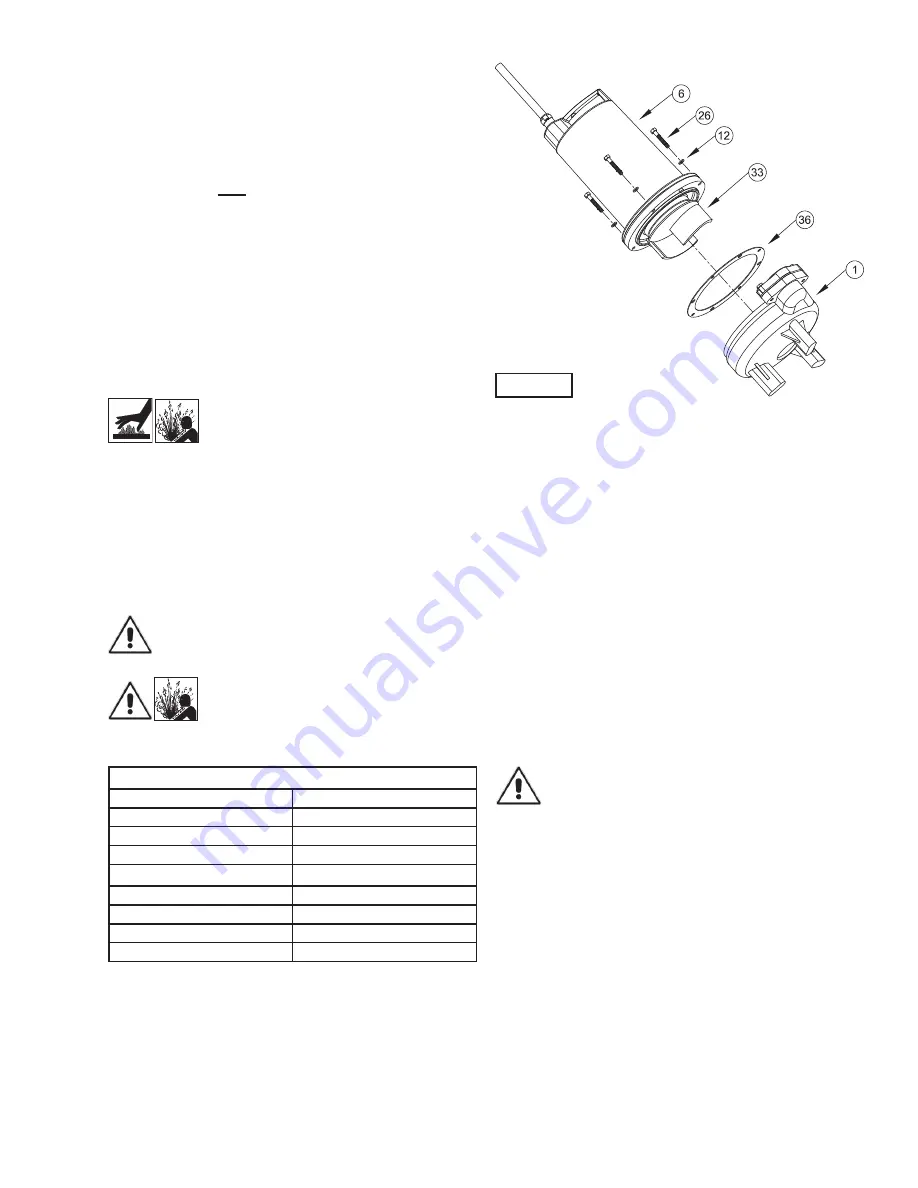
9
Pressurize motor housing to 10 P.S.I. Use soap solution
around the sealed areas and inspect joints for “air bubbles”.
If, after five minutes, the pressure is still holding constant,
and no “bubbles” are observed, slowly bleed the pressure
and remove the gauge assembly. Replace oil as described in
section F-1.4. If the pressure does not hold, then the leak must
be located and repaired.
Pumps that have NOT been disassembled, Motor Housing-
The pressure test may be done with the oil at its normal level.
Remove pipe plug (39) from motor housing (6). Apply pipe
sealant to pressure gauge assembly and tighten into hole
(See Figure 3). Pressurize motor housing to 10 P.S.I. Use soap
solution around the sealed areas above the oil level and inspect
joints for “air bubbles”. For sealed areas below the oil level,
leaks will seep oil. If, after five minutes, the pressure is still
holding constant, and no “bubbles”/oil seepage is observed,
slowly bleed the pressure and remove the gauge assembly. If
the pressure does not hold, then the leak must be located and
repaired.
CAUTION ! Pressure builds up extremely
fast, increase pressure by “tapping” air
nozzle. Too much pressure will damage
seal. DO NOT exceed 10 P.S.I.
F-1.4) Replacing Oil:
Motor Housing-
Set unit upright and refill with new cooling
oil as per Table 1 (see parts list for amount). Fill to just above
motor as an air space must remain in the top of the motor
housing to compensate for oil expansion (see Fig.15). Apply
pipe thread compound to threads of pipe plug (39) then
assemble to motor housing (6).
Important ! - For single phase units, oil level
should be below capacitor
Warning ! - Do not overfill oil. Overfilling of
motor housing with oil can create excessive
and dangerous hydraulic pressure which
can destroy the pump and create a hazard.
Overfilling oil voids warranty.
TABLE 1 - COOLING OIL - Dielectric
SUPPLIER
GRADE
BP
Enerpar SE100
Conoco
Pale Paraffin 22
Mobile
D.T.E. Oil Light
G & G Oil
Circulating 22
Imperial Oil
Voltesso-35
Shell Canada
Transformer-10
Texaco
Diala-Oil-AX
Woco
Premium 100
F-2) Impeller and Volute Service:
F-2.1) Disassembly and Inspection:
To clean out volute (1) or replace impeller (33), disconnect
power, remove hex bolts (26), and lockwasher (12), vertically
lift motor and seal plate assembly from volute (1) see Figure 5.
Clean out body if necessary.
Clean and examine impeller (33), for pitting or wear and replace
if required, inspect gasket (36) and replace if cut or damaged.
If the impeller (33) needs replacing, place a flat screwdriver in
the slot of the end of the shaft to hold the shaft stationary while
unscrewing the jam nut (66) and impeller (33).
F-2.2) Reassembly:
To install impeller (33), clean the threads with thread locking
compound cleaner. Apply removable Loctite® 603 or equivalent
to shaft threads. Screw impeller onto the shaft hand tight
while using a screwdriver in the slot at the end of the shaft
to hold it stationary. Apply thread locking compound (60) to
shaft threads. Then install jam nut (66) and torque to 40 ft.
lbs. It is important that the spring of the lower shaft seal (28)
seats in the hub of the impeller (33). Rotate impeller to check
for binding. Position gasket (36) on volute flange and position
impeller and motor housing on volute (1). Position lockwasher
(12) on cap screw (26) and screw into volute (1). Torque to 100
in-lbs. Check for free rotation of motor and impeller.
F-3) Shaft Seal Service:
Important ! - Handle seal parts with extreme care.
DO NOT scratch or mar lapped surfaces.
F-3.1) Disassembly and Inspection:
Outer Seal -
To expose shaft seal (28) for examination,
disassemble volute and impeller as outlined in paragraph F-
2.1. If further repair is required, remove retaining ring (28d),
spring (28c) and rotating member (28b) from shaft (see Figures
6 & 7). Examine all seal parts and especially contact faces.
Inspect seal for signs of wear such as uneven wear pattern on
stationary members, chips and scratches on either seal face.
DO NOT
interchange seal components, replace the entire
shaft seal (28). If replacing seal, remove stationary (28a) by
prying out with flat screwdriver.
FIGURE 5
Содержание BARNES 3SF-L Series
Страница 14: ...14 FIGURE 15 ...
Страница 15: ...15 FIGURE 16 ...