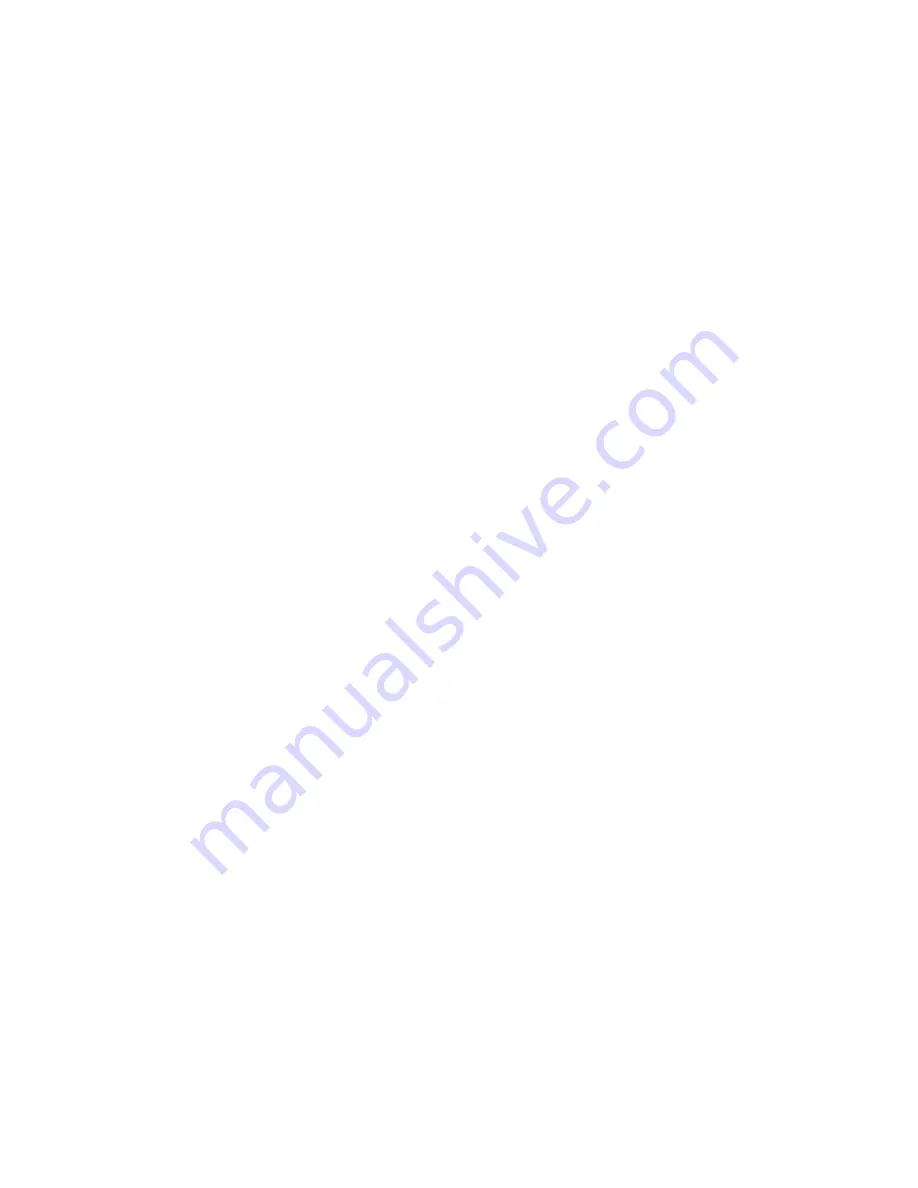
8
r the installation of the
u er, tank, and controls have been completed and
refully checked.
3)
ca
pu
res
4)
5)
6)
7)
op
8)
Cl
ad
sh
AS
OIL
3.
4.
5.
6.
7.
8.
limit “OFF” setting.
,
h
test shall cover the
llowing points: CO2 in the flue gas by analysis, draft,
the flue gas by analysis shall
not be less than 8%.
s
r and not more than 12 inches from the
ion. The stack temperature shall be
m
4)
ex
at
5)
s
6)
In
in
ma
GAS
1.
h
2.
3.
i
4.
5.
Fla
6.
M
.
Adjusting the Burner
– Afte
rn
b
all wiring ca
1)
Leave line switch open and set thermostat well
above room temperature.
2)
Make sure that the resetting device on the control
panel is in operating position.
Set can at gauge port or bleeder tube opening to
tch oil. Close line switch and allow burner to
mp oil until flows clear. If control locks out,
et, and when oil comes out clear, open line
switch and replace plug or gauge.
Close line switch. The burner then should start.
Check oil pressure and adjust, if necessary, to
100 lbs.
Adjust air shutter on burner so that flame burns
clean with slightly smoky tips. Burner is shipped
with air shutter closed.
Start and stop the burner several times by
ening and closing main line switch.
ose main line switch and change thermostat
justment to below room temperature. Burner
ould stop.
G
Size
– The burner shall be adequate size for the
furnace and the connected heating load as
recommended on the gas burner certificate by the
installer. Models and BTU input rating: See “Furnace
Specification” Section.
SEQUENCE OF OPERATION
Thermostat calls for heat.
1.
2.
Protector relay energizes motor and ignition
transformer.
Pump supplies fuel to nozzle.
Burner ignites.
Furnace blower activates at blower “ON” setting.
Area is heated and thermostat is satisfied.
Protector relay de-energizes burner components.
Furnace blower continues to operate until fan
9.
End of cycle.
Certificate
– Following the installation of the burner
certain test data shall be obtained and recorded by the
installer on the gas burner certificate to be placed wit
each gas burner installation. The
fo
stack temperature, firing rate.
Requirements
– The standard requirements as
approved by the industry are as follows:
1)
CO2 – The CO2 in
2)
Draft – The draft shall be in accordance with
specifications in the manufacturer’s installation
manual. An automatic draft regulator or it’
equivalent is required.
3)
Stack Temperature – The stack temperature shall
be measured on the furnace side of automatic draft
regulato
smoke connect
measured at the certified firing rate. If an automatic
draft regulator is built into the furnace, such
regulator shall be closed when the stack
te perature is measured.
Firing Rate – The firing rate shall be based on the
burner manufacturer’s recommendation for the
isting total connected load. Burner shall be fired
that rate.
Smoke – During the above test, there shall be no
vi ible smoke at the chimney.
stallation Manual – The burner shall be installed
accordance with manufacturer’s installation
nual.
T
Burner motor starts and spark ignition begins.
lot valve opens.
ermostat calls for heat.
P
Pilot ignites.
me sensor proves pilot.
ain gas valve is opened
7.
Burner ignites.
8.
Furnace blower activates at blower “ON” limit
setting.
9.
Area is heated and the thermostat is satisfied.
10.
Thermostat de-energizes burner components.
11.
Furnace blower continues to operate until fan
limit “OFF” setting.
12.
End of cycle.
Содержание HO-225
Страница 1: ...Products Commercial Installation Operator s Nov 99 Heating Furnace And Manual...
Страница 10: ...10...
Страница 11: ...11...
Страница 12: ...12...