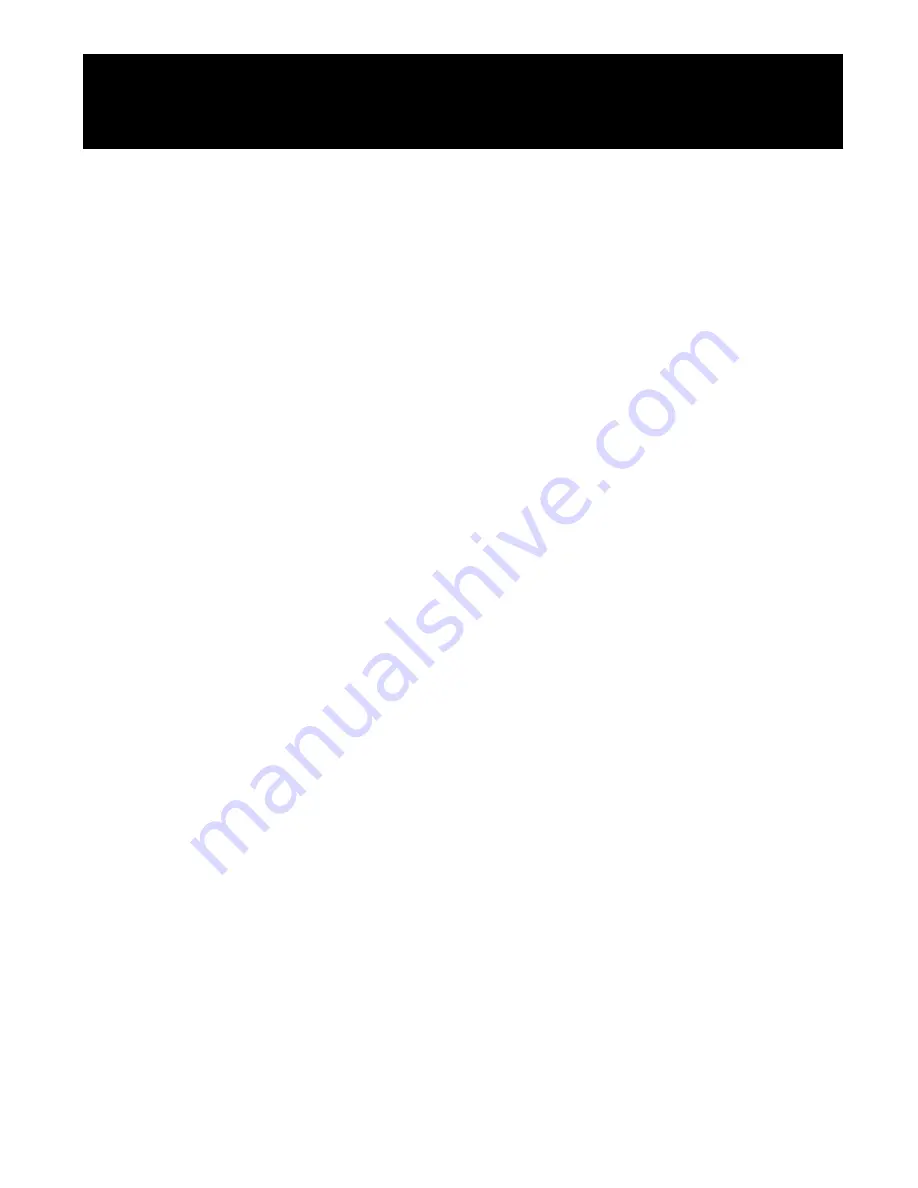
SAFETY FIRST!
PLEASE READ THIS BEFORE INSTALLING
OR OPERATING PUMP.
GENERAL
1. Most accidents can be avoided by using
COMMON SENSE
.
2. Read the operation and maintenance instruction manual supplied with the pump.
3. Do not wear loose clothing that may become entangled in the impeller or other moving parts.
4. Always wear appropriate safety gear, such as safety glasses, when working on the pump or piping.
5. Bronze/brass and bronze/brass fitted pumps may contain lead levels higher than considered safe for potable water
systems. Various government agencies have determined that leaded copper alloys should not be used in potable water
applications. For non-leaded copper alloy materials of construction, please contact factory.
PUMPS
6. Pumps build up heat and pressure during operation-allow time for pumps to cool before handling or servicing.
7. Only qualified personnel should install, operate and repair pump.
8. Keep clear of suction and discharge openings.
DO NOT
insert fingers in pump with power connected.
9. Do not pump hazardous materials (flammable, caustic, etc.) unless the pump is specifically designed and designated to
handle them.
10. Do not block or restrict discharge hose, as discharge hose may whip under pressure.
11. Make sure lifting handles are securely fastened each time before lifting.
12. Do not lift pump by the power cord (if applicable).
13. Do not exceed manufacturers recommendation for maximum performance, as this could cause the motor to overheat.
14. Secure the pump in its operating position so it can not tip over, fall or slide.
15. Keep hands and feet away from impeller when power is connected.
16. Submersible Pumps are not approved for use in swimming pools, recreational water installations, decorative fountains or
any installation where human contact with the pumped fluid is common.
17. Do not operate pump without guards and safety devices in place.
18. When towing pump behind a vehicle; make sure hitch is properly attached, always attach safety chains.
19. Always replace safety devices that have been removed during service or repair.
20. Operation against a closed discharge valve will cause premature bearing and seal failure on any pump, and on end suction
and self priming pump the heat build may cause the generation of steam with resulting dangerous pressures. It is
recommended that a high case temperature switch or pressure relief valve be installed on the pump body.
ELECTRICAL
21. To reduce risk of electrical shock, pump must be properly grounded in accordance with the National Electric Code (NEC),
or Canadian Electrical Code (CEC) and all applicable state, province and local codes and ordinances.
22. To reduce risk of electrical shock, always disconnect the pump from the power source before handling or servicing.
23. Any wiring of pumps should be performed by a qualified electrician.
24. Never operate a pump with a power cord that has frayed or brittle insulation.
25. Cable should be protected at all times to avoid punctures, cut, bruises and abrasions - inspect frequently.
26. Never handle connected power cords with wet hands.
27. Never operate a pump with a plug-in type power cord without a ground fault circuit interrupter.
28. Do not remove cord and strain relief. Do not connect conduit to pump.
29. To reduce risk of electrical shock, all wiring and junction connections should be made per the NEC or CEC and applicable
state or province and local codes. Requirements may vary depending on usage and location. See wiring diagrams in manual.
GAS/DIESEL ENGINE POWER PUMPS & DRIVES ONLY
30. Never operate in an enclosed building or area where exhaust gases can accumulate.
31. Do not breath exhaust fumes when working in the area of the engine. (Exhaust gases are odorless and deadly poison.)
32. Never operate near a building where exhaust gases can seep inside.
33. Never operate in a pit or sump without making provisions for adequate ventilation.
34. Allow exhaust system to cool before touching.
35. Never add fuel to the tank while the engine is running. Stop engine and allow to cool.
36. Do not smoke while refueling the engine.
37. Do not refuel near open flame.
38. Carefully read instruction manuals supplied by engine manufacturer before attempting to assemble, operate or service
the engine or any part. The
"WARNING"
statements indicate potentially hazardous conditions for operator or equipment.
IMPORTANT!
Barnes® Pumps, Inc. is not responsible for losses, injury, or death resulting from a failure to observe these
safety precautions, misuse or abuse of pumps or equipment.
3
Содержание BARNES E Series
Страница 17: ...Fig 9 H Series ONLY E EH Series 17 ...
Страница 18: ...Fig 10 H Series ONLY E EH Series 18 ...